The engineering challenges of Grand Paris Express, Europe’s largest transport infrastructure project
03 July 2023
Part infrastructure upgrade, part social cohesion project, part carbon reduction strategy, the Grand Paris Express, which is scheduled to complete in 2030, will double the size of the Paris Métro. Société du Grand Paris boss, Bernard Cathelain, tells KHL’s Lucy Barnard about the engineering challenges behind Europe’s largest transport infrastructure project
Worming their way in an enormous figure of eight under the French towns and countryside of the Greater Paris area, dozens of enormous tunnel boring machines have been slowly drilling 200 kilometers of underground passages.
The Grand Paris Express is currently Europe’s largest transport infrastructure project and the fourth largest on the planet with an estimated revised cost of €38bn (US$45bn).
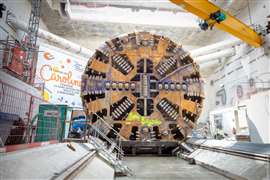
An ambitious plan to connect the chic city of Paris more cohesively with its airports, science hubs and gritty banlieux by building four new lines, 68 new stations and a 14-kilometer viaduct, the project will not only double the size of the French capital’s existing Métro but also aims to connect the outer parts of the city with each other bypassing the need to travel through the centre.
“Grand Paris Express is not only a transport project but a transformation project of the organisation of the Paris metropolis,” says Bernard Cathelain, a board member at the Société du Grand Paris, the public body created to spearhead the construction of the new network.
“It is a metro around Paris which is very important because at the moment our transport system is mainly radial, meaning that if you want to go from one part of the city to another you usually have to travel through the centre and change trains. And the second point is that you have huge differences between the east of Paris, which is usually quite poor compared to the west, which has most of the business areas. So, we expect the project to lessen the inequalities between east and west and to recalibrate the metropolis.”
Re-shaping Paris
Originally launched in 2007 by former president Nicolas Sarkozy but based upon plans to create a bigger and better city which can be traced back to Napoleon III, the concept has been controversial from the very start, criticised for its grandeur and spiralling costs and praised for its emphasis on carbon saving and innovation.
Part infrastructure upgrade, part social cohesion project, part carbon reduction strategy, the project itself is an impressive feat of engineering however you look at it. Tunnelling work started in 2018 and the first part of the project – an extension of the existing Métro line 14 – is due to open in 2024 in time for the Paris Olympics, while four completely new lines will come into service between 2025 and 2030.
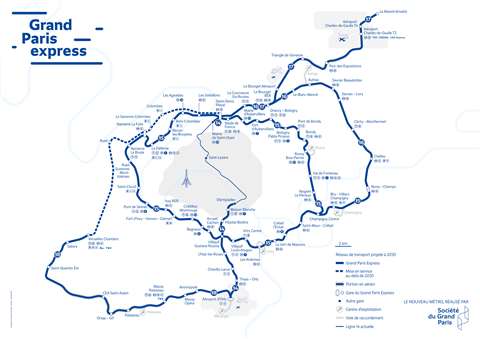
“The size of the project is the first challenge we faced. The scale is completely different to anything we had before in France,” says Cathelain. “Previously in France we had only four TBMs working together throughout all the country. At the height of the works for the Grand Paris Express we had twenty and at the end of the project we will have used thirty. So, we had to find companies which were able to use them to have people working inside these machines.”
Although the world record for the most tunnel boring machines operating simultaneously on a single project goes to the Moscow Metro project which used 23 TBMs, the Paris Grand Express still boasts one of the largest fleets ever used, with 18 procured from German manufacturer Herrenknecht and two from Chinese manufacturer China Railway Engineering Equipment Group. At peak times, Doha Metro, constructed between 2014 and 2016, saw 20 TBMs working simultaneously while 19 machines worked together on the first phase of the Delhi Metro between 1998 and 2006. Construction of the Channel Tunnel in the 1990s was undertaken by a fleet of just eleven.
Construction packages
Despite the length of the completed tunnels, the Société du Grand Paris opted to split construction work on many of the lines into separate construction packages, while the TBM worked on a tunnel section, averaging just 3.5 kilometers each in order to speed up delivery and reduce the amount of time tunnel entrances and access shafts needed to stay open.
