How will hydrogen change construction equipment rental?
18 August 2022
Belinda Smart looks at how industry is engaging with hydrogen, with insights on the implications for the construction equipment rental sector. Additional reporting by Julian Buckley, Editor of New Power Progress.
Regarded as a “simple” element - the hydrogen atom is made up of a single proton and a single electron – hydrogen also promises a simple solution for a complex problem: decarbonising power.
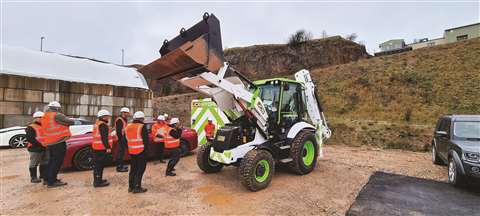
At first glance, its benefits are clear: it’s a renewable energy source and bountiful in supply; is relatively clean and non-toxic; and more efficient than many other sources of energy. On the downside, its widespread use isn’t predicted any time soon.
There’s a way to go understand its most useful application – is it better for larger machines or can it be used in smaller ones? – and to make it commercially viable.
Undeterred, OEMs such as Volvo CE (as discussed in a recent interview with IRN) and JCB, as well as engine specialists Cummins and Deutz - among other construction stakeholders - are sharpening their focus on hydrogen.
That focus currently encompasses two main areas; hydrogen internal combustion engine (ICE) technology and hydrogen fuel cell technology.
Like conventional fuel, hydrogen contains chemical energy that is released via a chemical reaction. In the case of a hydrogen-powered ICE, that reaction is combustion; in a fuel cell, the hydrogen fuel is combined with oxygen.
While the combustion in a hydrogen-powered engine is converted into mechanical energy, in a fuel cell, the chemical energy from the hydrogen and oxygen is converted into electrical energy.
OEMs are investigating the potential of both, with a range of outcomes.
JCB’s approach to hydrogen
A visit to the JCB R&D centre in the UK earlier this year revealed insights about the OEMs work-in-progress on a hydrogen internal combustion engine. In late 2021, JCB made a series of announcements which caught the eye of the national media.
At one such press call, former British Prime Minister Boris Johnson was pictured with JCB chairman, Sir Anthony Bamford, as Johnson refuelled a backhoe loader fitted with a hydrogen engine.
The event served as the official reveal for JCB’s £100 million (€118 million) investment to support development and production of a new hydrogen-fuel internal combustion engines.
Speaking at the event, Lord Bamford said: “We are investing in hydrogen as we don’t see electric being the all-round solution, particularly not for our industry because it can only be used to power smaller machines.”
Fundamental benefits of the hydrogen internal combustion engine (ICE) include rapid refuelling, while emissions from the hydrogen ICE are water and trace levels of CO2 and NOx, both of which are far lower than those of an EU Stage V-compliant diesel.
“We looked at our ‘Road to Zero’ and tried to understand what’s needed to achieve that goal,” says Tim Burnhope, chief Innovation and Growth officer, speaking to KHL journalist Julian Buckley. “We have battery-electric machines and where there is an energy demand similar to a car, then that technology is a good fit. But 85% of our product range goes above that energy demand in terms of working hours.”
What are the benefits of a hydrogen ICE?
Bunhope says that the team considered fuel cells - “[Hydrogen] is a fantastic mobile fuel, it can be taken to the site, refuel the machines and they keep working” – but concluded “fuel cells are a little immature for our industry, too complicated and too expensive. With the high transient responses of our machines, they’re not the best energy source.”
At a presentation in mid-2020, it was put forward that a hydrogen-fuel ICE would serve as the best all-round solution for JCB machines. In December, the team successfully completed the first demonstration of a hydrogen-powered engine.
The hydrogen ICE is based on the proven JCB Dieselmax 448 four-cylinder engine block, with the addition of such features as additional venting to support purging of any excess hydrogen fuel at shutdown. Unlike the block, the head unit has undergone some significant reengineering to support hydrogen as a fuel.
Paul McCarthy, Chief Engineer - Performance, Controls & Integration at JCB Power Systems says JCB’s R&D engineers identified key issues in developing a hydrogen engine; one was dealing with gas as a fuel.
“H2 is an intriguing gas, it’s very light, very low density. It disperses very well, but because of the low density and tiny molecules, getting it to mix in a cylinder can be problematic. Getting the hydrogen exactly where we want it in the cylinder has been a key focus.”
The first prototype engines used injectors developed for use with natural gas, but while suitable for testing, they are not for production models. JCB has been working with an injector supplier to develop a proprietary solution.
Getting hydrogen into the combustion chamber is an issue, but getting sufficient air is also a problem. “Hydrogen needs far more air than diesel, it’s stoichiometric combustion,” says McCarthy. “That made us focus on our turbo solutions, the way air is forced into the cylinder. We need that mass of air to carry momentum and overcome the low weight of the hydrogen gas to make a good mix.”
He adds that while the temperatures and pressures are “a bit different”, it’s still only fundamental turbocharging that can force sufficient air into the combustion chamber. “Instead of exhaust, we’re working with steam to drive the turbo,” he adds.
