Keep It Safe
20 March 2008
Some businesses think that maintaining health and safety is a bureaucratic nightmare; some may just feel vulnerable and a little uncertain about what they should do about it.
Certainly in the UK we have to demonstrate our compliance to a considerable range of regulations for health and safety, and many believe these regulations show safety in the UK as representative of a ‘centre of excellence’ globally. However, there is no room for complacency, as figures published 2005/6 indicate:
212 workers killed at work, a rate of 0,7 per 100000 workers.
146076 other injuries to employees, a rate of 562,4 per 100000.
328000 reportable injuries occurred, a rate of 1200 per 100000 (2004/05).
30 million days lost overall, 24 million due to work-related ill health, 6 million due to workplace injury.
The European Commission's new five-year strategy for safety and health at work aims to dramatically reduce accidents at work from 4 million by 25%. The USA, meanwhile, has reported reductions in fatalities at work, but this still led to over 5000 deaths in 2005.
So what has this got to do with your business?
How would you tell the loved ones of someone who worked for you that their son or daughter was killed while working for you?
What would your customers think reading about your company in the press?
What damage to your reputation would be incurred?
Why should your customers think that you will look after their best interests with safe equipment if you do not safeguard your own people?
A senior director of a rental business once made a statement that I think sums it up: “We simply do not have the right to earn our living by putting others at risk”
There is also a statement that says, ‘Good health and safety at work is good business.’ Why?
1 The business has to work harder to meet customers’ needs if your team are not at work.
Healthy, happy and here is a good aim.
2 Management can contribute better to developing business if they aren't investigating accidents, re-organising work, repairing damaged property or plant, and dealing with loss adjusters.
Most managers have pride in what they do for you; it's hard to rebuild it.
3 In the worst case scenario, rebuilding the team, shocked at the loss of a colleague.
Some won't cope, so you may lose good people.
4 Rebuilding your reputation for being a trusted company who do things safely, effectively and well.
No business can afford the damage, the potential cost can be very significant: fines, compensation, and legal bills, increased insurance premiums, lost orders, lost custom...
The reasons then for creating a health and safety plan for your rental business are perhaps evident, but for clarity:
Good health and safety is good business.
Your reputation with your customers is at reduced risk of damage.
Your staff and customers recognise you care about their health and safety.
No unexpected costs, financially or in damaged reputation.
Of course the rental industry is represented with a huge diversity of companies-small, single-depot operations up to massive multi-nationals-but the principles for health and safety are the same; you may just need more competent safety help as you get bigger.
As you grow there are a number of changes that take place that stretch the need to manage effectively. Good communication becomes the most challenging.
To maintain a clear and consistent understanding throughout your business of what is important to the company and its customers
What it is that makes your company their favoured choice?
The essence of this message is that to make a health and safety plan you will need to state your vision for health and safety. The vision represents your values, and the aim is that they are accepted and understood and become embedded in the management of your company. A great health and safety culture will be led by your people creating it “as the way we do things round here”.
The Plan
Say where you're going:
Management leading from the front:
Walking the floor, talking and listening.
Not walking past a problem.
Endorsing and supporting staff to make it happen.
Setting out the vision and aims to create the values expected in the company for health and safety.
Creating a policy, publishing it for all to see, and ensuring that it is fully explained and understood throughout the business.
A policy statement should be straightforward in this and try to be a single side, endorsed by the most senior manager in the organisation, preferably the chief executive.
Say how you're going to get there:
A simple explanation of the organisation behind the statement.
Who is responsible for making it work?
The line managers, supervisors, fire wardens, first aiders.
Everyone in the business looking out for themselves and for each other.
Leadership being demonstrated.
The board and directors endorsing and supporting the business to make it happen.
Helping make the right investments in people, places and plant.
Helping develop skills to do the job safely and effectively with training and development.
Creating necessary systems of work, policy and procedure to control risk while delivering practical excellence in service.
To continue the plan, it is now necessary to assess your risks. This will enable you to quantify and identify the controls, understand what needs to be done and create suitable implementation programmes.
Before you can do this it is worth thinking about something I said earlier: “everyone in the business has a responsibility to look out for themselves and for others.” This means recognition that everyone knows what this is, what it means to them and you, and then what they are supposed to do with it. What are they looking out for? Do they know?
A good starting point is, do they know what a hazard is, and what hazards they have around them?
A hazard is something that has the potential to cause harm. Examples of these may be; a substance, a process, an object, vehicle, another person!
In a rental business some of these may be: a spillage, LPG gas, electricity, petrol, diesel, oils, cleaning agents, dust, awkward loads, faulty machinery, vehicles, fork lifts, loading and unloading, testing equipment.
Probably the most dangerous of all-ignorance.
Importantly-whether the potential harm is a bruised ego, injury or death.
