Telescopic boom lifts: electrification and new technologies
21 March 2022
AI delves into the market for telescopic boom lifts and provides a selection of project reports, demonstrating how these products are put to good use.
Larger capacities and working heights, along with electrification and feature enhancing technologies, could be a quote used to sum up the ideal telescopic boom lift product of today, and tomorrow.
Some of those subjects were covered in the Telescopic booms article in the September 2021 issue of AI.
This feature picks up where it left off to find out what’s up next, with much of the latest equipment coming from Chinese manufacturers as they fill out their ranges.
The view from Canadian producer Skyjack is that the telescopic boom market is in positive territory after a pull-back during the early stages of the pandemic.
Corey Connolly, product manager at Skyjack, says, “Demand has bounced back. However, supply chain issues may continue to affect the extent of this growth.”
In the US, in particular, Connolly says, there is a lot of money being spent on various infrastructure and development projects and telescopic booms are a key piece of equipment used on these jobsites.
“They easily navigate tough terrain and the recent trend towards increased capacities when combined with their reach makes them a versatile tool.”
The trend for increased capacities follows the introduction of the ANSI standards in North America.
This was motivated by the introduction of integrated load sensing required by the new standard, meaning machines would now be locked out if overloaded.
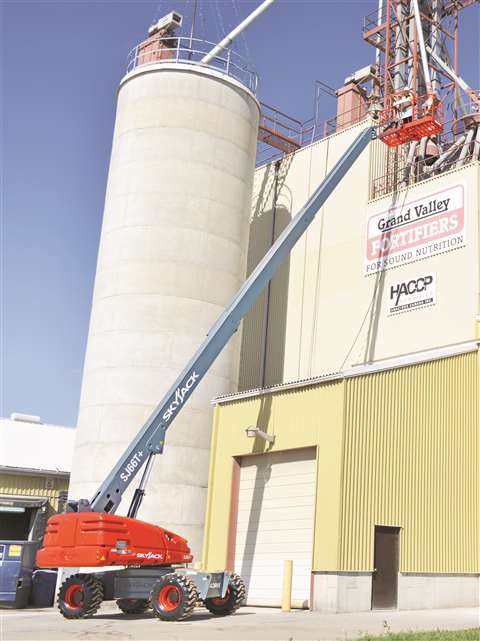
Improved telescopic boom models
Skyjack says it understood that in many applications this would introduce concerns for users and introduced capacities up to 1,000 pounds (454 kg) and three persons in the platform.
As such, over the past year, Skyjack has made a number of improvements to its SJ45 T and SJ66 T telescopic boom lifts, the biggest being to its control system, powertrain and platform capacities.
The enhancements Skyjack made to its control system benefit its Elevate telematics option, providing access to additional data points to better understand machine usage.
Updates to Skyjack’s power train were specific to the SJ45 T+. Connolly says, “After analysing machine usage and consulting with a number of its customers, Skyjack identified an opportunity to utilise a 18.5kw engine.
“In conjunction with its ECOstart anti-idling option, this change will reduce fuel usage up to 40%.”
Expanding on market sentiments for telescopic boom lifts, Haulotte is not planning on launching a new product in the foreseeable future, nevertheless, it says, the market for telescopic booms has grown by 14% in the last five years.
However, most of that growth is coming from China, without which the market trend is flatter and slightly in the negative at around -2% over the same period.
Models with expanded versatility and greater capacity are also being joined by more compact units on the market.
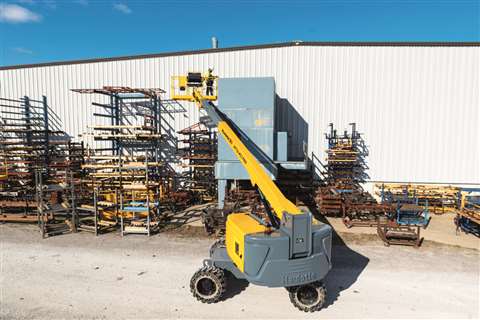
In June 2020, Haulotte presented the HT16 RTJ, designed for working in challenging environments and tackling demanding projects.
The diesel-powered HT16 RTJ O/Pro (HT46 RTJ O/Pro in North America) offers a basket capacity of 250kg and has a dual load option increasing the basket capacity to 350kg.
Its mechanical axle drive allows for the use of a smaller 18.5 kW, simpler engine, while maintaining the same performances as other RTJ booms in the range.