Water content in the exhaust has to be carefully managed to prevent that fluid combining with the oil. Together with another partner, JCB is working to develop a hydrophobic engine oil that uses additives to prevent emulsions from forming in the coolant. The development team is now working with prototype oils infused with additives to ensure those products are not drawn out of the coolant.
Unlike most JCB diesel engines which use compression ignition, the hydrogen engine requires a spark. McCarthy says that creates new issues related to over-sparking or double sparking. “It has to be very clean, very clear, which dictates how the flame front propagates combustion of the mix,” he points out.
With LPG and natural gas engines already on the market, it would seem like a simple step to produce an internal combustion engine that uses hydrogen. It might be less complex than a hydrogen fuel cell, but as the various projects which have come before the JCB project highlight, it’s far from a simple solution.
“There are so many things that are counterintuitive with hydrogen, every day is a school day,” says McCarthy.
JCB’s hydrogen fuel internal combustion engine is due for commercial launch in Q4 this year.
Is hydrogen the future of the power sector?
US-headquartered engine and power specialist Cummins spends about €1 billion on research and technology annually to help its customers decarbonise. A key focus has been supporting the future of hydrogen in the power sector.
The company is working in three key areas: production of green hydrogen, the management and transportation of hydrogen and the application of hydrogen power in internal combustion engines and fuel cells.
Jeremy Harsin, Global Construction Market Director at Cummins, tells IRN an important outcome has been the development of large-scale electrolysers - systems that use electricity to break water into hydrogen and oxygen through electrolysis - as well as a joint venture to develop tanks with hydrogen storage specialist NPROXX.
Another has been the use of hydrogen with Cummins’ new agnostic fuel platforms. Unveiled in February, the Fuel Agnostic range was developed with fuel sources including hydrogen in mind. It also offers footprint and component commonality for use with diesel and natural gas.
Benefits for the rental sector
Cummins confirms that “the Fuel Agnostic engine platform has many potential benefits to the rental sector, particularly in light of hydrogen use. Firstly, it requires minimal machine redesign: Engines within a fuel-agnostic platform have a common product architecture.
For OEMs, there is less need to drastically alter vehicle design to accommodate different versions of the same engine family.”
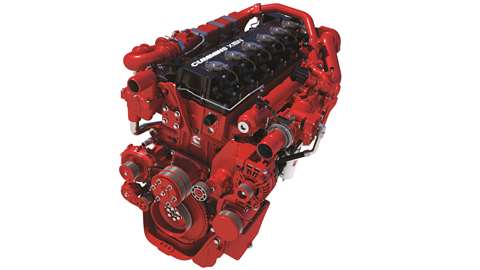
The use of hydrogen in particular also means limited manufacturing process changes. “The need to re-tool production lines and create manufacturing processes to accommodate engines that are a part of a fuel-agnostic platform is lower than adopting a completely new power technology.”
Harsin points out that fuel storage is top of mind for players developing new fuel typologies, and this is where another of hydrogen’s advantages come in; it’s more energy-dense compared to diesel or natural gas - one kilogram has the general energy equivalence of approximately three kilograms of diesel fuel.
In other words, compared to diesel or natural gas, hydrogen fuel can power a vehicle travelling the same distance or performing the same task with less fuel.
But there are still challenges; chief among them the supply infrastructure for the fuel, at least to date.
“Despite many projects currently in place around the world to increase hydrogen, developing such critical infrastructure takes time and resources,” Harsin tells IRN. “This means that the adoption of hydrogen will most likely begin in markets where fuelling can be done centrally,” for example, close to large hydrogen hubs.
As hydrogen production, distribution, and equipment development scales up, cost will decrease, which is good news, albeit a longer term prospect, with the change anticipated to take place over the next 10-20 years for a wide range of applications.
“Ultimately though, hydrogen will be competitive with internal combustion engine counterparts,” says Harsin.
Cummins also has several projects related to development areas in hydrogen fuel power. It has installed over 2,000 hydrogen fuel cells across various on-highway and off-highway applications around the world.
Examples range from commercial truck operations in Norway with ASKO, a major grocery wholesaler in the region, and Alstom’s Coradia iLint – the world’s first hydrogen-powered train in commercial operation throughout Europe.
Recently, Cummins announced that alongside partners Air Liquide, it had completed construction and commissioning of the world’s largest PEM (Proton Exchange Membrane) electrolyser - used to generate hydrogen. It is supplied with renewable energy and is producing up to 8.2 tons per day of low-carbon hydrogen in Bécancour, Québec, Canada.
And last year, it launched a partnership with Iberdrola, to create one of the world’s largest electrolyser plants in Castilla-La Mancha, Spain. A joint venture with NPROXX also means Cummins is building capability in high-pressure hydrogen storage for both stationary and mobile applications.
Hydrogen ICE
Meanwhile, German ICE manufacturer Deutz has launched its first hydrogen engine, the TCG 7.8 H2. Launched in 2021, it has a drive that meets all eligibility criteria set by the EU for zero CO2 emission engines – and an output of around 200 kilowatts, making it suitable for all off-highway applications.
