Exoskeletons: Will they become a more common sight on construction sites?
19 May 2023
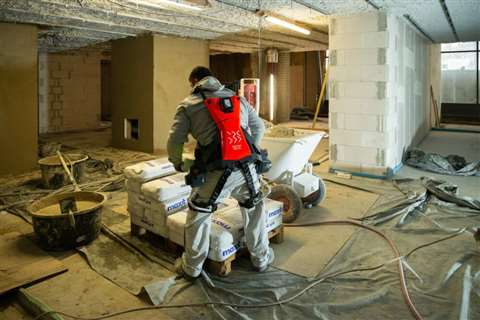
Construction work can be hard on the body.
Musculoskeletal disorders (MSD) are the single largest cause of work-related illness in the sector.
In the US, work-related MSD is 16% higher in construction than in all industries combined. It affects as many as 44 million workers in the European Union (EU), and costs the European economy an estimated €240 billion (US$262.7 billion).
So providing workers with a wearable solution that reduces strain on their joints during repetitive manual tasks and in some cases increases their strength seems like an obvious step.
One potential solution is an exoskeleton. Already there is an array of options available from different manufacturers, who in many cases have adapted it from a medical setting to create a use case for industrial settings.
But the sight of an exoskeleton on a construction site is still very rare. While some contractors have trialled the technology and their prevalence is growing slowly, growth is slower than in other industries like manufacturing. And few contractors have yet invested in exoskeletons as a solution for their wider workforce.
Advantages need to be balanced against disadvantages
Studies that examine the use of exoskeletons in construction are similarly rare. And this could be part of the reason why uptake so far has been slow.
Some have uncovered health and productivity benefits. The Centers for Disease Control and Prevention (CDC) in the US pointed to a study that showed exoskeletons designed to decrease load to the spine decreased work, fatigue and load. Others have found that exoskeletons are capable of decreasing shoulder discomfort.
Meanwhile, Lockheed Martin, which developed an exoskeleton for US Navy workers involved in using heavy tools for tasks like sandblasting, riveting and grinding off excess metal increased their productivity between two and 27 times.
And in an industry with a skills shortage and an ageing workforce, exoskeletons and exosuits could open up job opportunities to workers who might otherwise have physically been unable to perform certain essential tasks.
But there’s the risk of unintended adverse effects too.
A 2017 study in France (Froment, N. The use of exoskeletons on construction sites) found that a device that assisted users with overhead loads created additional effort for the wearer by forcing them to counteract resistance if they wanted to move their arms below the intended range.
And the same study that found a benefit to the spine also discovered that increased chest pressure due to wearing the devise could affect workers with pre-existing conditions like chronic obstructive pulmonary disease (COPD). The CDC also warned of the potential for pressure wounds or compressed nerves from poorly fitted devices.
There are more practical challenges too. As much as exoskeletons may protect workers doing certain repetitive tasks or while trying to hold awkward postures, their added bulk could also present movement challenges in other circumstances, or even safety concerns if their added weight causes users to lose balance. And they could be uncomfortable or hot to wear for extended periods of time.
That’s partly due to the fact that most exoskeletons produced so far are not designed specifically for construction, which can limit their effectiveness.
And then there is the cost. Kitting out a significant number of workers with exoskeletons and then maintaining them has the potential to be expensive.
Exoskeletons and exosuits typically cost thousands of dollars, with even the cheapest over $1,000. That could prove a tough sell in an industry that historically is quite resistant to change.
Finally there are regulatory issues. “As the technology is relatively new and specific regulations governing their use in construction currently don’t exist, some companies are hesitant to adopt exoskeletons,” says Ali Golabchi research and innovation scientist at the University of Alberta in Canada.
Ongoing trials
Of course, developers of exoskeletons and exosuits are not standing still. The Apex 2, which is due to be available this summer, has been redesigned to reduce its weight by 30%. That in turn reduces heat retention, alongside more breathable materials.
Ekso Bionics, whose earlier EksoVest cost about $7,000 has claims to have reduced the cost of its updated Evo model. It has also used trial feedback to make it slimmer and lighter, as well as reducing the amount of heat it generates for users.
Meanwhile other trials and evaluations of exosuits and exoskeletons for construction continue.
In Europe and the UK, the Exskallerate project aims to increase the adoption of exoskeletons in the building and manufacturing industries by encouraging construction companies to trial passive exoskeletons for free. The project is funded by InterrReg North Sea Region and is supported by BE-ST, formerly the Construction Scotland Innovation Centre, although it will come to an end within the next few months.
And the University of Alberta’s Construction Innovation Centre (CIC) in Canada is working to evaluate the technology, specifically as it relates to construction work. With the technology still in its infancy, most studies so far have focused on other industries like the automotive sector.
“Construction work sites are dynamic environments and construction tasks have higher levels of complexity compared to many other industries,” explains Golabchi, who is working on the evaluation.
“As a result, we are evaluating the technology through different angles, from using various measurement techniques including objective (e.g., muscle activity, motion data) and subjective (e.g., user comfort) metrics, to identification of proper strategies for effective adoption at an organizational level.”