On the other end of the working height spectrum, Snorkel’s 2100SJ mega boom, which it launched as the world’s largest boom lift at ConExpo in 2020, is being used as a benchmark for the company’s future products.
The company is currently focused on delivering the first 2100SJ units and completing the global roll-out of its new dual capacity mid-size telescopic booms, which it launched last year.
[See the September feature for more details about the mid-sized booms].
The influence of the 2100SJ will come into play with the redesign of its large telescopic boom family, ranging from 80ft - 150ft.
Included in those new designs will be some of the new features developed for the 2100SJ, which boasts a 66m working height and an outreach up to 35.1m.
Patent pending technology
Some of those innovations include a static axle mechanism that allows the axles to be extended while the lift is standing still.
The use of the wheel motors, rather than cylinders, drives the axles into their extended position to minimise the risk of tyre scrub on the ground. The automatic chassis extension is activated by a single toggle switch.
The model also has five-steering modes, including lateral steer which enables the lift to be driven side-to-side along a building with the wheels in a 90° position, the unit is able to navigate confined spaces with a 2.6m inside turning radius.
Automatic traction control locks the four wheels together to create a four-wheel drive, while closed loop hydraulics provide a smooth driving experience.
Equipped with a 189 liter steel fuel tank, the 2100SJ has an electric fuel gauge, similar to cars, plus a manual gauge.
It also has a range of patent-pending design features, including a secondary control pendant in the platform so that the operator can face the direction of travel for precise positioning at height.
The boom assembly has 40% less moving parts than the current industry standard, says Snorkel, meaning less complexity and spare parts from a service and maintenance perspective, and increased reliability.
For increased operator safety, the company has added haptics to its upper controls. This provides the operator with a joystick vibration experience that becomes proportionally stronger to warn the operator as they near the boundaries of the working envelope.
Genie says it will have some exciting news coming soon about an addition to its telescopic boom lift lineup.
Simone Manci, booms application engineer for Genie, says the company is not ready to talk about it yet.
In terms of industry trends, Manci says electrification is near the top end of features that customers are interested in, and where the industry is heading.
“This is the case across product lines as the industry moves toward equipment that can meet demand for both performance and sustainability.”
As Manci confirms, hybrid and electric technologies are not new but says the pace of adoption is accelerating as several factors come together.
“Demand is increasing globally as a result of jobsite regulations that are becoming more stringent, the cost to implement the technology is coming down, and advances in technology mean that in some cases, electrified equipment can offer better and more efficient performance.”

Hybrid telescopic booms
However, the direction Genie has been taking thus far is through its FE hybrid range, which combines the benefits of a 4x4 diesel machine with the performance of a fully electric boom.
And Genie uses the example of how its FE articulating range is showing how hybrid is, in its eyes, an important development area for boom lifts generally.
The FE range has been on the market for some time now with one of its significant features being that it can keep working, and has the ability to work a full week on a single tank of fuel in hybrid mode, or all day in all-electric mode.
One of the topics under discussion in this issue of AI is onsite charging for electric equipment and the challenges of providing it for the growing requirements for electric-powered all-terrain equipment.
One solution for that, depending on the situation can be a hybrid.
The intelligent control system on Genie’s FE booms keep the batteries charged using regenerative braking technology an automatic engine start and stop, which helps keep the batteries charged and the machine ready to work.
Rather than the hybrid route, most other manufacturers are choosing the full electric option.
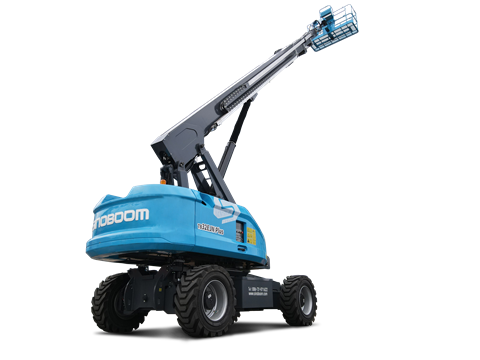
Sinoboom says its news TB32EJN is the world’s tallest electric telescopic boom without extendable chassis.
The narrow chassis is only 2.49m wide, making the boom easy to navigate jobsites, while also being convenient to transport, including in a container.
The TB32EJN, which tops out its TB series of lifts with thus far working heights of 20m to 28m, also offers a permanently oscillating axle in all working conditions.
