How technology can advance modular construction
09 June 2023
The Architecture, Engineering and Construction (AEC) sector lags behind other industries in terms of its environmental, social and governance (ESG) standards. Responsible for one-third of global energy consumption, the sector’s large environmental footprint stems in part from its waste-heavy and energy-intensive supply chains.
Construction workers are exposed to hazardous situations, and frequent cost increases and delays due to highly complex workflows that continue to plague the industry and affect housing affordability.
Modular construction – manufacturing building parts in a factory and assembling them on site – is one approach to addressing the sector’s ESG challenges. Prefabricated modular units may range from flat-pack components, such as walls, complex mechanical, electrical and plumbing (MEP) assemblies to three-dimensional building sections, such as fully built bathrooms.
The practice of off-site construction has been around since the early 1900s but has, until recently, remained a niche approach. This is changing as advances in digital technology have eroded some of the traditional shortcomings of off-site construction. State-of-the-art digital tools enable complex planning and help optimise module design, workflows and delivery logistics. Off-site construction now offers solutions to a range of pressing social and environmental challenges associated with traditional on-site methods.
Prefabrication can reduce construction’s environmental impact
Currently, an estimated 25% of construction material ends up in landfills. Prefabrication helps reduce waste by optimising material usage and enabling reuse or recycling of offcuts. Because prefabricated components are manufactured in a controlled, moisture-free environment, it is easier to use sustainable materials for some of the components, such as wood. Constructing large parts of a building off-site means construction managers need to transport less material to the site, which results in fewer emissions. Less on-site construction waste also means fewer emissions from waste removal trucks.
In addition, the controlled factory environment reduces the potential for human error and optimises workflows. Weather delays do not derail in-factory construction, and on-site foundation work can take place while the modular units are assembled. From an environmental perspective, these optimisations bring several advantages: Less time spent on construction inevitably translates into fewer carbon emissions from vehicles and less heating or cooling requirements at construction sites. Bringing in pre-assembled building units minimises noise and dust pollution at the site.
At the end of their lifecycle, prefabricated building units can be disassembled without demolishing them. Thanks to standard sizing, deconstructed modular units are more likely to be reused at other sites. All in all, the European Program EuroHouse estimates that modular construction reduces the quantity of material utilised and produced by excavations by 50% and produces up to 80% less waste during on-site works.
The construction industry has notoriously struggled with poor safety records. By shifting part of the construction process to a controlled factory environment and minimising time spent on the construction site, prefabrication reduces the potential for many common workplace accidents. Thus, factory-based construction offers safer and more comfortable working conditions for construction workers. Meanwhile, the factories can be set up where the labour is — a crucial advantage in an industry plagued by talent shortages.
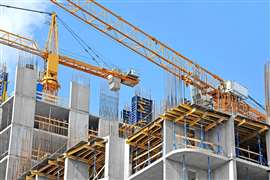
Cost savings and social benefits of prefabrication
Besides improved worker well-being, prefabrication offers additional social benefits. The construction industry is facing a growing and urgent need for affordable housing, and prefabrication can help to meet this demand. Because prefabricated components can be manufactured quickly and efficiently, it’s possible to construct high-quality, affordable housing units in less time and at a lower cost than with traditional methods.
The same holds true for community-serving infrastructure that can be built at scale, such as schools and hospitals. During the Covid emergency, for example, modular construction allowed China to set up new hospitals within a matter of weeks. And off-site construction still has enormous cost- and time-saving potential — which rapidly evolving digital technology is poised to address.
McKinsey & Company expects digitalisation and automation to rapidly transform the construction industry, whereby prefabrication will play a major part.v Today’s project-based approach is set to shift to a more product-based one, with construction sites increasingly turning into places of assembly of pre-engineered parts.
The need to keep all project participants up-to-date increases demand for building information modelling (BIM) and modern data-sharing solutions. Current industry solutions connect previously siloed players by making data accessible to disparate stakeholders across all phases of the construction project. Platforms that are crafted for optimising building design and construction by connecting the office and the field every step of the way are especially important.
Construction’s need for digital solutions
Stacks of integrated solutions empower customers to monitor the complexity of their projects based on near real-time status and geographic location. Purpose-built for the construction industry, these solutions provide an easy-to-use interface for material coordinators, workforce planners, and construction management teams to plan activities effectively and support the schedule.
Tight building schedules and labour shortages are driving the adoption of prefabrication methods out of necessity. BIM-focused reality analysis platforms have emerged to effectively address these pain points. Automated workflow tools enable teams to detect and fix mistakes, reduce costly rework, prevent critical path delays, and gain accurate, transparent financial visibility into the project’s progress.
Reality capture technology allows for precise layout and measurements. Künzli Holz AG, for example, used the Leica iCON solution in the construction of a new children’s hospital in Lengg, Zurich. The new hospital is a hybrid concrete structure with prefabricated timber frame elements. Robotic total stations enable the placement of the prefabricated elements with incomparable accuracy, allowing Künzli Holz AG to maximise the structural and architectural advantages of combining components made of different materials.
