Cummins teams with Tierra on machine diagnostics
10 May 2022
Cummins and telematics service provider Topcon Tierra are collaborating to provide equipment manufacturer Liugong with advanced diagnostics and troubleshooting for major components.
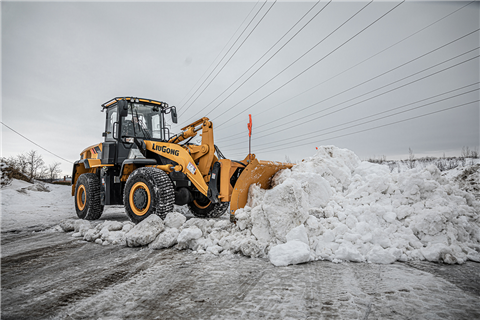
A statement on the venture said it would help Liugong, its distributors and customers to reduce machinery down time and make efficient repairs to equipment.
Through a single interface that gives users access to actionable insights that enable component care, damage prevention and faster service response, equipment availability will be improved and cost of operation will be reduced.
Cummins Connected Diagnostics wirelessly connects engines to enable continuous monitoring and diagnosis of system health and faults.
By using telematics, this digital product delivers data to fleet managers via mobile app, email or web portal.
Mohamed Abd El Salam, Tierra Product Management and Business Development Senior Manager, said, “Tierra adds new elements to its telematics solutions, offering a trusted and proven diagnostics service from Cummins.
“A system capable of adding even more value to our solutions and greater remote control of our customers’ assets, offering them higher autonomy, efficiency and a high ability to predict problems on the vehicle. This is just the first of a series of new, upcoming projects.”
Cummins is working to offer digital capabilities with existing telematics services providers like Topcon/Tierra to support customer needs in a flexible manner.
Commenting on the use of connectivity to support construction equipment, Ed Hopkins, Cummins Digital Partner Management Leader, said, “With more information end users can make more informed decisions.
“Site managers can use the data to determine whether to stop machine operation or continue to the end of the shift by understanding the suggested root causes.
“They can gain an understanding in how long they have before an issue is likely to escalate to a breakdown or critical failure. This means that uptime can be maximised, with any potential fixes done more quickly.
He added, “With the information provided in Connected Diagnostics, the correct parts, tools, and technician can be made available to resolve issues in an efficient manner.”
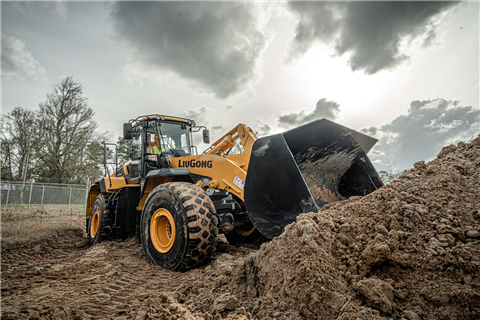
Sam Ternes, Customer Solutions Director for Liugong North America, commented, “LiuGong is proud of the collaboration with these important supplier partners and the achievement to deliver a technical solution to our dealers and customers that will directly impact machine availability.
“With this advancement in diagnostic information and communication through the TopCon telematics system Liugong will have a distinct advantage in minimising machine downtime and getting repairs completed on the first service call.
“Using the expertise and advanced capabilities of Cummins Connected Diagnostics, Liugong customers will receive timely feedback in the event of an engine related diagnostic code, allowing for continued operation where appropriate for scheduled repair, or instruction to stop operation to minimise the risk of further damage to the equipment.”
STAY CONNECTED
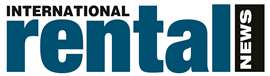


Receive the information you need when you need it through our world-leading magazines, newsletters and daily briefings.