The plan was to make a machine that is reliable and easy to maintain thanks to its simple structure without extendable undercarriage.
The model features tie-rod steering, which is easier to use and more economical than 4-wheel steering control, says the company, contributing to greater reliability.
Its hydraulic leveling, rather than electrical leveling, provides easier maintenance for service technicians, while commonality of parts with the existing Sinoboom TB26 and TB28J Plus models, contributes to TB32EJN uptime and overall good return-on-investment.
The large format screen allows easy viewing, operation, calibration and troubleshooting.
It features bright colours with good backlighting for optimum visibility, and an intuitive, rich interface with powerful functions, including visually intuitive fault buzzer and horn buttons.
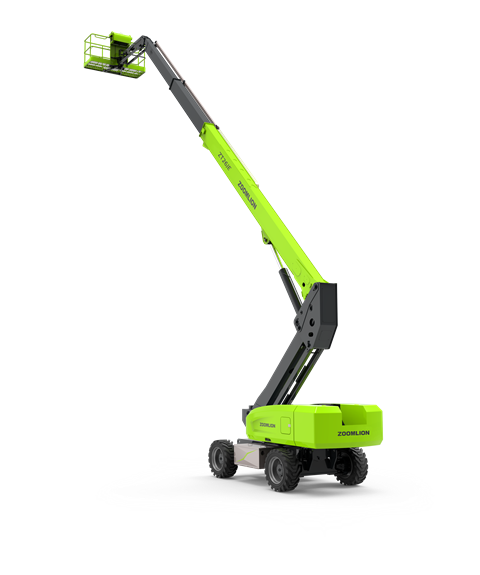
Electric aerial working platforms
Rather than the hybrid route, most other companies are choosing the full electric option.
Zoomlion Access introduced its first all-electric telescopic boom lifts in early November last year.
The two new models are the ZT22JE and ZT26JE indoor models, rather than rough terrains, and are powered by lithium batteries.
The lifts offer working heights from 24.4m to 28.7m, with horizontal outreach of 17.9m for the ZT22JE, and 22.1m for the ZT26JE.
Common features include 300kg unrestricted platform capacity, 24° gradeability, 360°continuous swing and 4-wheel drive.
“Zoomlion is devoted to providing electric and green access solutions,” said Yi Zhong, manager of R&D at Zoomlion Access.
“We initially integrated the lithium power into the Zoomlion scissors range in 2019, which is ahead of the industry trend. Now we are expanding the advanced technologies of lithium batteries into our telescopic boom lifts.”
Equipped with an 80-volt lithium battery that can be fully charged within seven hours.
Operators can also remotely manage the lifts by using Zoomlion Z-Asset, the manufacturer’s telematics system for monitoring the machines’ battery and tracking its current operation status.
“As the awareness around carbon neutrality rises, we believe the needs for electric booms will grow significantly on construction sites, especially in North America and Europe, both indoors and out,” says Jason Liu, global sales and marketing director of Zoomlion Access Overseas.
“The new chapter of electrification has opened in the access industry, and Zoomlion will take measures on delivering eco-friendly access solutions across the product lines, with electrification and sustainability as our focus.”
Telescopic booms for the European market
In 2022, LGMG Europe has plans to launch an electrically powered telescopic boom lift to the market.
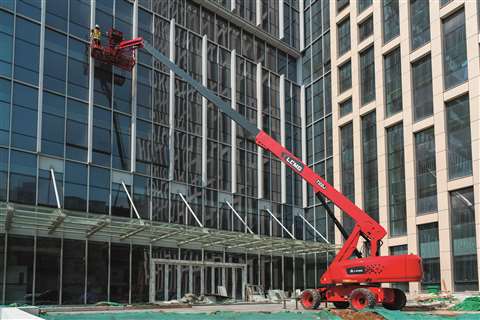
These electrically-powered booms have been tested in China since 2020, says the company and are now ready for the international market.
They follow three new booms lifts to Europe last year. The T20J, T22J and T26J were launched in 2021 in response to demands for larger platforms and dual lift capacity machines.
Combining all the elements discussed so far through its new US$348 million (CNY2.2 billion) production facility in Zhejiang, eastern China, will be Dingli.
Once completed, the new 240,000 square metre plant will be equipped with the technology required for manufacturing modern high-reach access platforms.