Total stations enable the creation of more sophisticated and flexible systems of off-site components and the integration of off-site components into conventional builds. The technology thus helps address a major “image problem” of modular construction, a method often associated with boring building designs that allow for little customisation. In addition, software modelling and simulations let designers fine-tune building designs and optimise prefabrication — which helps to speed up construction and reduce waste.
Modular construction and digitalisation will go hand-in-hand in making the AEC sector cleaner, leaner and greener. What may look like an almost impossible challenge — to meet skyrocketing building needs in the face of dwindling resources and labour shortages — can turn into promising opportunities for reimagining construction practices poised to benefit the environment, society and the bottom line.
Eva Carranza is Hexagon’s Global Director ESG & Sustainability.
STAY CONNECTED
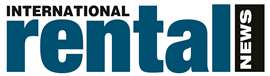


Receive the information you need when you need it through our world-leading magazines, newsletters and daily briefings.
CONNECT WITH THE TEAM
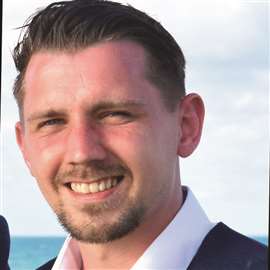
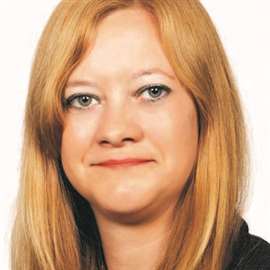
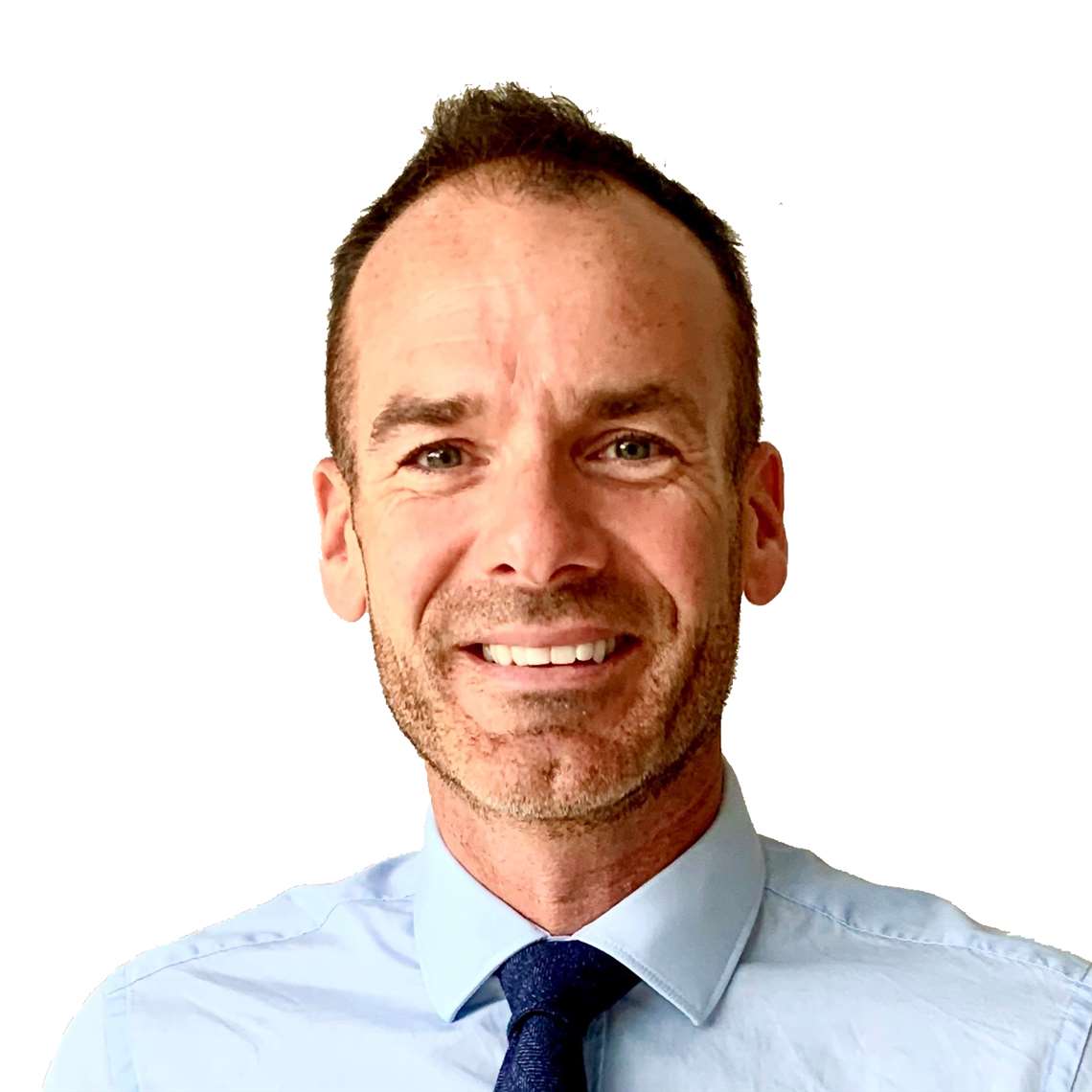