Compressor emission control: we quiz the manufacturers
23 April 2014
What technologies are the portable compressor manufacturers using to meet the latest engine emission regulations, and what will it mean for engine maintenance and servicing? IRN asked some of the biggest players.
Question One: what engine technologies have you used to meet Stage IIIB/Tier 4 Interim engine emission regulations?
Atlas Copco is using technology based on cooled exhaust gas recirculation (EGR), diesel oxidation catalyst (DOC) and diesel particulate filter (DPF) for engines in the 130-560 kW range. Tier 4 Interim compressors for the US market were introduced in 2012, powered by John Deere or Caterpillar engines.
For Europe it used Caterpillar engines with Clean Emission Module (CEM) to achieve Stage IIIB standards in the 130-560 kW range. Models were introduced at the end of 2012. The CEM comprises DOC, DPF with CRS (Cat Regeneration System).
Atlas Copco says; “One of the reasons for a DPF solution was that diesel exhaust fluid (DEF) wasn’t required for the Tier 4 Interim standard. When the interim Tier 4/Stage 3B standard was introduced, DEF on construction and mining sites was rare, meaning there weren’t any established logistic channels so it would be an additional barrier for our customers to accept the new standard.
“Our aim was that customers would not see any difference in the operation of interim Tier 4/Stage 3B compressors compared to Tier 3/Stage 3A. We integrated DPF management in our new Xc3003 controller to make it easy to operate.”
For smaller Tier IV Interim/Stage 3B compressors, the company is using John Deere, Caterpillar and Kubota engines in US and Deutz in Europe.
Kaeser was an early starter in the Stage IIIB shift, introduced its M250 and M350 compressors in 2010, powered by Mercedes-Benz Stage IIIB engines, using SCR-Cat and AdBlue technology.
At Bauma last year it showed its largest ever Mobilair unit, the M500-2, a dry-running screw compressor with a 450 kW Caterpillar engine combined with Cat’s V Clean Emissions Module (CEM) that uses DOC and DPF with CRS.
The company introduced two other IIIB units at Bauma, the M171 with a Deutz engine and the M115 with a Kubota unit. Both engines use DPF technology. Serial production of these models is projected for spring 2014.
Finally, the M114 will run with a Deutz engine with DOC and the M130 also using Deutz and requiring DPF. “Thus”, says Kaeser, “we will be able to offer portable compressors with Stage IIIB engines from 85 kW to 450 kW, which corresponds to a free air delivery range from approximately 10 to 45 m³/min.
At Doosan Portable Power, meanwhile, its large compressors are using a mix of Cummins and Caterpillar engine solutions, all using EGR technology.
Question two: what engine technologies will you use to meet Stage IV/Tier 4 Final engine emission regulations? When will these units compressors be available and in what models?
Atlas Copco will use technology that includes selective catalytic reduction (SCR) in addition to cooled EGR, DOC and DPF. The company is using Caterpillar and John Deere engines.
The company says that for Europe, cooled EGR and SCR technology was chosen because “large compressors are mostly used in construction and geothermal drilling. This work is normally done in cities, so availability of DEF is less of a problem. At the same time, EGR + SCR installation is very flexible and compact, which is important as customers expect a small footprint and low noise level.”
Conexpo will see the launch of Atlas Copco’s first Tier 4 compressor, the XATS 1050. This unit will be available with Caterpillar and John Deere engines.
Coming in the second quarter of the year will be the Drillair XRVS 1350/XRYS 577, a Tier 4 Final/Stage IV unit for the US and European markets. It will have a Caterpillar engine. Finally, in Europe in mid-2014 some 12 bar Stage IV units will be available, with larger, high-pressure compressors coming in the second quarter of 2015.
Kaeser says that its choice of engine technology will be determined by what the engine manufacturers are offering; “From today’s point of view, it seems that most engine manufacturers will focus on solutions with a particle filter, combined with an additional SCR-Cat.”