Around 4,000 units, including 36m - 50m working height electric boom lifts, 33m - 36m electric scissor lifts and vehicle mounted insulated booms, will be produced at the facility each year.
As the company says, over the past year it has continued to broaden its strategy of electrification with its complete boom range now available as a lithium-battery powered option.
The plant occupies a 61-acre site and forms Phase 5 of the company’s “Future Factory” expansion project, which aims to take advantage of China’s rapidly expanding access rental sector.
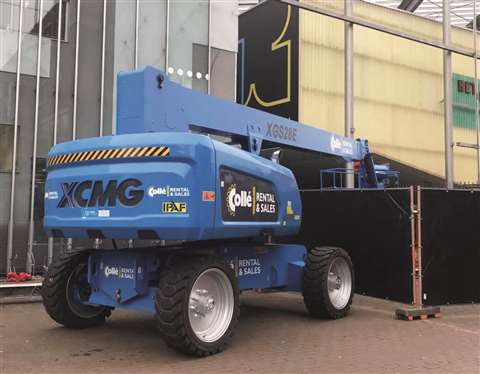
XCMG is also now delivering large volumes of scissors and booms to Europe, with stock available from the end of January at a warehouse close to XCMG’s European HQ in Krefeld, Germany.
The products include eight articulating and telescopic booms up to 28m working height.
An all-electric version of its 28m XGS28 diesel powered telescopic model will be one of them and available by July or August. It’s a 4WD model with jib and dual capacity.
Crane technology for boom lifts
Aarse told Access International the priority sales areas to start will be Germany, Austria, Switzerland and the Benelux countries.
Netherlands business Collé Rental & Sales has already placed a substantial order.
Aarse said pricing will be very competitive and the booms draw on XCMG’s crane expertise. “The boom line is ‘breathing’ crane technology. For example, they use long-life pipelines instead of hoses, like in cranes.”

Project report: Custom aerial platforms
Snorkel developed a custom 11ft platform for its 660SJ telescopic boom lift to help install siding on a mixed-use development in the city of Rome, in Central New York, US.
The siding selected for the project came in 12ft lengths and direct access to the exterior of the building was limited, making the installation using a standard platform challenging for the commercial siding contractor, Holland Exterior Specialists.
As Snorkel explains, Holland reached out to New York-based rental company MAC Equipment, which in turn, contacted Snorkel for assistance.
The solution was the 11 foot-wide platform for the Snorkel 660SJ which enabled the contractor to fasten a piece of siding in place, without needing to move the platform.
It also allowed more room for hoisting material and made it less cramped for two people to work in the platform, which ultimately made the install of siding, decking and railing on multiple levels of the building much more efficient.
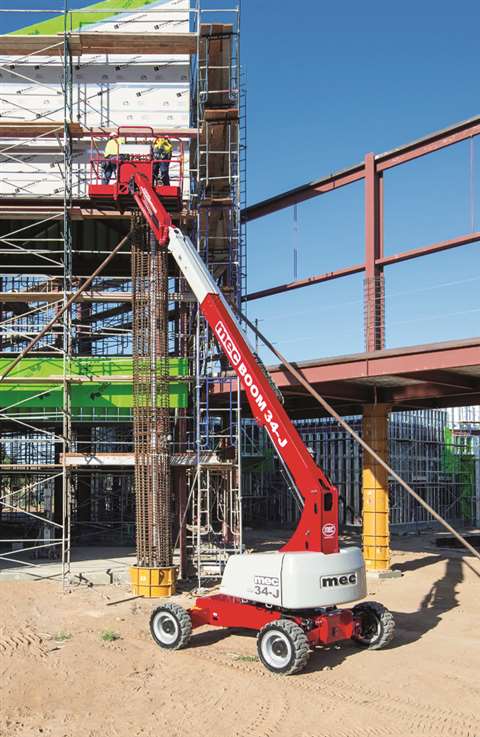
Versatile boom lift design
Beyond electrification and larger capacities versatility is also the name of the game.
Challenged to develop a better value solution boom lift for the thousands of construction jobs that are under 40 feet. The 34-J was designed to revaluate return on investment when it comes to lower height projects.
Gary Crook, VP of Engineering at US-based MEC, says smallest telescopic booms available in today’s market offer 46ft working height, which is often more machine than is necessary for the job.
“With increasing running costs, using a small, clean, and efficient diesel engine reduces the fuel consumed,” says Crook.