“One of the specifics of the projects indeed is we had to coordinate this work,” says Cathelain. “We need to have different companies working together and coordinating during works which is quite specific. The Société du Grand Paris has been created for this purpose. It’s our job to do it. We have a lot of meetings. We have schedules. We are moving the schedules and we have people working on it every day to adjust when unexpected things occur. Almost every day we have to make changes, so we have to adapt every day.”
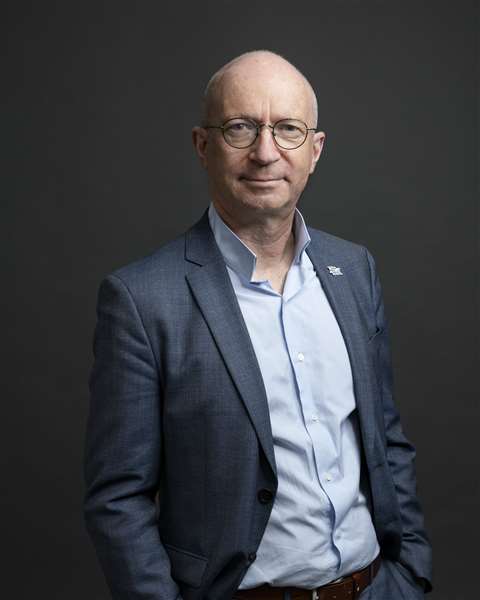
One of the ways in which diverse teams have been able to collaborate on the mega project, Cathelain says, has been through its innovative use of BIM technology. The new metro is one of the first large scale infrastructure projects to use BIM from start to finish with six architecture and civil engineering design firms participating on the project.
Together the teams produced one vast 3D digital model of the entire network covering 12,000 square kilometers, including the surface, geological strata and over a million buildings in and around the project to enable engineers to provide a clear picture showing how each component will interact with each other.
“BIM is very useful because it gives us the possibility to see what the interfaces between different works will be and to organise them,” Cathelain says. “BIM is useful to prepare the coordination during works too but afterwards the coordination is a job for our teams.”
For Cathelain, whose distinguished career includes managing large construction and engineering projects at both Paris Airports and French motorway company SANEF, one of the biggest challenges with creating the new metro is the fact that it is so deep below ground, effectively meaning that each of the 68 new Grand Paris Express stations is a highly complex construction project in its own right.
In order to avoid large amounts of existing utilities infrastructure, to compensate for the hilly topography of the Greater Paris metropolitan area and to enable tunnelling to take place in the city’s stable chalk beds, engineers have had to dig the new metro on average 30 meters below the city – at least twice as deep as the original network, completed at the turn of the twentieth century which averages just 10-15 meters under the surface (although just a fraction of the depths of the world’s deepest metro networks of Kiev, St Petersburg and Pyongyang).
Twice as deep as the original network
Since tunnelling started in 2018, work has been progressing on each of the lines and most of the stations simultaneously with tunnelling contracts awarded in packages to consortia comprising many of the biggest names in French and European construction including Eiffage, Bouygues, Vinci, Webuild, Ferrovial and Trevi.
“It was in the conception to dig deep but it is quite a challenge,” Cathelain says. “It is a challenge for the conception of the stations because we need to make people go so deep to take the metro. So, then we have to build lifts and mechanical escalators to convey them.”
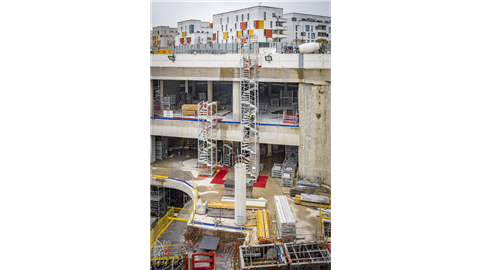
At 52 meters below the surface, Saint Maur – Créteil to the southeast of the city will be both the deepest station on the Grand Paris Express – and the deepest in the whole of France. A consortium led by Eiffage subsidiary Eiffage Génie Civil and Razel-Bec, the civil works division of Fayat Group has been working on the structure which stretches nine storeys below ground level, since 2019.
The station is located on Line 15 South just after a point where the tunnel passes under the River Marne and at a point where it sits underneath the water table in saturated rock. Diaphragm walls form a waterproof station box reaching 72m below the surface while supporting piles are driven 80 meters underground.
