Using technology to measure – and reduce – carbon emissions
04 August 2023
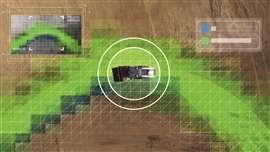
Today’s contractors are under closer scrutiny than ever before when it comes to sustainability, climate change and, specifically, carbon reduction on the job site, particularly on public sector projects. They are often asked to quantify, report and, in some cases, reduce CO2 generated for a given job. However, these metrics can be difficult to come by.
Until now, calculating emissions from heavy equipment has largely been using data including operation time, fuel burned, heat content, and CO2 emission intensity to measure environmental impact. A common underlying assumption is that less time equates to less fuel, with no accounting for startup, idle time and engine speed during operation. Another largely correct assumption is that automation results in improved productivity and a more sustainable outcome. But by how much?
“From a technology development perspective, much of our emphasis to date has been on productivity, for example reducing equipment runtime,” said Dietmar Grimm, Vice President, Corporate Strategy and Sustainability Solutions at Trimble.
“We have not focused on baselining the actual fuel savings that technology provides, which makes it difficult for customers to quantify the actual greenhouse gas reductions realised through our solutions.”
In a recent productivity and sustainability study, Trimble sought to scientifically document the carbon reduction benefits that can be realised using automated solutions, such as horizontal steering control. The two-month study, which focused on a relatively simple soil compaction operation, provided interesting results and has set the course for similar studies across Trimble’s civil construction portfolio.
Methodology
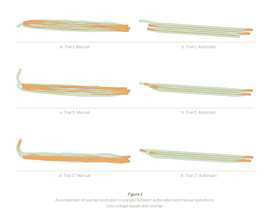
Compaction, or the process of increasing soil density and removing air, is usually done to improve the strength and stiffness of soil. While there are a number of types of compaction machines, including rollers, rammers and vibrating plates, this study focused on rollers.
In any compaction operation, the idea is to minimise under- or over-compaction across a given area. Too little machine overlap leads to gaps or bulges of material at the edges of a pass. Over-compaction can produce unwanted changes in the mechanical properties of the compacted material and decrease productivity and sustainability profiles, unnecessarily increasing fuel consumption, operator hours and resources.
The goal of the study was to quantify the impact of horizontal steering control on compaction overlap and its relationship to overall CO2 emissions.
Compacting conditions
To ensure consistent data for analysis, the study team established the following control variables for the study:
Area to compact: 300 ft x 30 ft (836.127m2)
Operators: skilled and novice
Machine: Dynapac CA2500D compactor with a Cummins QSF3.8 Tier 4 Final engine
A common soil composition
Two randomly selected compactor operators performed the manual and assisted steering operation 20 times, using the same machine and area to perform the compaction for both manual and assisted steering to insure statistical relevance. Of note, the auto assist drive mode path planner was preset to a 15% overlap between consecutive passes.
Recorded observations for both manual and automated functionality included: fuel burn start, fuel burn end, passcount and total time. As well, data extracted from the machines included the location of the compactor drum over time and the target pass counts to achieve desired design specifications.
The data was analysed using the Analysis of Variance analysis tool. It found that using Trimble technologies reduced fuel consumption and duration at a 99.5% confidence level.
A key focus area of the study was measuring productivity, moving and idle time; total compacted area compared to pass counts per hour; and to calculate CO2 emissions in kilograms.
For the derivation of CO2 emissions, the team read fuel values directly from the engine, which addressed any variations in machine RPM – as opposed to assuming a constant nominal value as provided by the manufacturer’s specification. The team also assumed a constant value for the conversion between diesel weight and volume.
Pass counts and percentages
As expected, automatic steering has a noticeable positive effect on relative overlap, reducing expected value and variance.
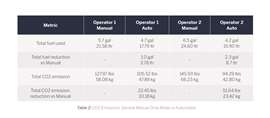
Overlap in the assisted steering mode stayed very close to the preset 15%, while the manual overlap varied from 30-50% between operators. The consistency of overlap in assisted steering mode results in a more predictable outcome and helps to avoid the issues of over- or under-compaction.
Further, operating in assisted mode dramatically reduced the time to complete the compaction operation (by about 25% and 40% for Operators 1 and 2, respectively).
From a sustainability perspective, the numbers were equally impressive. The team tabulated CO2 emission and fuel burned. For estimating CO2 emissions, the study team relied on the following formula: Combusting 1 gallon (3.785 liters) of diesel produces 2.64 kg/l * 3.785 = 9.992 kg ≈ 10.0 kg of CO2.
The cumulative results of all trials (20 automated/20 manual) found that the use of assisted steering in the study led to an average time reduction of 43.8 minutes (29.4%) and an average reduction of fuel consumption of 1.65 gallons (26.46%) compared to manual steering.
Applying these savings to a typical historical compaction job results in significant financial savings.
The potential carbon savings using the average (26.46%), as shown in Table 3, equates to an average saving of 680 gallons (26.46% x 2,569) across the testing scenario, which is equivalent to a carbon savings of over 15,262 pounds.
