Power generation: The powers that be
17 August 2020
Ask anyone involved with construction equipment and they’ll have an opinion on the future of diesel power. Some say it’s on its way out as the adoption of electrified equipment increases, others say it will always have its place on construction sites. One thing is certain, alternatives are available and some are becoming more realistic options in terms of practicality and cost.
The hybridisation and electrification of construction equipment is a trend that has been gaining momentum. It started with diesel-electric machines powered by an engine coupled with an electric generator, AC drive motor or other source of electric power.
Today, lithium-ion battery technology is commonplace and hydrogen fuel cells (HFC) can be clearly seen on the horizon. And there’s still the good old internal combustion engine which burns cleaner with every iteration, calling into question which power source is really the best choice from both an environmental and performance standpoint.
The goal for every technology is to reduce carbon emissions while maintaining high performance standards without a prohibitive increase in cost to equipment owners.
“Cummins Stage V Performance Series
engines have been developed with the philosophy of delivering ‘more with less’,” explains Steve Nendick, marketing communications director, global off-highway at Cummins. “They deliver on average 10% more power and 20% more torque across the 75-321 kW range when compared to Stage IV predecessors.”
Cummins claims its four-cylinder F3.8 and B4.5 engines have high power density for their size, enabling manufacturers to improve machine capability and add value to machine owners.
“Cummins B6.7 engine produces over 30% more torque than its predecessor, so OEMs can downsize and replace engines of higher displacement,” Nendick says. “This reduces installation costs with no impact on productivity, as well as reducing running costs for the operator.”
These engines and aftertreatment systems are more compact and lighter than before, which suggests they are more efficient, potentially driving down fuel use and CO2 emissions.
“Another alternative is GAS (Liquefied petroleum gas),” notes Glen Hampson, business development manager, construction, Kubota UK. “We see this as the middle ground between traditional diesel and electric. The benefits of GAS are the initial purchase price, which is significantly lower than electric, and the ability to perform a full day’s work without specialist infrastructure for charging.”
He continues, “Operators can change the gas cylinder of the unit in less than three minutes. GAS machinery also emits both low noise and low vibration compared to diesel, whilst retaining engine durability due to having the same core design.”
Hybrid power for construction equipment
While diesel engines become cleaner, smaller, and more efficient, construction equipment manufacturers are also developing diesel-electric solutions that allow them to meet performance requirements needed for off-highway equipment, as well as operate within changing environmental regulations for both noise pollution and carbon emissions.
“Pairing diesel engines with an electric drivetrain can offer the same benefits expected of electrification – improved fuel efficiency, reduced noise, lower operating costs, and reliable power – but with the added durability that’s expected from diesel engines,” states Sandrine Couasnon, manager, marketing support at John Deere Power Systems.
John Deere’s 644K and 944K wheeled loaders were some of the first machines to utilise electric drive technology. According to Couasnon, they’ve collectively logged more than 1.5 million operating hours in the field to date.
Elsewhere, Caterpillar recently introduced its EU Stage V C18 hybrid engine at ConExpo, noting it provides 800hp diesel and 600hp hybrid for a total of 1,400hp with low noise and zero emissions. It’s a plug-in hybrid as well, so it can work off of the grid.
According to the company, the Cat C18 hybrid concept helps optimise machine performance by capturing surplus energy through a parallel hybrid system which, when required, will re-introduce the energy back into the machine.
“Hybrid systems offer many benefits to the OEM and end user,” notes James Gardiner, product development manager for the hybrid concept.
“We achieve engine downsizing, reduced noise and emissions levels, enhanced machine performance, and many other efficiency gains through proper integration of the complete machine system including the engine, hybrid system, drivetrain and other components with the machine.”
For its part, Perkins featured four new hybrid concepts at ConExpo. Utilising the Perkins Syncro 2.8 L engine, each of the hybrid technologies offers its own set of benefits at 75kW/100hp – all of which allow the deletion of the diesel exhaust fluid (DEF) system.
Perkins also debuted its new second-generation hybrid-electric concept, which offers OEMs a zero-emissions, zero-noise, electric-only mode.
“Perkins is focused on delivering more choice and increasing value to our customers. The four hybrid concepts are examples of future technologies that will take machine efficiency to the next level,” said Tom Nankervis, electrification marketing manager, Perkins.