The company says this Spring will see four new Mobilair units offering free air deliveries from 10 to 17 m³/min, comprising the M114 (Deutz engine with DOC), M115 (Kubota engine with DPF), M130 (Deutz, DPF) and M171 (Deutz, DPF).
Doosan, meanwhile, says its choice of engine suppliers may result in slightly different solutions per size, although “all with common market acceptance.” Regarding the timing of new Stage IV/Tier 4 Final compressors, it says; “Introduction dates are fixed for the engine suppliers, however stock and customer demand conditions will affect/dictate the introduction dates of new machines.”
The company is about to introduce the 12/154, a Stage IV version of the current 12/150.
Question three: can you provide details of any benefits of using the new engines, such as lower fuel use or lower noise?
For Kaeser, the machines are “more economic and always meet the requirements of the acoustic emission regulations. This is not only a benefit of modern engine technologies, but also owes to more sophisticated controllers such as our SIGMA Control mobil, and to additional engineering features like for example a particularly energy-efficient ventilation-system that helps to save around 6% of diesel.”
At Doosan Portable Power, a specific benefit of the new engines is speed control, which gives enhanced performance opportunities. The company points out also that the emission regulations have triggered the development of new compressors, with “new platforms that allow us to introduce new designs and/or features, enhancing the customer experience.”
Atlas Copco has also seized opportunities offered by using the latest engines; “We decided to take the opportunity of going to Stage IV to integrate new features to improve versatility, efficiency and user friendliness.
“The new XC2003/3003 controllers provide information on a large control display and have extended logging capabilities, which is important for rental operations. The new controller, DrillAirXpert and extended pressure range will increase versatility, which can positively influence rental utilisation.”
Question four: for Stage IV/Tier 4 Final units, what will be the main changes or additional requirements for maintenance and service?
For reliable operation of Stage IV units, says Atlas Copco, ultra-low sulphur diesel fuel (ULSD) and high quality lubricants and original filters are paramount. Service interventions are “limited: DPF service interval is about every 4000 hours, whereas with a SCR solution, the DEF filter should be normally be replaced every 1000 hours.”
Kaeser highlights that electronic engine controls have already meant that service jobs have become more ambitious; “so we strongly recommend leaving maintenance to well-trained experts. Here, the trend goes towards a service contract with the operator. The additional exhaust emission treatments with SCR-Cat [and DOC] are mostly maintenance-free.”
The German manufacturer says the particle filters in its Mobilair units are automatically self-regenerating during normal operation, and adds; “The exhaust emission legislation obliges engine manufacturers to guarantee the exhaust emission values for engines below 130 kW up to 3000 hours of operation, and above 130 kW even up to 4500 hours of operation. Beyond this, engine manufacturers offer exchange programs for particle filter components.”
Doosan says that its Stage IIIB/Tier 4 Interim units introduced its customers to EGR technology and new systems like DOC and DPF where required; “Going for Stage IV/T4F the main change will be the introduction of AddBlue, as the use of Urea doping will become prevalent in Stage IV solutions.”
BOX STORY
Definitions
Diesel Exhaust Fluid (DEF): liquid additive, such as Adblue, used in modern engines that have a Selective Catalytic Reduction (SCR) system.
Exhaust gas recirculation (EGR): technique to reduce nitrogen oxide NOx emissions.
Diesel oxidation catalyst (DOC): catalytic converter that converts toxic pollutants to less toxic pollutants.
Diesel particulate filter (DPF): removes particulate matter or soot from exhaust gases.
BOX STORY
Emissions deadlines
US: Tier 4 Final
19 – 55 kW: January 2013
56 – 129 kW: January 2015
130 – 560 kW: January 2014
>560 kW: January 2014
Europe: Stage IV
37 – 55 kW: Stage IIIB limits
56 – 129 kW: October 2014
130 – 560 kW: January 2014
STAY CONNECTED
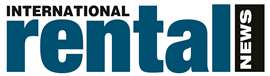


Receive the information you need when you need it through our world-leading magazines, newsletters and daily briefings.