“With the river we have water almost everywhere inside the soil so we have to deal with water underground and it could be a difficulty sometimes because we are digging inside water,” says Cathelain. “At the beginning the station is a sort of box with water around so it is just like a boat. It needs to be anchored strongly enough not to have the boat rising up. If it goes wrong, we have water inside the station. It’s quite unpleasant. We had it once, but we dealt with it of course. We have to be very cautious with this.”
In 2021 the consortium completed the excavation work, removing nearly 107,000 cubic meters of rubble from the site before pouring 3,900 cubic meters of concrete to form the base.
Rubble trouble
Cathelain says that one of the biggest problems with digging 200 kilometers of tunnels and 68 multi-storey buildings underneath one of the biggest cities in Western Europe is what to do with all of the earth and rock the project has displaced – 47 million tonnes to be precise.
“We have 47 million tonnes of spoils to deal with and of course, to deal with them or to re-use them each time is quite a big challenge,” Cathelain says. “Each time we need to find the place where the spoils could be sent. We are usually inside one of the most urban parts of the city, so this is not really easy.”
To overcome this, Cathelain says, the Société du Grand Paris launched a competition for community groups and other organisations to come up with innovative uses for the material to meet its aim of re-using 70% of the spoils in local projects. So far, he says the plan has been extremely popular, providing ballast for community projects including new disabled accesses, community spaces and gardens.
Moreover, to keep tabs on what was in the excavated material and where it was used, a sample of each spoil is sent to an independent laboratory for analysis before the spoil is then transported to an appropriate recovery and processing plant. The results are then logged on a specially developed software programme, logging information about each soil sample site and its processing centres.
And reusing the spoils is just one of the ways in which Cathelain says that the Société du Grand Paris is attempting to incorporate innovation into as many elements of the project as possible. In a post-pandemic world with working patterns in flux, passenger numbers falling across many city transport systems and where rapidly evolving technology such as ride hailing apps are already changing urban commuting pattens, he says that the Société is attempting to use innovation as a way of future proofing the network.
A duty to innovate
“Because this is a huge project, we thought that it was our duty to innovate. It is a fantastic opportunity to try new things and to improve the way you do such a project in future,” Cathelain says. “The second reason is that this project is made in quite a short time. We decided on this project in 2010 and it will be under operation for all the lines in 2030 so just 20 years. It is quite a short timeframe for such a project. But it is also quite a long time to decide from the beginning what will be the expectation of the people using it in the future. So, we thought it was necessary to innovate in order to be up to date when the project will be under operation and to be able to adapt during the 100 years when this project will be under operation.”
As a result, the Société du Grand Paris made a bold decision both to create a budget specifically for innovation within the project and to include innovation as one of the categories through which it evaluates commercial tenders, carrying a weighting in some cases of up to 8%. In some cases, the Société also agrees to share any cost savings with the proposer.
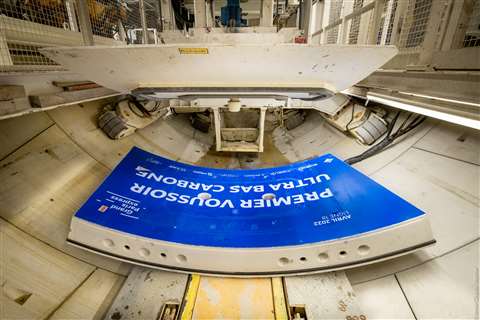
Innovations which have been included as a direct consequence of this strategy include anything from the use of low carbon concrete and steel fibre reinforced concrete to the introduction of a mobile phone app alerting residents in a certain area when specific works were about to start and designing natural ways to regulate the temperature of the network.
Low carbon concrete is one area where the Société du Grand Paris really hopes to capitalise on its investment into innovation. The Société has commissioned research from the Institute Mines-Télécom in Douai, northern France, to investigate methods of flash calcination, where excavated rubble from the project is rapidly cooked and used to replace the carbon-heavy clinker, the main constituent of traditional cement.
The IMT team tested different materials comprising the spoils excavated from line 18 including millstone clay, Beauchamp sand, coarse limestone and backfill to determine the best ingredients for its low carbon cement, eventually selecting millstone clay as the best fit. It then worked on flash calcining the clay and mixing it with several types of concrete to find the best formulation for construction. The team concluded that it was possible to create concrete containing 40% fewer CO2 emissions using soil from the Grand Paris Express site and blast furnace slag. Another team is also currently working on a project to produce low carbon prefabricated concrete elements incorporating 10% Beauchamp sand excavated from construction sites on line 16.