The university is working with industry partners and taking experiments onto construction sites, with most of the prior research in exoskeletons having taken place in a lab environment.
Golabchi sees exoskeletons as a promising solution for alleviating the physicaly demands of construction work and reducing the rate of injuries.
He also believes that the evaluation of exoskeletons as to be task specific. He sees the main applications for exoskeletons in construction as being related to the back and shoulders, making back-support exoskeletons a potential solution. But he warns that this does not mean workers can use them to lift over allowable lifting thresholds.
“Our experiments show that workers generally perceive exoskeletons to have a positive impact on their efficiency. However, further long-term studies are needed to scientifically confirm this. Similarly, the impact of exoskeletons on work quality also requires more research,” he says.
But all in all, Golabchi remains optimistic about the future of the exoskeleton in construction. “Overall, I believe as the exoskeleton technology evolves and these devices become smaller, cheaper, more user friendly, and more accessible, we will see them more and more in construction sites,” he adds.
“Continued research and development in the field will lead to better understanding of the needs and requirements of construction workers, resulting in more effective and comfortable exoskeleton designs.
8 construction exoskeletons and exosuits
There is now an array of different exoskeletons and exosuits available to construction companies across the world. International Construction has rounded up 10 of the best-known models in the sector:
1) Auxivo Carrysuit
Swiss firm Auxivo has developed a passive upper body exosuit that aims to reduce loads on the hands, arms, shoulders and back while carrying and holding heavy loads. Its rigid frame stretches from above the user’s shoulders to their hips, and transfers load to their hips. The company has field tested the project on construction sites in Switzerland.
Cost: CHF1,690 (US$1868.70)
2) Bioservo Ironhand
A battery-powered exoskeleton specifically for the hand, which Swedish company Bioservo claims can help construction workers with grip-intensive or repetitive work tasks. The system consists of a glove, covering all five fingers, and a power back worn as a backpack or hip-carry. It activates when users start moving their hands to perform a task, using sensors on the palm and fingers. It pulls artificial tendons in the fingers to strengthen users’ grip and a ‘Smart Assist’ function learns hope operators use the glove and adapts the control system to provide a natural force.
Cost: €6,500 (US$7,275)
3) Ekso Bionics Evo
A passive upper body lifting exoskeleton which aims to eliminate neck, shoulder and back injuries, as well as increasing productivity and reducing fatigue. The new exosuit supersedes the EksoVest, and promises a lower cost, reduced heat and greater comfort. It also decouples the left and right shoulder support structures which Ekso Bionics claims increases flexibility in a user’s torso or waist. It provides 4.8lbs-15lbs (2.2-6.8kg) of lift assistance per arm.
Cost: Not known
4) German Bionic Cray X
German Bionic has developed the Cray X exoskeleton, a battery-powered device with a carbon fibre frame which provides 66lb (30kg) of lifting support. The upper body exosuit runs from the shoulders to the hips and thighs. It has also been designed to be dust- and waterproof to IP54. It won a “Best of Innovation” distinction in the wearables category of the CES 2023 Innovation Awards in January this year.
Cost: Subscription model starting at US$499 a month
5) HeroWear Apex 2
A passive suit weighing 3lb (1.3kg), which HeroWear claims can take 75lbs (34kg) of strain off a user’s back. The manufacturer claims it can reduce muscle fatigue and strain by up to 40% during physically demanding movements. It primarily uses soft materials and relies on elastic assistance.
Cost: US$1299 (for an individual suit), or as low as $1,099 (for bulk orders)
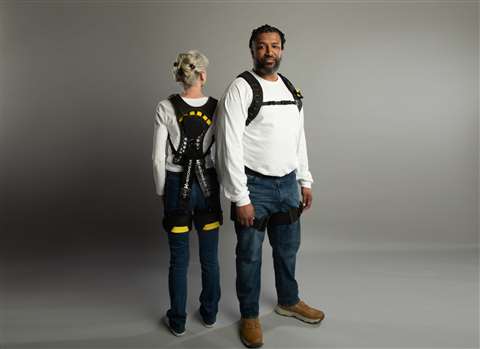
6) Hilti EXO-S and EXO-01
Hilti offers passive exoskeletons that aim to relieve strain on shoulders and arms during overhead installation work. The EXO-01 is currently available in the UK weighs 4.4lbs (2kg). The new EXO-S is available for the North American market and will launch in the UK later this year. Among the tasks Hilti envisages the exoskeleton as being useful for are: installing overhead air ducts, ventilation equipment and piping, hanging plasterboard, and fastening overhead cables and conduits. It launched the exoskeleton after developing a technology partnership with medical technology company Ottobock.
Cost: US$1,399 (for EXO-S)
7) Levitate Airframe
A passive exoskeleton that transfers the weight of the arms from the shoulders, neck and upper back to the outside of the hips. San Diego-based Levitate Technologies claims that it can lower exertion levels by up to 80%.