“With our range of hybrid engines, customers can choose to downsize their engine and use the hybrid power for peak-load, or they can reduce output from the diesel engine, choosing to lower fuel consumption up to 20%.”
Construction equipment electrification gains momentum
Particularly in compact machinery, electrification continues to be a primary alternative to diesel power for construction equipment. Increasing numbers of OEMs are moving to electric power, such as Volvo CE which announced at the start of 2019 that, by mid-2020, it would launch a range of electric compact excavators (EC15 to EC27) and wheeled loaders (L20 to L28) and stop new diesel engine-based development of these models. However, it is important to state there is no one-size-fits-all solution.
“The off-highway applications in which it’s used vary greatly, so a single electrification solution cannot address the diverse integration and application considerations,” Couasnon says.
“Electrification is still new to market segments, and we understand that some OEMs will introduce a few electric drivetrain-powered vehicles into an existing product line,” she continues. “Our engineers have identified key electric drivetrain components that will easily integrate into an existing envelope where a transmission exists, minimising changes to the vehicle chassis.”
For full electric requirements, Cummins has bought in technology companies Brammo, JMBS and EDI, which has led to industrial projects with numerous OEMs, Nendick notes.
“Working with XCMG, Cummins has developed power for a 3.5-ton electric excavator using eight Cummins battery modules connected in a series configuration,” he says. “Producing total energy of 35 kWh, it’s ideal for urban construction site use, with zero emissions and low noise.”
Juergen Haberland, director, sales engines at MAN Engines & Components, notes electric drives have the advantage of providing instant torque over a wide range of RPMs.
“This is a very desirable characteristic,” he says. “And there is considerably lower effort in terms of maintenance. But the energy storage degrades over time… so this is the downside of that approach. I would say the technology is fantastic, but for many applications size and weight of batteries need to come down in order to successfully realise new concepts.”
How viable are hydrogen fuel cells in construction equipment?
Hydrogen fuel cell (HFC) technology and its potential application in construction equipment is being increasingly talked about in certain circles, but there are questions surrounding how cost effective it can be in real-world applications. To date, it’s mostly being used in lift trucks, offering lower operating costs, reduced emissions, improved reliability, and much faster refueling compared with battery charging/swapping.
The concept is fairly simple; HFCs essentially combine hydrogen and oxygen to produce electricity, which runs a motor. The only byproducts are heat and water.
The fuel cells are compact too, taking up less space than batteries, giving equipment manufacturers more room to play with in machine designs. Unlike traditional lead-acid batteries, hydrogen fuel cells have no power degradation, and refueling takes about three minutes, much like an internal combustion engine.
So what’s the downside? Expense, for one. The cost is higher than more time-tested technologies, but experts report that will come down over time as adoption increases. Another positive is that there is no grid dependency and solar power can be harnessed to make hydrogen on site so, in concept, it could be a sustainable technology.
Some companies are working diligently to make HFC a reality on construction sites. Cummins, for example, recently acquired Hydrogenics for its fuel cell production capabilities. Their technology is being tested on trucks and rail and will be applicable to industrial use at some time in the future, Nendick says.
“Hydrogen as a power solution is very exciting and there is certainly a future for the development of hydrogen fuels cells in equipment in the future,” he states.
“Cummins is investing in long-term hydrogen capability. Following the Hydrogenics acquisition we have also developed relationships with Loop Energy and NPROXX, looking at hydrogen storage and transportation as well as production.”
There are challenges with this technology, of course. Haberland at MAN notes that hydrogen is very difficult to store and distribute because its atomic structure is very volatile. “Over time it dissipates,” he explains. “It requires a very complex and expensive storage infrastructure on the vehicle itself.”
He also adds, “It needs to be stated that this technology is only beneficial if you take the electricity to produce the hydrogen out of renewable sources. If you use a fossil fuel to do it, then it’s not a green technology at all.”
JCB recently announced that it has developed what it claims to be the construction industry’s first ever working prototype of a hydrogen-powered excavator.
The 20 tonne 220X excavator powered by a hydrogen fuel cell has been undergoing testing at JCB’s quarry proving grounds for more than 12 months.
JCB Chairman Lord Bamford said, “The development of the first hydrogen fuelled excavator is very exciting as we strive towards a zero carbon world.
