Aviation access
05 November 2018
Simon Francis, MSA Safety’s aerospace and aviation manager for WinGrip, reveals the steps you can take to minimise the risk of both injury to employees and damage to aircraft.
There is a common misconception that serious injury and death from falls happen when you’re working at great height. That simply isn’t the case. When I started my career within aviation fall protection the first two fatalities I learnt about were both from less than two metres, and in each instance, workers fell onto an access platform.
MRO aviation hangars are unique work environments; often the modern hangar needs to be able to cope with both wide and narrow-bodied aircraft positioned in different configurations at different times. Most of my working life is spent in such locations across the globe, talking with MRO’s, maintenance managers, and facilities managers about safe working at height practices and procedures. The design of hangars varies greatly from the latest state of the art facility that wouldn’t look out of place at NASA, to a more utilitarian fabricated, sometimes open-roofed model. One thing that defines them all is the need to keep to rigid time schedules, because if maintenance checks don’t start and finish on time it means an aircraft’s return to service is delayed. While an aircraft is sat in the hangar, it isn’t earning money, and that is not good for business.
Starting place
Let’s start with our goal. What is it? To catch people when they fall, or to help prevent them falling in the first place? For any viable business, it must be the latter. Why? Because a fall can not only be catastrophic in terms of the human factor, but a fall can also damage aircraft. Minimise the risk of a fall and you reduce the risk of damage; the equation is that simple.
Of course, we all feel a moral obligation to help keep our colleagues safe when going about their work, but a fall can cause damage to an aircraft as well. This isn’t surprising as we’re talking about 2.5 – 3 tonnes of dynamic load being exerted on a wing, fuselage or stabiliser. A restraint system, which is used in accordance with the OEM’s guidelines and following thorough training, minimises the risk of a fall. If, however a fall were to occur, our system absorbs and dissipates the load generated, to better protect both the user and the airframe. Always dig deep in your research and question how systems work, what surface they have been tested on (i.e. alloys/composites) and what operating conditions they are approved for.
Safety first
In an ideal world, work-at-height safety planning will start at the blueprint stage, so lines and systems are an integral part of the hangar design. Forward planning inevitably cuts costs and maximises safety as your permanent system is ready and waiting before any aircraft appears.
Whether you access aircraft via platforms, MEWPS, ladders or staging, typically there will be a significant amount of GSE (ground service equipment) around – and this creates the added risk of limited fall clearance. Again – in the ideal world you would have total clearance underneath a wing or stabiliser, but in the vast majority of busy hangars, this simply isn’t possible.
Advising my clients on access is very important – but access is the tip of the iceberg. Once your worker is at height, how do they then access the area of the fuselage, wing or stabiliser that they need to reach?
User-friendly
If equipment is light, easy to install and allows freedom of movement to go about maintenance or construction tasks after training, it will be used. If it’s heavy, complex to set-up and restricts movement then workers are more likely to avoid using it.
Unplanned tasks
It’s often not the B, C or D checks that are likely to result in accidents (although they still do) as these are typically scheduled and well planned with strict procedures and documented tooling including safety equipment. It is often the unscheduled task that can compromise safety. Where work at height safety is concerned, it is never worth taking the risk; that five-minute job where a technician accesses an aircraft structure with no safety equipment, could result in a life-changing injury or worse, and in addition cost hours of lost productivity and potentially lost business.
Safety systems
Your business is about the maintenance and repair of multi-million-dollar aircraft, so you obviously want to attract and retain the very best maintenance technicians. By ensuring their safety when working at height, you are showcasing your partnership approach and that you value their skill, input, and their life. High quality safety equipment gives both management and workers peace of mind. It’s also an aid to productivity. Your crew needs to be able to concentrate on the task in hand; supplying top class safety systems enables all the work focus to be on repair and maintenance.
Commitment to Excelllence
Your customers want to know your operation will deliver best practice in MRO – they are entrusting their aircraft and reputation to you and your team. If they see your workers taking risks with either no or inadequate safety provision, they might subliminally wonder what other corners you are cutting.
Tips to prottect the team
- Check the products and equipment you are using for working-at-height comply with all relevant legislations and standards.
- Schedule regular maintenance checks for all PPE and safety systems.
- Confirm that the workers who need to use the safety devices receive the correct training.
- Build a culture of safety in your team.
- Include safety equipment on your tooling list and require that it is used for all work at height tasks – including ad-hoc work.
Simon Francis, MSA Safety’s aerospace and aviation manager for WinGrip, reveals the steps you can take to minimise the risk of both injury to employees and damage to aircraft.
There is a common misconception that serious injury and death from falls happen when you’re working at great height. That simply isn’t the case. When I started my career within aviation fall protection the first two fatalities I learnt about were both from less than two metres, and in each instance, workers fell onto an access platform.
Starting place
Safety first
User-friendly fall protection
Unplanned tasks
Quality safety systems
Demonstrate your commitment to excellence
Tips to protect the team
Check the products and equipment you are using for working-at-height comply with all relevant legislations and standards.
