Four challenges facing modular housing construction
11 July 2023
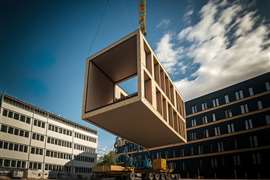
The benefits of employing modular construction techniques to build new houses should be something of a no-brainer.
When the system works, it should allow for faster construction of energy-efficient dwellings, arguably to higher levels of quality thanks to the production of repeatable designs in factory conditions.
“Constructing a modular building off-site in a purpose-built facility provides a far more stable, controlled and safe environment compared to traditional construction. It also reduces logistics,” says David Wilson, depot operations manager, at UK-based portable and modular building company JCPSA.
“The materials used within modular construction are delivered to a single location in bulk volumes, compared to the frequent individual deliveries and associated miles of traditional construction sites. Thanks to standardised products and minimal follow-up work on site, there are potentially high cost savings from modular buildings,” he adds.
No wonder then, that huge sums of money have been invested in modular builders around the world and there have been warm words about modular construction’s potential, along with the wider promise of modern methods of construction (MMC), from government and private clients and developers.
Modular builders under pressure
But the reality for several manufacturers has not been plain sailing.
In the UK, Yorkshire-based Ilke Homes, which manufactures modular homes for clients including local authorities and housing associations fell into administration last month. It attempted to find a buyer before its collapse, citing “volatile” trading conditions and called for more investment to meet its overheads.
It is the latest in a string of UK modular builders to hit challenging times. In May, insurer Legal & General halted production of its loss-making modular housing factory near Leeds, while it reviewed the business.
In Europe, Skanska’s BokLok joint venture with Ikea is the subject of a turnaround plan.
Last year, UK-based Caledonian Modular and Urban Splash Modular both collapsed.
And in the US, modular giant Katerra filed for bankruptcy in 2021 after its financial backers reportedly pumped a total of $2 billion into the business. Volumetric Building Companies has since bought the company’s factory in Tracy, California.
So why is it proving so tough for modular construction companies to maintain positive cashflow and stay profitable when, on paper, their product appears to have so many advantages over traditional housebuilding methods?
And what needs to change to put modular construction on a more stable footing?
4 challenges facing modular housebuilders
1) Controlling costs
Designing and setting up manufacturing facilities involves a significant capital expenditure. There are also substantial working capital requirements that modular companies face, receiving payment only once a project is complete.
“Advanced manufacturing doesn’t come cheap,” says Verity Davidge, director of policy at manufacturers’ organisation Make UK. “It’s a significant investment. If we look at the modular builders we represent, there’s been about £1 billion (US$1.3 billion) of private investment already made. You have to be innovative, dynamic, you have to be investing in robotics and cobotics.”
“The problem is that margins for many contractors are in the range of 1%-2%,” says managing director of consulting engineers Sutcliffe, Sean Keyes.
Sutcliffe is involved in the design of around 20,000 homes a year across the UK, constructed and procured in a variety of different ways, including modular.
“If you look at other sectors like social media and software development, margins can by 20%, 50% or even 100%. All of the research and development needed is being paid for by a healthy profit. But in the modular construction sector, sadly that isn’t the case,” he says.
Meanwhile, production delays can push up costs not just at the factory but on the construction site where modular units are destined to be delivered too. “The cost of a construction site standing still can be quite a significant cost. If the product is delayed in the factory then you are also paying for the site’s operational cost – the security, the fencing, the site agents, the teams of people on site,” he says.
2) Volatile order pipelines
Important when it comes to keeping cash flowing and staying on top of costs is having a consistent pipeline of orders.
And that is where the construction business model differs from, for example, car manufacturing.
“You are bound to have gaps and delays in between different contracts,” says Keyes.
That can prove even trickier in an inflationary environment because manufacturers don’t necessarily have the certainty to order materials like steel or timber when prices are more advantageous because of a lack of regular work.
3) Planning snags and political instability
Meanwhile, Davidge points out that a lack of stability when it comes to political policies and hold-ups in the planning process can also prove to be significant obstacles to modular builders.
“Frustrations with planning – the lack of understanding from local authorities – is a common problem modular building shares with traditional building,” Davidge says.
“Housing policy will also change with governments or indeed changes within the machinery of government,” she adds.
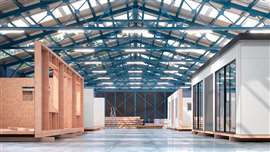
Targets setting out the number of homes to be built can come and go. For example, the UK government recently dropped its ambition to build 300,000 homes a year, and the industry is instead managing something around 180,000 to 200,000 a year.
“When you make an investment [in a factory], you need to understand that that investment is going to pay off. The lack of certainty puts modular housebuilders at a disadvantage,” Davidge adds.