“In the coming months, JCB will continue to develop and refine this technology with advanced testing of our prototype machine and we will continue to be at the forefront of technologies designed to build a zero carbon future.”
Cost considerations for power options
The cost of power is an important consideration – electric power has a higher up-front investment cost, and a lower running cost compared to diesel. The cost, capacity and life of batteries is a key challenge to their adoption in construction but, as the technology advances, the cost will come down.
The industry is already seeing increasing numbers of OEMs adopt electric as the main power source for compact equipment, especially where the equipment is working in urban environments with strict emissions and noise regulations.
For larger equipment, diesel is likely to remain the ‘go to’ power source due to its flexibility in enduring longer and harder work periods and the ease of re-fueling. However, it shouldn’t be forgotten that electric machines offer better torque response compared to internal combustion engines and hydraulic systems.
According to Antti Väyrynen, off-highway business line director at Danfoss Editron, this improves the overall productivity and performance of the machine.
“Since electric machines can operate at a much higher peak power for a longer period of time, optimisation of the machine’s duty cycle and dimensioning can boost operational performance even further,” he says.
Electric powered equipment also boasts a high tolerance to shocks and vibrations that can lead to better reliability and an improved experience for operators.
“Benefits such as these mean that electric machines have a significantly longer lifespan than traditional hydraulic alternatives,” Väyrynen says. “Our electric motors operate on synchronous reluctance assisted permanent magnet technology, which provides outstanding efficiency in terms of low energy consumption and smaller battery size over a wide operating area.”
Where batteries are the best choice for powering equipment
Battery technology will play an interesting role in how electrification solutions evolve. Due to the power requirements in off-highway applications, the number of kilowatt hours needed from battery technology to sustain operations for a full work cycle – combined with the time it takes to charge those batteries – makes it challenging for off-highway applications to be fully electric for the foreseeable future.
“There are specific market segments that are driving off-highway electrification solutions,” notes Couasnon from John Deere Power Systems. “This is because they are invested in lowering their environmental footprint, using more efficient power generation methods and addressing emissions regulations. These include materials handling, mining, rail transportation and hybrid power generation.”
She adds, “Advancements made to support these key electrification-leading markets will eventually support the electrification development in surface off-road applications.”
Predictions on the future of power generation vary from expert to expert, but most believe there’s a lot of runway left for diesel engines.
“While the off-highway industry continues to grow and adapt, the demands remain the same. To that point, a rugged market demands a product that can meet customers’ expectations in a variety of applications,” Couasnon states. “Diesel engines offer the power density that’s required to meet the needs of off-highway applications in a way that other fuel and energy sources can’t currently match.”
Nendick agrees, adding, “For construction site managers to adopt electric power, the challenge of charging must be resolved. We expect that eventually worksites of the future will include charge stations, not that dissimilar to those fast-charging stations seen at service stations and some car parks, albeit on a greater scale.
“Fixed charge towers will be suitable for diverse, high-power and high-voltage fleet charging applications,” he adds. “Portable energy storage solutions will also be available to support non-grid enabled charging and potentially provide batteries with a useful second life. Making the most of these charging stations will require charge management through improved connectivity to monitor and coordinate the availability of energy, charger proximity, and eventually could include self-directed platforms that support autonomous machinery.”
The future of power generation in construction looks set to consist of a host of different options to meet the industry’s varying needs.
Components play a role
Improving current hydraulic systems by minimising losses and reducing battery wear consumption
“At Danfoss Editron, we offer fully electric and hybrid drivetrain systems that have been specifically designed to operate in harsh conditions across heavy-duty applications,” Antti Väyrynen, the company’s off-highway business line director claims.
“Meanwhile, Danfoss Power Solutions provides mobile hydraulics for various off-highway markets, integrating electronics and hydraulics to achieve total machine management. It was also the first company to introduce load-sensing proportional valves into hydraulic machines that could be controlled electronically,” he states.
Danfoss aims to improve current hydraulic systems by minimising losses and reducing battery wear consumption, thereby extending the operating time of machines when they are running on battery power.
Supporting documents
Click links below to download and view individual files.
STAY CONNECTED
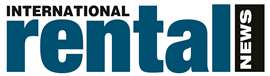


Receive the information you need when you need it through our world-leading magazines, newsletters and daily briefings.