Schedule regular maintenance checks for all PPE and safety systems.
Confirm that the workers who need to use the safety devices receive the correct training.
Build a culture of safety in your team.
Include safety equipment on your tooling list and require that it is used for all work at height tasks – including ad-hoc work.
STAY CONNECTED
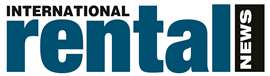


Receive the information you need when you need it through our world-leading magazines, newsletters and daily briefings.
CONNECT WITH THE TEAM
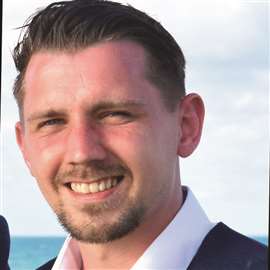
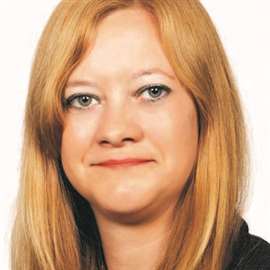
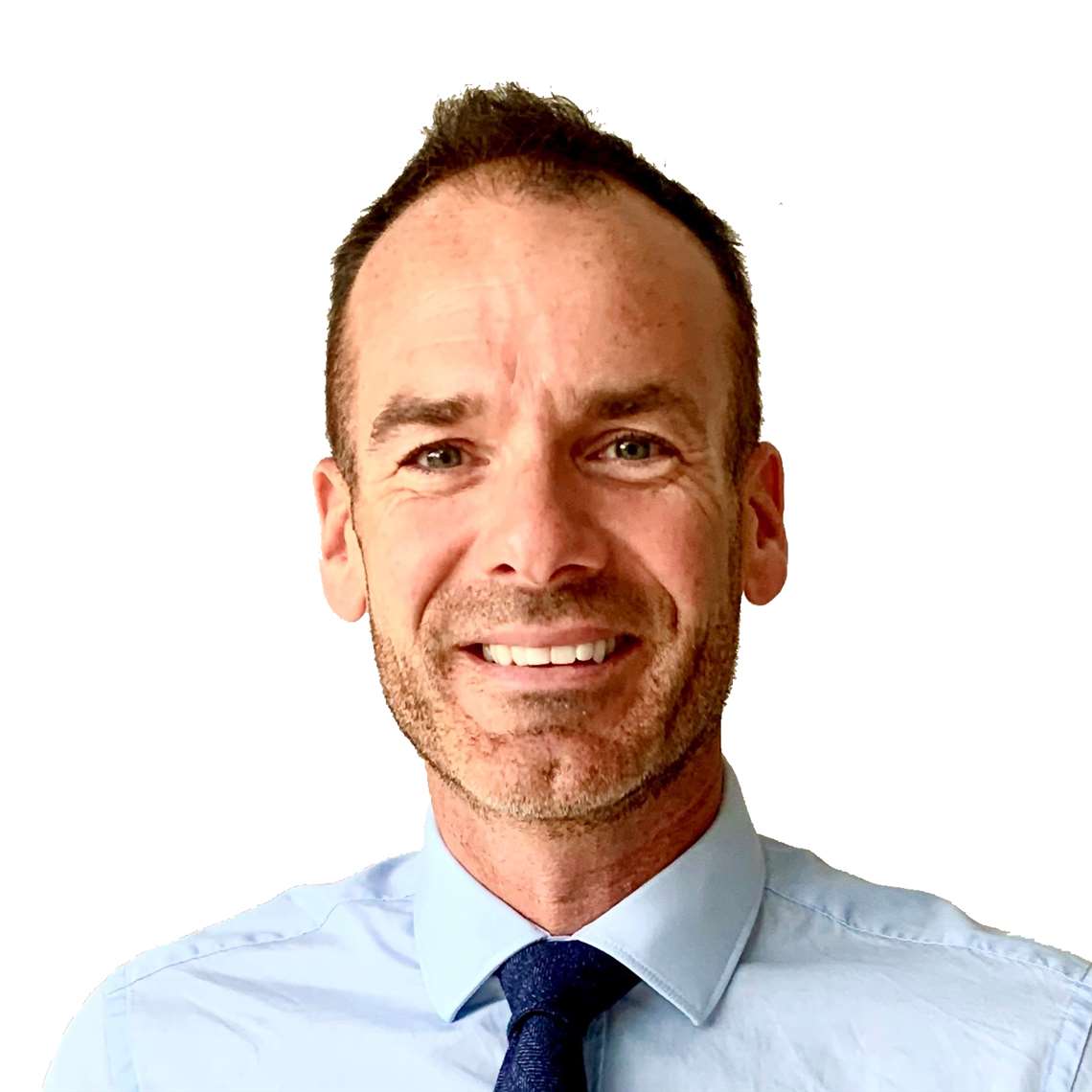