Secondly, do they know what risk means? Risk is the likelihood of it happening.
Once you identify the risks then there is a simple hierarchy of control to follow:
Eliminate them completely.
Reduce them as much as is reasonably practicable.
Improve the controls-the methodology to reduce the risk.
Communicate the risks and train people how to work safely.
Provide personal protective equipment and ensure people use it effectively.
Decide what procedures and polices, safe systems of work or permits to work are needed and instil the disciplines needed for people to use them.
Last, one golden rule: the people assessing the risk must be competent. A recognised definition of competence is someone having the skills, knowledge, attitude, training and experience to do so.
There is also a method to assess these risks, the socalled ‘five steps to risk assessment’:
1 Look for Hazards-walk around each location, eyes wide open, for anything that might reasonably cause harm.
2 Decide who might be harmed-as well as the usual team, don't forget visitors, contractors, or customers.
3 Evaluate the risks-decide how likely it is that the hazard could cause harm. After all the controls are in place, what's left? Residual risk. How significant is it, high, medium or low?
Are there any legal requirements?
What can you do whether or not there is a specific legal duty to reduce the risk and keep the workplace safe?
If you find something that needs doing, draw up a plan of action, doing the ones you think are high-risk first.
Defining high-risk-how dangerous the hazard is, or how many people it may effect.
Then decide if you can eliminate it altogether. If you can't, how can it be controlled so that it becomes unlikely that anyone will be harmed?
Ways this might be controlled:
Prevent anyone from having access to the hazard.
Engineer safeguards-locks, guards, use of remote control, less hazardous materials.
Organise the work process differently to reduce exposure.
Use the best PPE for the job
4 Keep a record-you need to show that you have made a proper check; consulted with the people involved; dealt with all the obvious and significant hazards; taken action to provide precautions; and that what's left is a low risk.
5 Review and revise-the assessment is only any good if it reflects how the work is done, so if you change this then reassess the risk or add or improve the one you have to reflect the change.
Planning And Implementation
Now you know what your hazards are and how you are controlling them, your health and safety plan will become clearer:
Decide on your vision and aims for health and safety in your business.
Communicate them throughout the business so that they become part of the values held in your business.
Ownership will start with leadership supporting these, but rely on your people to make them happen, to demonstrate that this is “the way we do things round here”.
Draw them up in a policy statement that makes your aims for health and safety plain, show how your organisation is structured to deliver them and who is responsible.
Assess your risks and develop the necessary controls with action plans in place for the highest risks, working through all of them down to the lowest ones.
Doing so, in each location, so that local environments are taken into account and the teams’ skill sets are addressed.
Establishing the improvement programmes so that necessary training and development requirements are implemented and maintained going forward.
Monitoring And Review
The last part of the plan: what does monitoring and review mean?
It means that knowing that the controls you now have are working, and that people aren't getting hurt when they come to work with you. The complexity will vary dependant on the size of the business, but a number of methods to monitor are available:
Accident and incident reporting
Housekeeping checks
Vehicle checks
Training records and staff reviews
Legal compliance checks
Safety toolbox talks
Safety meetings
Board reporting mechanisms
Independent audit and inspections
Using safety award schemes to gain third-party opinion
Annual health and safety review.
There are two areas where questions will need to be considered:
1 What is my plan going to cost?
The principle is that good health and safety is delivered through the ‘buy-in’ and understanding coming from the line managers. Thus, in day-to-day terms it demands some of their management time to monitor and maintain your standards and controls. This may mean some collection of data, investigation of accidents and near misses, ensuring relevant training is in place for all relevant skills, a good employee induction process.
There will be some costs in providing for these;
a Communication
i Meetings
ii Toolbox talks
iii Awareness campaigns
iv Process improvement
1 Handling equipment
2 Workshop tools
3 Waste management
4 Legislative change
5 Fleet management
6 Environmental matters
b Training
c Good housekeeping and property maintenance
d Safe storage
e PPE
Many of these will already be in place and not necessarily quantified as a health and safety cost. Their suitability for your business as it is now, the size and scale, are obviously primary factors in costing the plan.
2 When do you need to appoint a full-time health and safety professional?
aTo my mind this role is absolutely there to support the line management in delivering what you say you do on your health safety and environmental policies.
bMany companies start to employ health and safety officers and advisors with a strong bias toward training, accident investigation and site inspections.
cIn some cases their role may extend to liaison with customers on safe systems of work, advice on products and their application, noise, vibration, working at height, hazardous substances, dependant on the nature and complexity of the products that you hire.
dYou may find you need the expertise to keep your business compliant and your reputation strong as you grow.
eThe cost of this person will depend on their experience, qualifications and what it is you want them to deliver. Their value will be measured by the board, their peers, and your customers. For example, the current salary range in the UK for a health and safety advisor/officer is £25-35000 (€37-52000).