CONNECT WITH THE TEAM
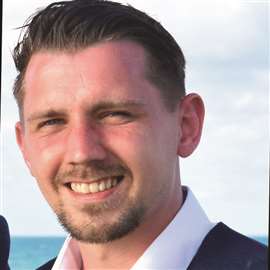
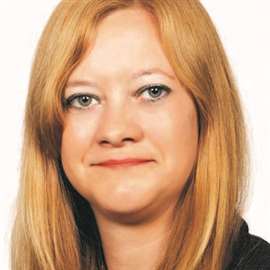
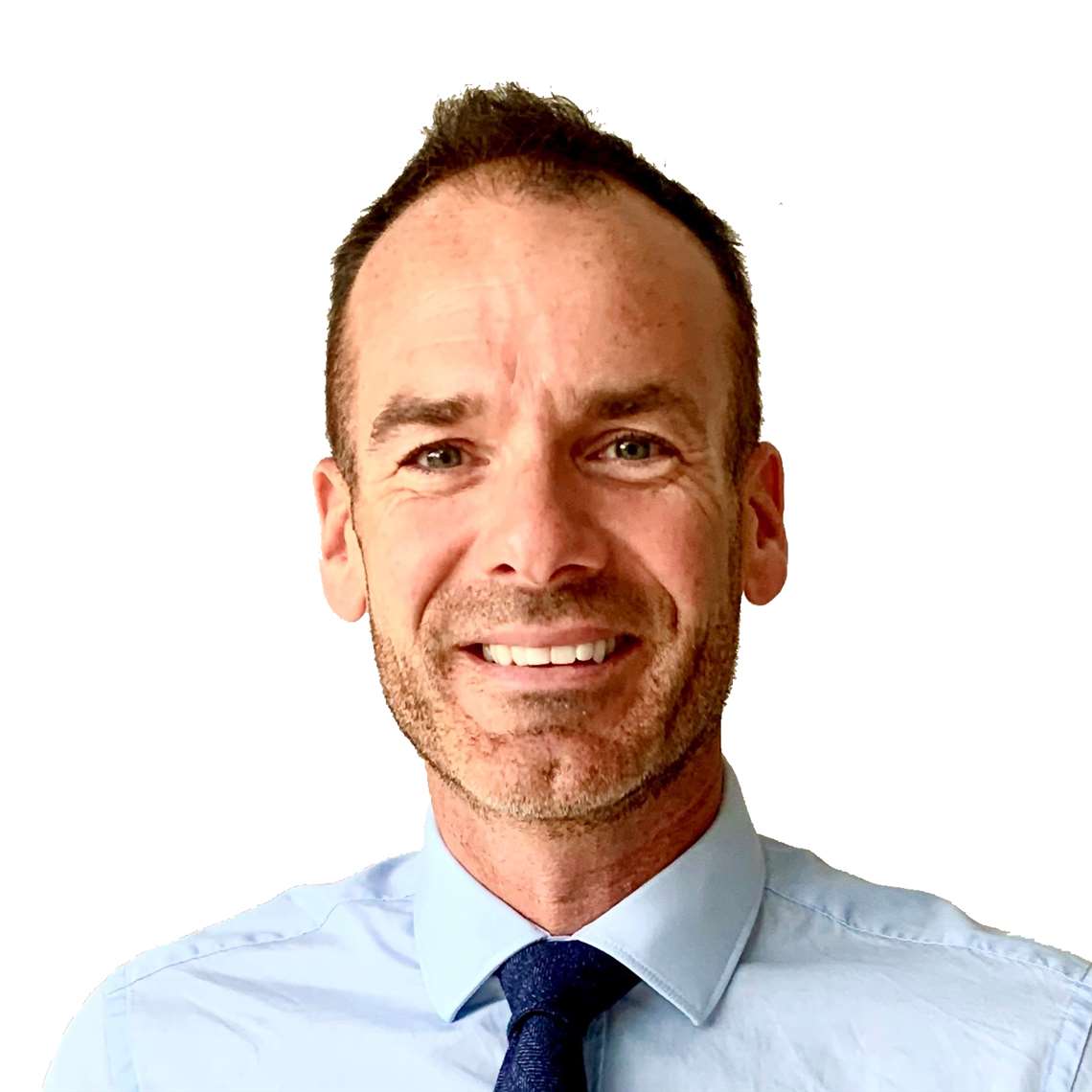