Similarly, when the time savings are applied against this historical project an impressive savings in labour cost is also realised.
In summary, using automatic steering in the experiment led to considerable time and fuel reduction, as well as significant carbon savings compared to manual steering. Although phase one of the solution is focused on quantifying productivity and sustainability of horizontal steering control for soil compaction, future labs are planned to validate similar findings across the Trimble Earthworks portfolio including machine control for excavators, dozers, and motor graders.
STAY CONNECTED
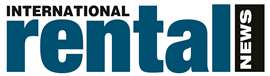


Receive the information you need when you need it through our world-leading magazines, newsletters and daily briefings.
CONNECT WITH THE TEAM
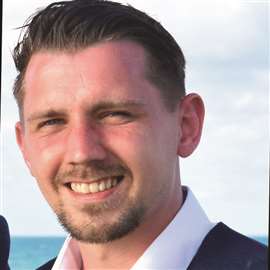
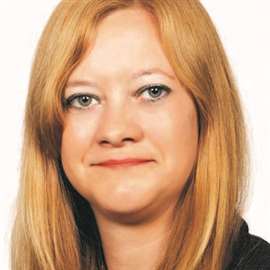
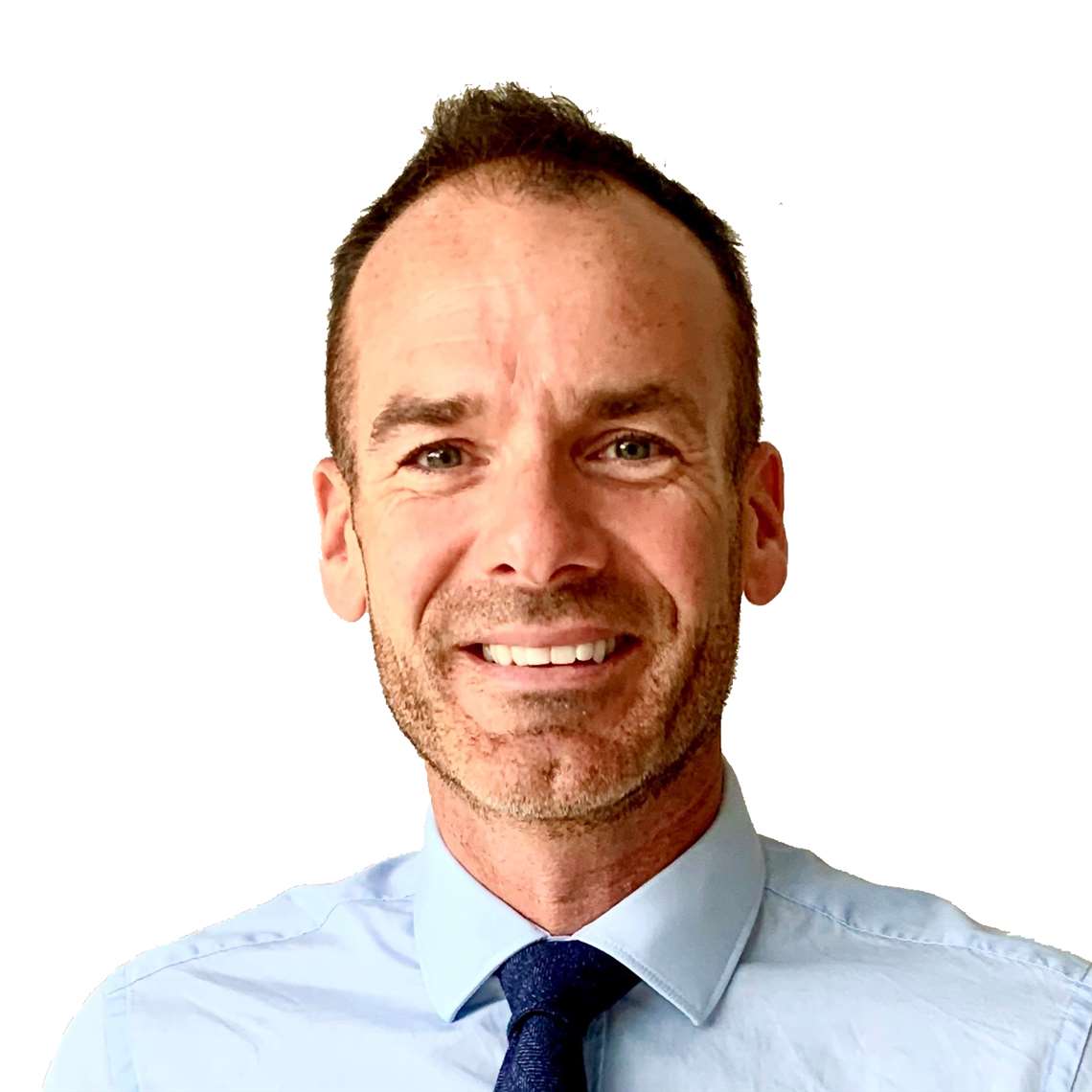