CONNECT WITH THE TEAM
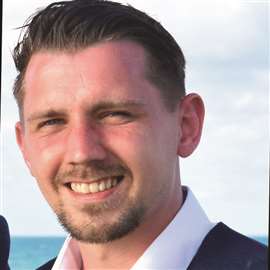
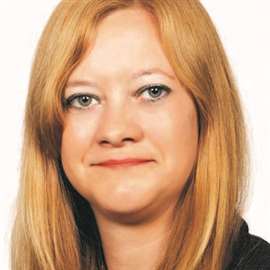
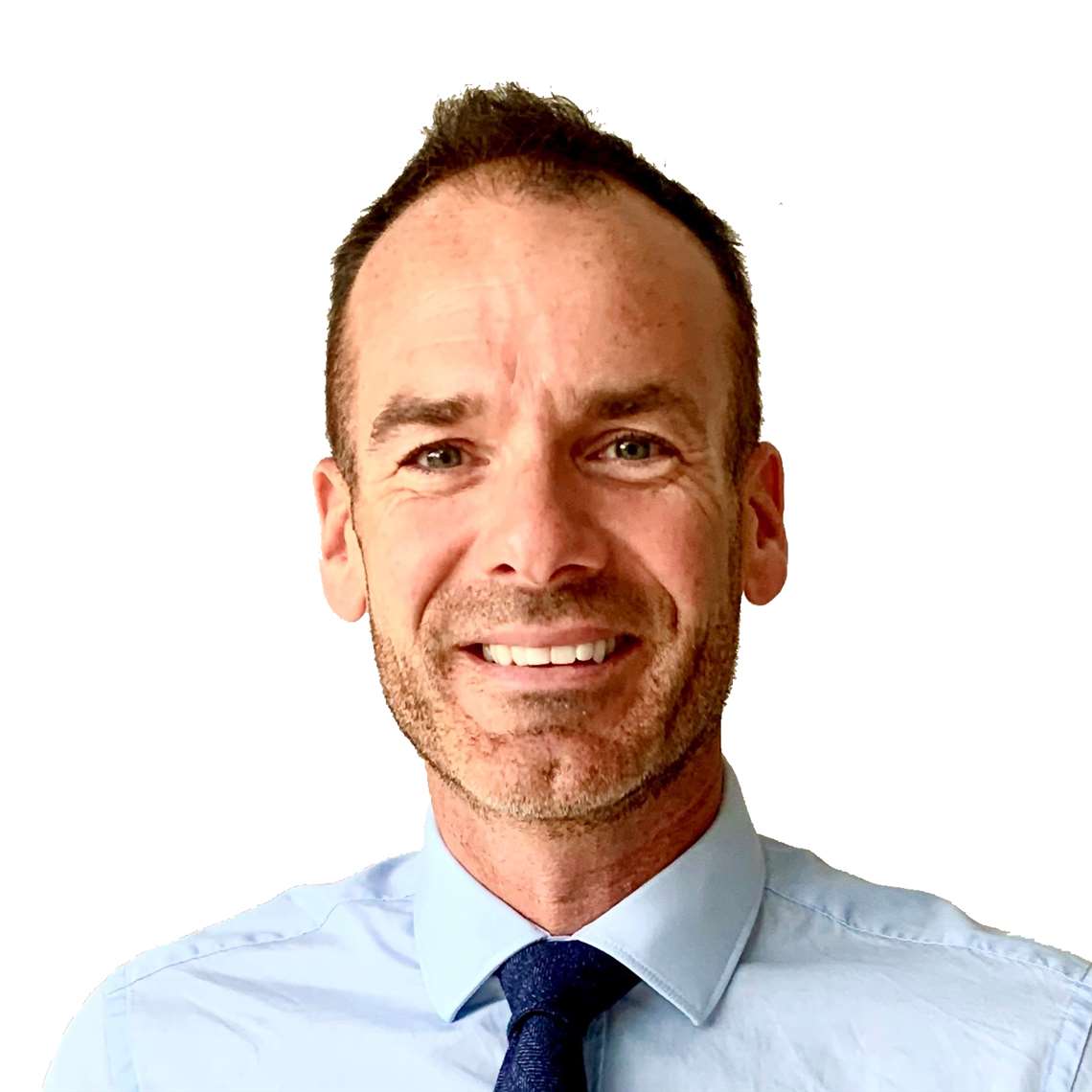