“We decided to pay for the low carbon concrete experiments because we think this is very important,” says Cathelain. “It’s not huge amounts of money but if it is efficient, it will be used in other projects and it could be interesting for the cost of the project later.”
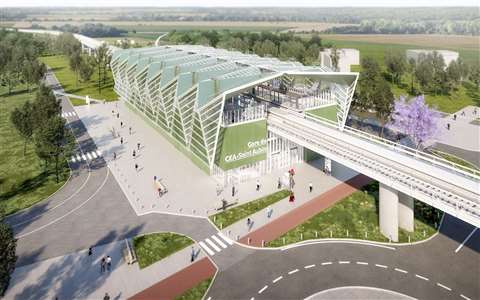
The use of steel fibre reinforced concrete in the project is another innovation in which Cathelain takes great pride. The material, which replaces the metal bars inside reinforced concrete with steel fibres, thus reducing the total amount of steel, is widely used around the world but was difficult to get permission to use in France.
And yet Cathelain says his biggest challenge with the entire construction of the project has not been with any of the innovations or designs of this massive project but rather with ensuring that all contractors working on the project continue to follow strict health and safety rules.
Since construction work started on the mega project in 2018, five workers have been fatally injured in a series of accidents across the network. The most recent, which occurred on April 6, 2023, was the death of 21-year-old Malian Seydou Fofana who was crushed by a concrete block on the future line 17 near Val d’Oise. The deaths prompted the Société du Grand Paris to suspend work on all of its 140 active sites on May 10 in order to hold extra safety training with all employees and to embed a culture of safety.
Changing the culture to ensure worker safety
“Our main concern today is the security of people working on the project,” he says. “Safety is not taken enough into account every day on the works. We have to change the mentality of people. We have to change the culture.”
“What we have started to do is to go directly to the workers and to repeat every day that safety is important and to make them think about safety in every gesture that we are doing in the works,” Cathelain says. “Our big concern is not the schedule or the cost, our biggest concern is the safety of people and the fact that people who are working on this project are going back home safe in the evening.”
Client: Société du Grand Paris, a public agency created in 2010 to oversee the development of the Grand Paris Express. The organisation is 100% state owned and currently employs more than 1,000 people. It is funded through state subsidies, loans and allocated tax revenue. Its management board, appointed by decree of the French president, comprises Bernard Cathelain, Jean-François Monteils and Frédéric Brédillot.
Works: 200 kilometers of track on four new fully automated subway lines (15,16,17 and 18), two line extensions (to lines 11 and 14) 68 new stations added and seven technical centres. 90% of the new lines are being built underground.
Contractors: In order to speed up delivery, the Société du Grand Paris has divided work on the new network into many different packages and awarded contracts to many different consortia. These include. Line 11 extension: NGE Line 14 (Clichy Saint Ouen - Pleyel): Bouygues; (Olympiades - Orly): Vinci; (Pont de Rungis – Orly): Webuild and NGE Line 15 (Noisy-Champs-Villejuif Louis Aragon): Systra; (Villejuif Louis Aragon – Pont de Sevres): Setec; (Fort d’Issy Vanves Clamart – Villejuif Louis Aragon): Vinci; (Noisy Champs – Créteil I’Échat): NGE, Implenia Line 16 (Chelles-Sevran) Webuild and NGE; (Saint Ouen – Aulnay -Le Bourget) Eiffage; (Clicy/Montfermeil – Noisy Champs): Razel-Bec, Sefi-Intrafor and Fayat Metal Line 17 (elevated sections): Consortium led by NGE; (Le Bourget -Gonesse Triangle) Demathieu Bard, Impresa Pizzarotti, Implenia, BAM, Wayss & Freytag Line 18 (St Quentin – Versailles): Consortium led by Ferrovial; (Orly- Massy Palaiseau): Vinci and Spie Batignolles
Costs: Costs estimates for the Grand Paris Express have risen from €19billion in 2010 to €35 billion at present.
Project timings: The first part of the new network, an extension of line 14, is due to open in time for the Paris Olympics in 2024. The remainder of the new network will open in stages and is expected to be fully operational by 2030.
STAY CONNECTED
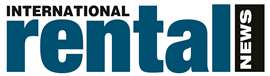


Receive the information you need when you need it through our world-leading magazines, newsletters and daily briefings.