Wilson makes a similar observation. “One problem is that standardised regulations designed around traditional building methods are also levelled at modular building companies, who can lose their competitive edge when trying to conform.
“This can leave the consumer to see no real-term benefit from choosing a modular building, which can also be seen as a gamble due to the infancy of the industry,” he says.
And Ian Atkinson, partner in the construction team at Womble Bond Dickinson adds, “Where investment has been made in developing large factories for modular construction, the pipeline of work has not been consistent enough to support that investment.
“The traditional process of large-scale housebuilding in the UK is to buy land and then build houses at a rate driven by sales numbers such that the market is not flooded. On the other hand, MMC factories rely on a constant pipeline of orders. So, there is a conflict between the two models that requires a huge shift in practice and mindset to resolve.”
4) Added complexity
Keyes argues that in order to be successful, factory-built homes need to be more repeatable and consistent in their design, in order to make their production and installation faster and more efficient.
“I think people anticipate that they can bring everything to site as a completed product and just bolt it together and connect it to the services and away you go. The difficulty is that most things are not exactly the same. We are building one-bedroom apartments, two bedroom-apartments, three-bedroom semis, terraced houses and we are looking to chop and change them. As soon as you start changing things you have another variable to take into account,” he says.
Wilson adds, “Many modular companies are trying to act like traditional building companies, but modern methods of construction (MMC) should act as a stand-alone entity.
“They offer near-instant deployment, with all the comfort and durability of a traditional building. To us, modular buildings should be seen as a refined product.”
And Atkinson thinks that consumers need to understand that modular houses are different to traditionally constructed homes, while also providing its own benefits, “Public perception also needs to change. In the UK, the customers want their houses to feel unique and special, and the idea of buying a factory-built ‘prefab’ model is yet to catch on.
“However, we know it can be done. In Japan, MMC is seen as aspirational. Selecting your home and its ancillary parts that customise it to your way of life are a collaborative process between housebuilder and homeowner.”
4 ways to put modular construction on a surer footing
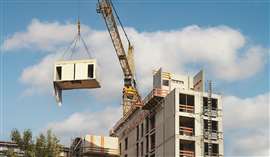
Fortunately, the appetite for modular construction still appears to be strong and there are positive developments in the sector too.
In June this year, modular builder Admares announced plans to build a $750 million modular ‘mega factory’ in the city of Waycross, in Georgia, USA, with the aim of producing housing systems by the end of 2025, demonstrating that significant funds are being committed to a modular future.
Keyes points to successes in the UK, like Starship Group on The Wirral, which rather than building full modules, produces light gauge steel systems and 2D panelised systems finished with windows and doors, or Mansell Building Solutions in Manchester which pre-fabricates panelised solutions in its own manufacturing facility.
And there are ways that could help put modular builders on a surer footing for the future. They include:
1) Guaranteeing demand
With choppy demand one of the key challenges facing manufacturers grappling with high costs, both Keyes and Davidge recommend that clients – particularly those in the public sector – specify a certain proportion of modular homes to build a pipeline and create a smoother flow of demand.
Both recommend public sector organisations commit to building a certain proportion of homes using modular construction.
“I’d like to see a certain proportion of affordable housing grants dedicated to modular and empower new building techniques for a new generation,” says Davidge. “These factories can be a game changer – they are precision-building beautiful homes.”
2) Political stability
Hand in hand with stimulating more demand from the public sector, goes clearer and more consistent messaging on overall housing targets.
Davidge advocates political stability to foster the right environment for confidence among investors both in offsite manufacturers and developers proposing to employ modular construction methods on their projects.
3) Improved financing options for developers
Developers also need to be able to access finance developments using those modular methods.
Traditional banks have been slow on this front but major lenders offering frameworks for the financing of modular construction schemes are starting to emerge.
One such lender in the UK is Atelier, which offers loans of £5 million (US$6.4 million) to £40 million (US$51 million).
Chris Gardner, joint CEO at Atelier, said he hoped the initiative would pave the way for more modular construction.
He said, “We’ve collaborated across the construction industry, incorporating the expertise of more than 30 leaders in offsite technology to give developers, intermediaries and contractors a clear and practical guide to the opportunities and challenges that these new ways of building offer. We’re working to be the lender of choice for developers who decide offsite is right for them.”
4) Stop imitating traditional construction
Wilson thinks that modular builders should try to avoid imitating traditional builders, which in his view leads to more work on site and erodes the value of offside manufacturing.
He says, “As these buildings are recent developments, they can’t demonstrate a history of 60+ years of performance, especially within forward-thinking design and build modular units.
“This can stifle more innovative processes, meaning off-site build companies find themselves moving towards part-build methods to conform, which in turn leads to more work being completed on-site.