“We are already seeing a lot of interest in our H2 engines from customers across all application areas,” says Dr. Markus Müller, Chief Technology Officer of Deutz. “And we are already planning further pilot applications.”
The TCG 7.8 H2 is currently being tested in a joint pilot project with a regional utility company in Germany, and volume production is scheduled to start in 2024.
STAY CONNECTED
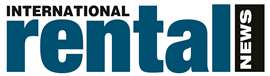


Receive the information you need when you need it through our world-leading magazines, newsletters and daily briefings.
CONNECT WITH THE TEAM
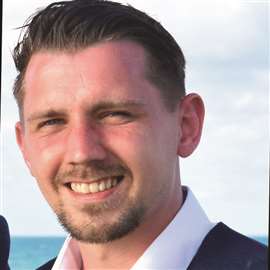
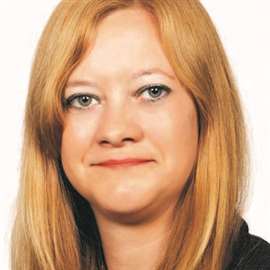
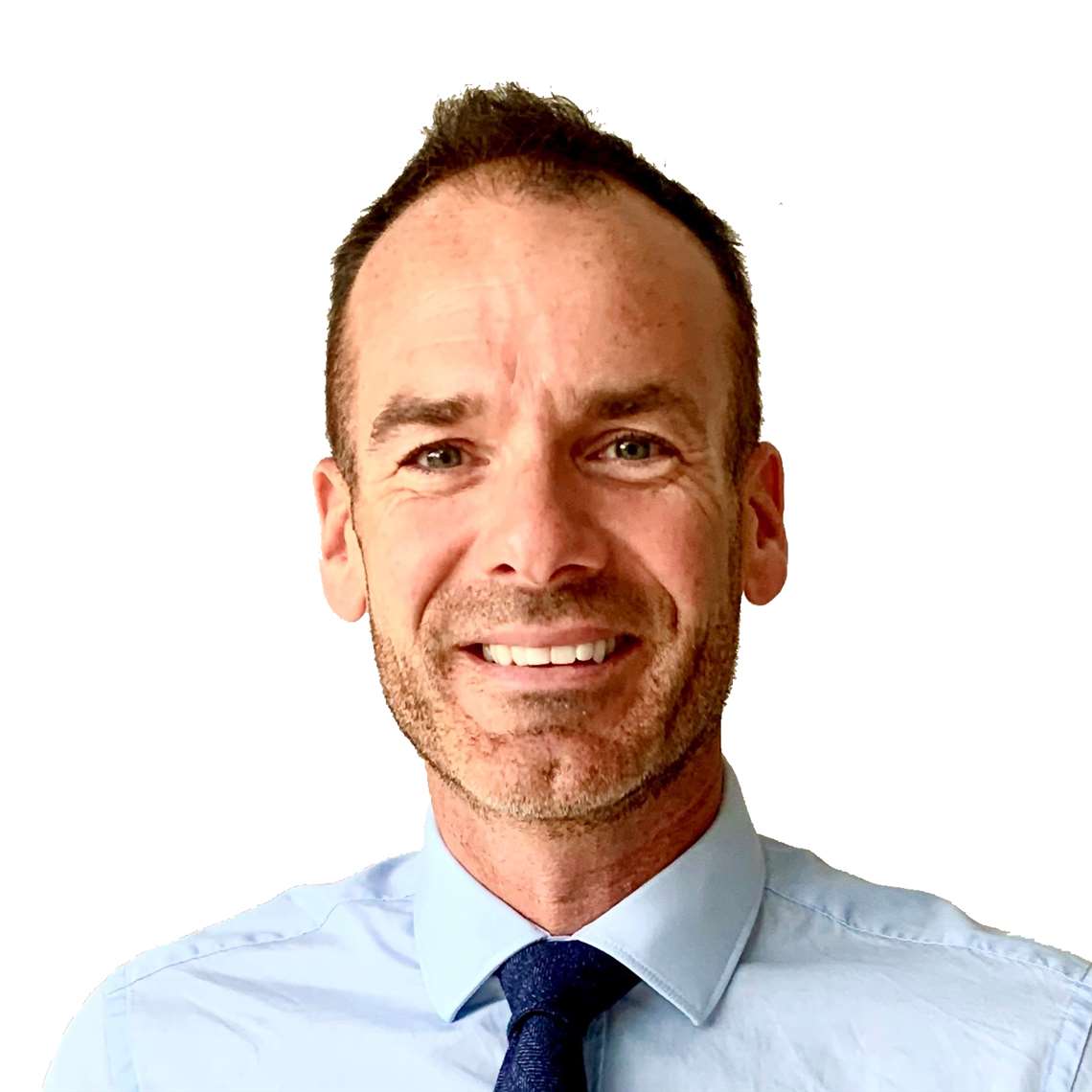