CONNECT WITH THE TEAM
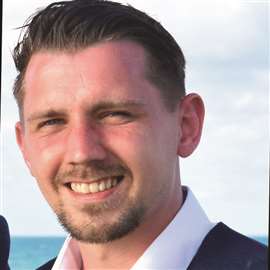
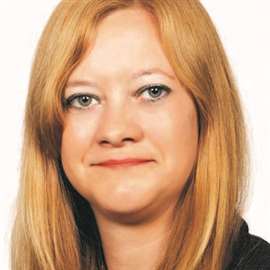
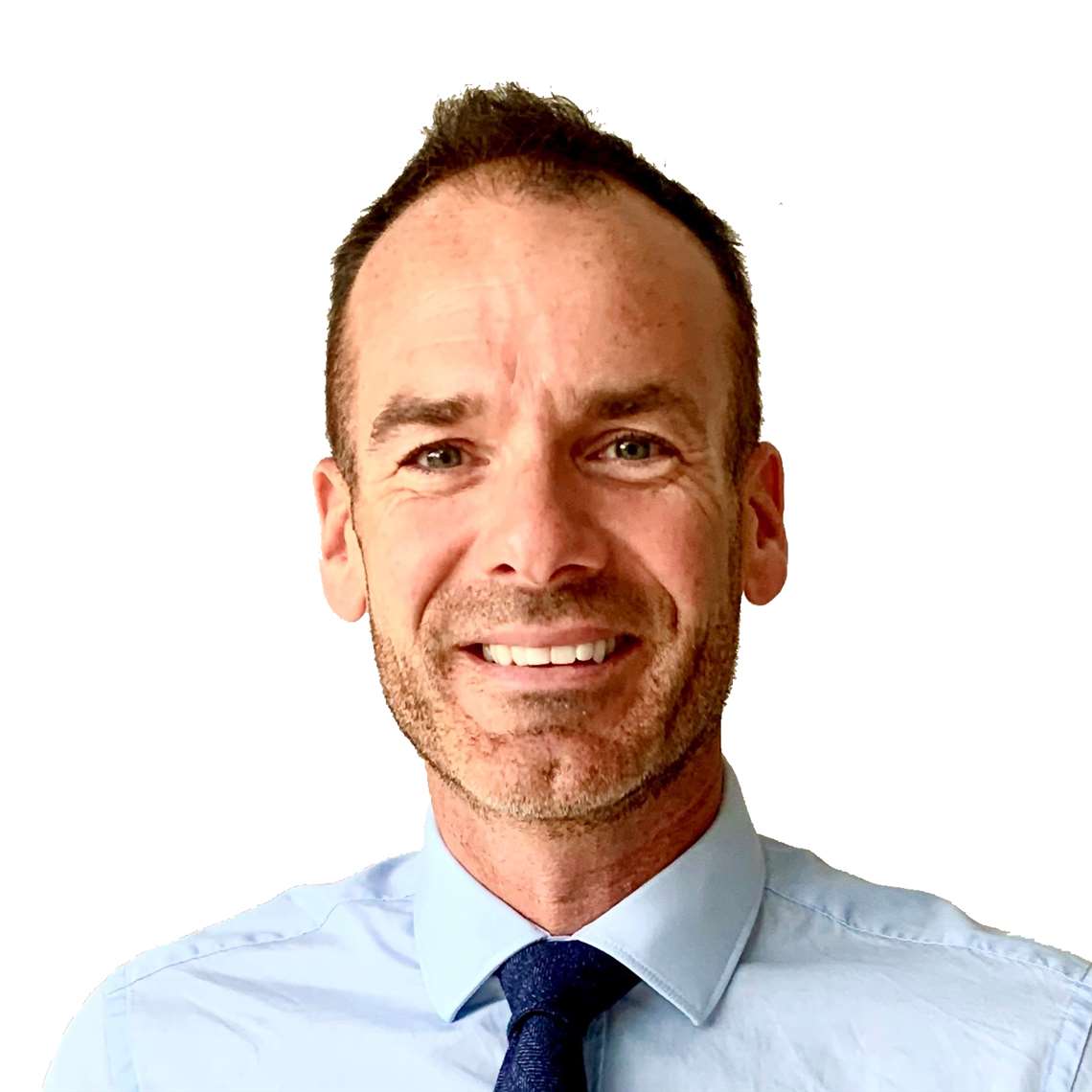