“This knock-on effect can make traditional construction an easier option with fewer restraints. Modular companies need to stop imitating what’s already being offered and aim to offer something different and superior.
“The modular industry should be built from the ground up, not from the remnants of traditional building methods.”
STAY CONNECTED
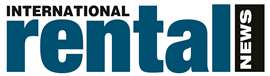


Receive the information you need when you need it through our world-leading magazines, newsletters and daily briefings.
CONNECT WITH THE TEAM
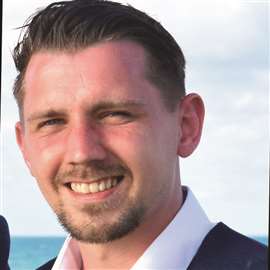
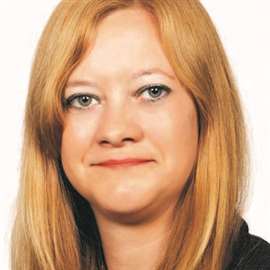
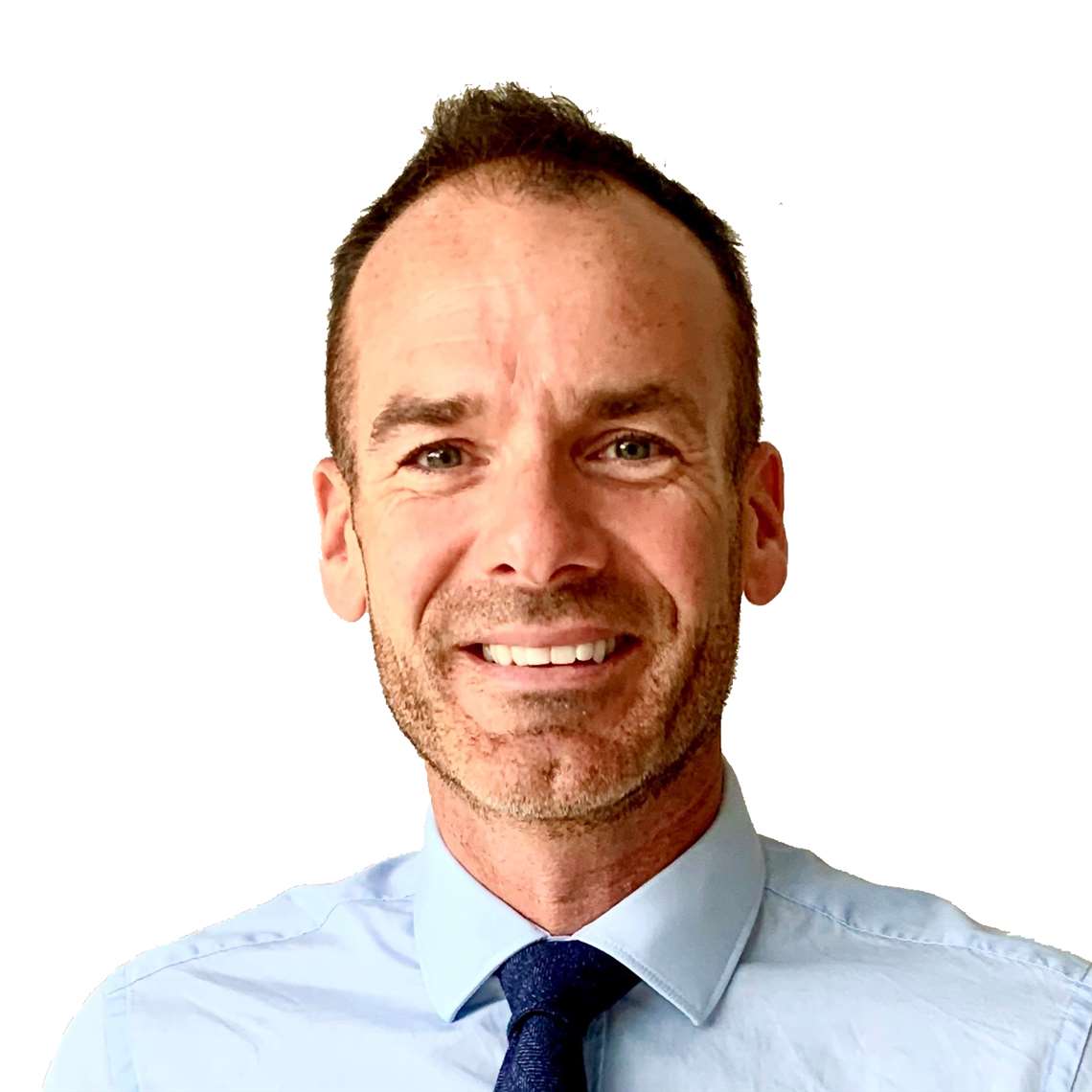