Finally, strive to improve year-on-year, driving your performance in health and safety to be truly world class.
STAY CONNECTED
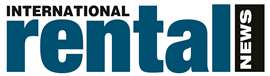


Receive the information you need when you need it through our world-leading magazines, newsletters and daily briefings.
CONNECT WITH THE TEAM
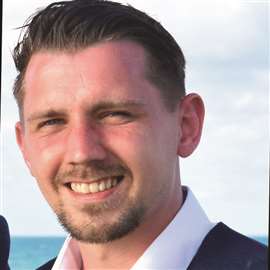
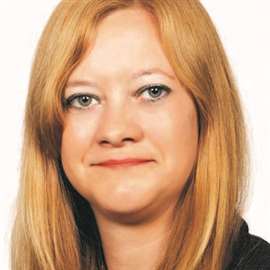
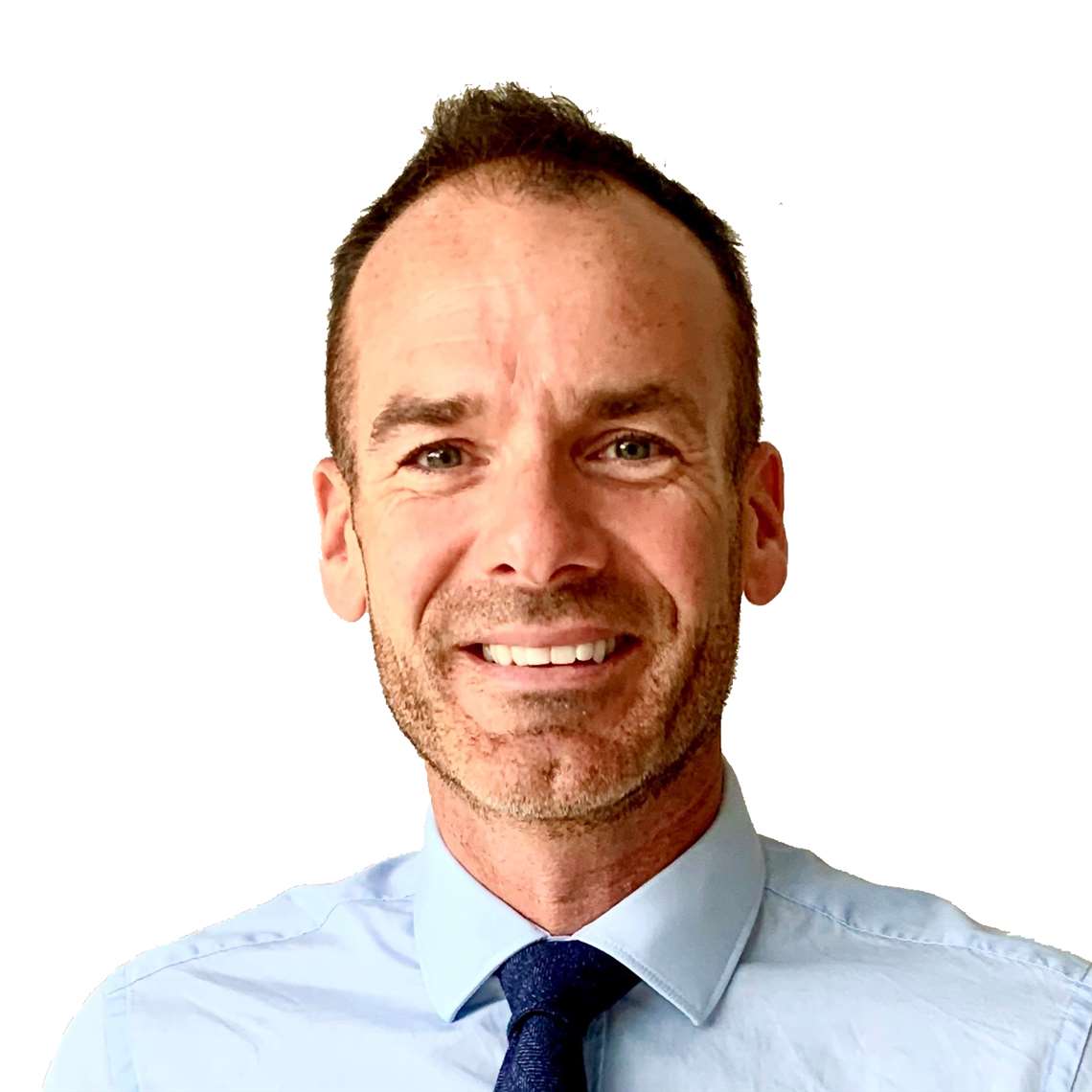