A key element of the specification is the low weight which means that an engine of fractionally under 25 Hp can deliver a solid 4WD rough terrain performance yet use much less fuel.
“A more compact and lighter machine that can achieve the same work objective is always a benefit to tight and congested applications,” says Crook. “More machines per delivery truck also helps to control transportation costs.”
Offering a 40ft (12.2m) working height, MEC describes its 34-J as a micro boom with standard 5ft (1.5m) jib for 135-degree range of motion.
It weighs in at 8,600 pounds (3,639kg) without, Crook says, compromising construction-grade durability.
Crucially, the 34-J can be towed with a full-size truck, or three units can fit on a flatbed truck for the lowest delivery cost.
Project report: Off-highway telescopic booms
As JLG’s Jennifer Stiansen writes, the first time Skanska heard about JLG’s new self-levelling boom lift, the JLG 670SJ, they were all in.

Tragedies in the industry had led Skanska to believe there must be a better way to work at height on uneven ground. Here was their answer.
The 670SJ uses a fully integrated, smart adapting steel chassis with self-levelling technology to automatically adapt to terrain on slopes up to 10 degrees in any direction.
The model, demonstrated at ConExpo-Con/Agg 2020 in Las Vegas, goes into production in the third quarter off this year.
It was 2017 when Mason Ford, director of sustainability and equipment services for Skanska, met with the JLG Industries team to share the contractor’s enthusiasm over the self-levelling chassis, at that time only a concept.
Once ready for the field, Skanska put the 670SJ to work on the Lynnwood Link L300 project in Mountlake Terrace, Washington, US - a nearly 4-mile raised extension of the Sound Transit rail line outside of Seattle. Skanska USA, headquartered in New York City, is the sole contractor for the project.
Ford says it was the perfect test case for the lift, because of the site’s unprepared surfaces located where they needed to access girders for the line. Normally, Skanska would use a 60ft boom lift after a significant amount of grading,
This means extra machines are basically doing unproductive work, since the pad would need to be graded out once the boom lift’s portion is completed.
For more on this project see the AI website.
Project report: Aerial platforms for high-rise projects
The government of Newfoundland and Labrador, the most easterly province of Canada, awarded the Public, Private, Partnership (P3) contract for a new mental health and addictions hospital in St. John’s Newfoundland to the Avalon Healthcare Partnership.
The Kiwi Newton Group was selected as the Design-Builder for the state-of-the-art parking facility of the project.
The three-bay, five-level car park consists of 1,000 spaces, full height mesh guard façade, two stair ways and an elevator tower.
Throughout the project, Skyjack’s SJ86 T was onsite to get into the awkward spaces created by assembly of Kiwi Newton Group’s prefabricated Canadacar parking structure.
Kiwi’s prefab structure is designed for a fast turnaround, and this large parking garage was completed from design, manufacturing, and construction in only 13 months.
As Skyjack outs it, “This system is changing the perception of what is possible to achieve in the construction industry.”

Project report: Bridges
Botswana is a southern African country without access to the sea, landlocked between South Africa to the south and southeast, Namibia to the west, Zambia to the north and Zimbabwe to the northeast.
The construction of the 1.2 km-long suspension bridge over the Okavango River makes it possible to offer transportation to and from neighbouring countries, as well as providing access to ports.
Based in Midrand, South Africa, Goscor Access Solutions (GAS) supplied the construction with two Genie SX-150 super booms.
As part of the majestic design of this project, the bridge pylons are in the form of crossed elephant tusks.
The construction site is a two-day drive from the capital, Gaborone, and the last 360km take a rough and downhill route, making the transport of equipment and materials particularly difficult.
In addition to a mix of other Genie equipment, GAS advised the use of several Genie Z-80/60 articulating boom lifts.
The great floods of 2020 and the coronavirus pandemic slowed down progress last year, but the team has managed to almost complete the job, which includes the construction of 3 km of ramps connecting existing roads, as well as rainwater drainage works, electrical installations and street lighting.
The bridge is located near the border between Botswana and Namibia. Once completed, it will provide easy access to Namibian ports and promote links with Angola and Zambia, whose borders are close to the site.
STAY CONNECTED
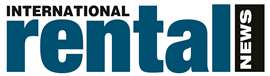


Receive the information you need when you need it through our world-leading magazines, newsletters and daily briefings.