Cost: US$2,500
8) Sarcos Guardian XO
The as-yet-unreleased Guardian XO from robotics firm Sarcos is a full-body industrial exoskeleton. It can amplify an operator’s strength by a factor of up to 20 and carry a maximum payload of 200lbs (90kg). Sarcos also claims that a highly responsive control system allows operators to execute fall prevention motions, while a hands-free mode allows them to lock the suit’s arms and complete dextrous tasks requiring human hands while carrying a heavy load.
Cost: Unknown
STAY CONNECTED
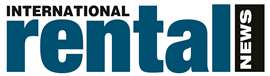


Receive the information you need when you need it through our world-leading magazines, newsletters and daily briefings.
CONNECT WITH THE TEAM
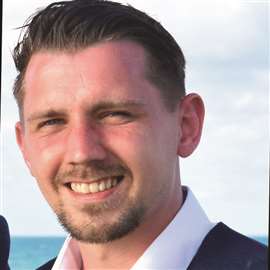
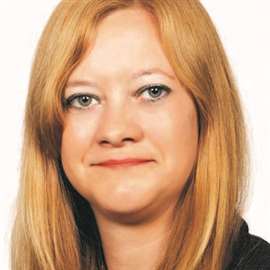
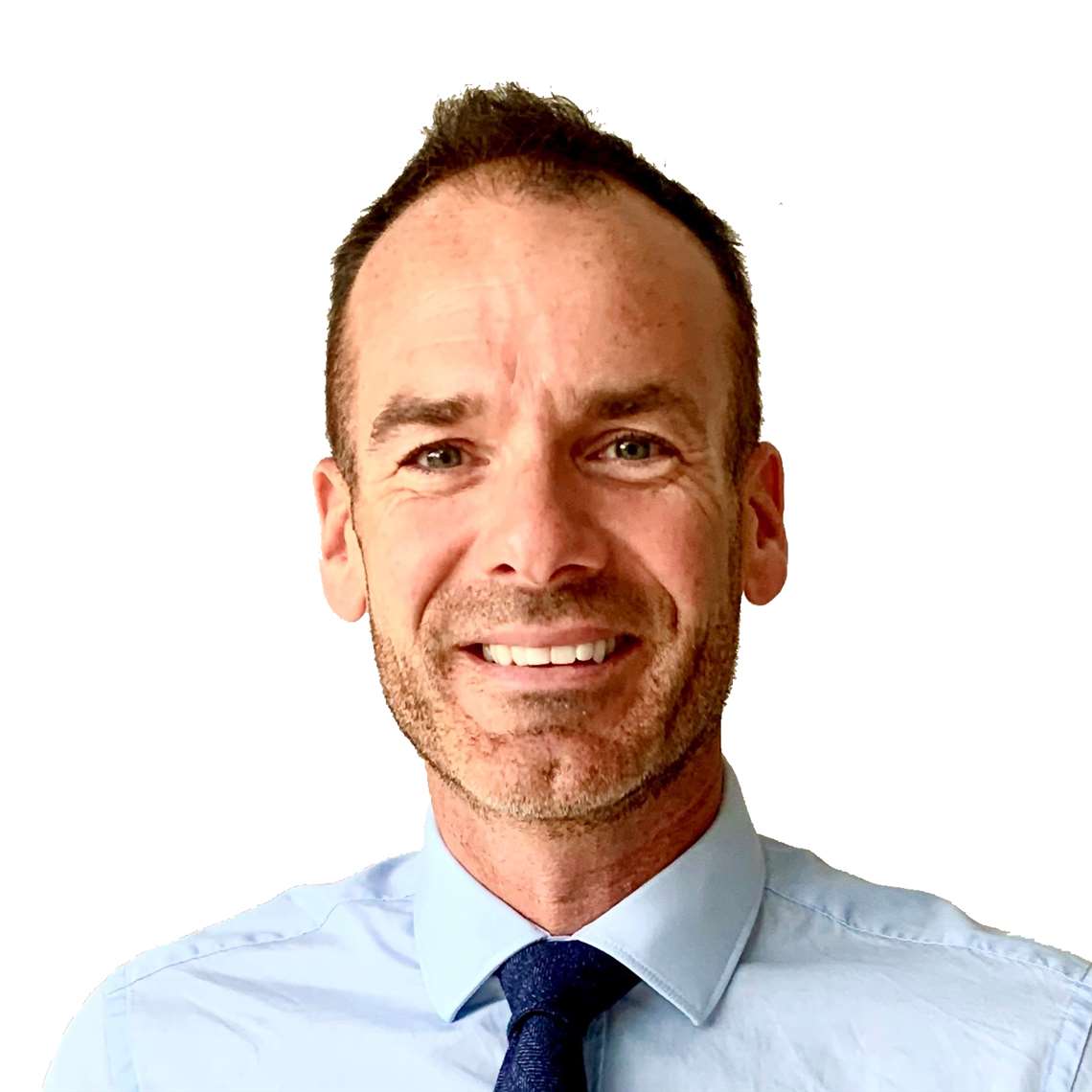