CONNECT WITH THE TEAM
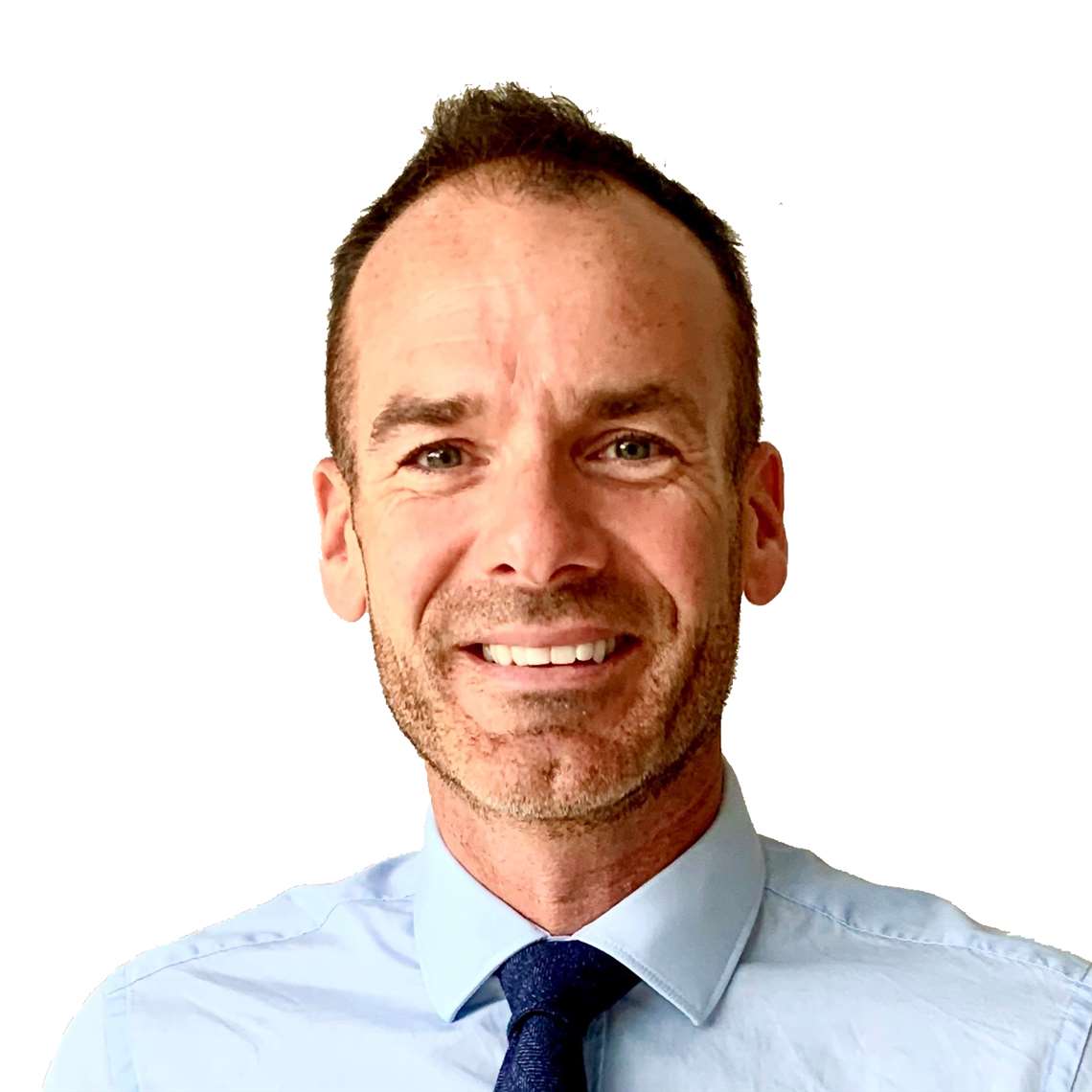
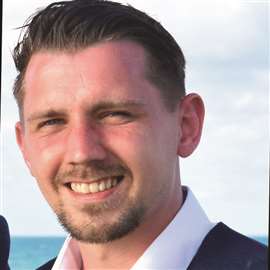