CONNECT WITH THE TEAM
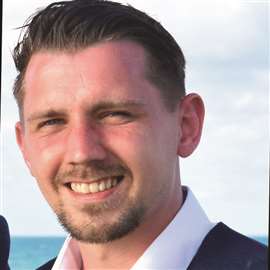
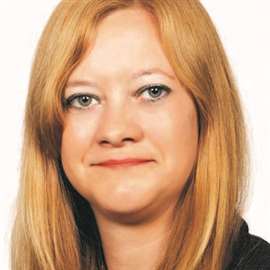
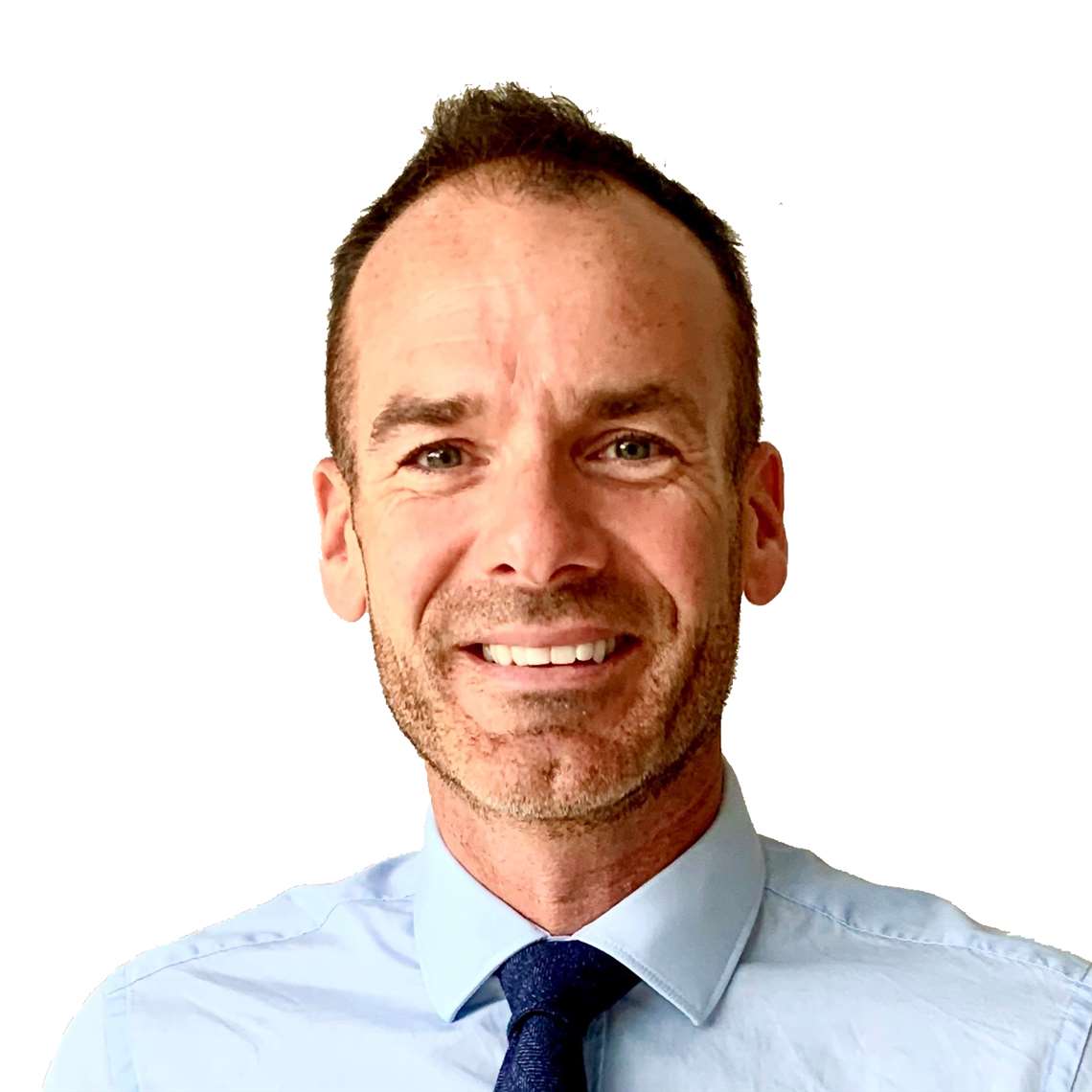