Market review: Mast climbers and hoists
12 July 2021
Lindsey Anderson examines the North American mast climbing and hoist market’s strategies that kept companies afloat during the global pandemic
The mast climbing and hoist market is trending upward, in stark contrast to many industries who are still finding their footing after work and life stuttered through the global Covid-19 pandemic.
These past 12 months were interesting to watch through the lens of the burgeoning mast climbing and hoist industry. From numerous acquisitions by one of the world’s largest providers of access and scaffolding systems, to the coronavirus’ crushing blow on construction, there has been plenty of ups and downs during the past 365 days.
Jacques Lainé, corporate affairs and marketing for Canada-based Fraco Products – who provide equipment to condo construction, demolition, forming operations, glazing and masonry – explained that the company has experienced growth in the mast and hoist sector.
Lainé said, “Looking back at the year, we feel very fortunate to have operated in an industry that experienced growth during the pandemic.
Business adapted to post-pandemic reality
“The uncertainty was omnipresent back in March 2020, and it was difficult to predict how things would turn. Of course we struggled in the beginning, and we had challenges over the year.
“But overall we adapted, and we stayed flexible in order to be ready for what came next. The demand was there, but the difficult part was keeping up with it on top of the price increases for materials and lack of labor.
“The demand for work platforms was so high that we had trouble keeping up in the spring/winter of 2021. We also noticed an increase interest for the hoists, because of the social distancing regulations.
“Our guess is that the shortage of labor has pushed contractors to invest in machines that can help their teams be more productive.”
Lainé added that Fraco believes growth will continue. He enthused about the company working towards “perfecting” their 3,000lb capacity FMC-3 mast climber, which will be available to the market soon.
He claimed, “The FMC-3’s lightweight features will make it a great tool for masons and contractors looking to work with smaller, more flexible machines.
“We have also added Spanish products to our product line. We now offer the PL-15 transport platform, a temporary elevator that can handle a load capacity of 3,300lbs in a smaller price range.
“We feel that there will not be a slump in construction, but commercial building development may start to slow down. Overall we are ready to be busy, maybe less in the housing market.
“On the other hand, condo building projects remain dynamic – a phenomenon that is coherent with the growth of the larger metropolitan areas and suburbs. Numerous multi-residential buildings projects are being started in the most populous North American areas, with many more than 50 storeys high.”
The Millstone Companies – which provides scaffolding, suspended scaffolding, shoring, hoisting and related access products to the market in the Mid-Atlantic region – also came out of 2020 on a positive note.
Yet John Miller, president and CEO of the Maryland-based business, admitted that there have been slight hiccups this year.
Miller said, “We did not miss a beat once we were deemed to be essential in March 2020. We continued working throughout 2020 with enhanced safety protocols in place with occasional project delays, usually one to three days due to periodic jobsite cleaning when positive Covid-19 cases were reported by companies with workers onsite.
“Overall, 2020 remained a profitable year despite Covid-19, but we blew through most of our backlog. In addition, 2020 was a contentious election year, for which many took pause in the second half until we had election clarity and some direction going forward.
“Construction usually takes about six months to feel the effects of adverse events, which shook the system. As a result, the first quarter of this year did get off to a slow start but it seems to be coming back around now. We are projecting a strong second half.”
He expects growth going forward, yet sensibly remains cautious.
Miller tentatively added, “We need to keep an eye on inflation as construction materials, manpower and freight are all up considerably. But with availability problematic, this could affect some project starts.
“We are seeing strong demand for high-speed hoisting, with oversized cars to accommodate the large curtain wall panels coming in from abroad. We continue to see regulators still trying to lump construction hoists into elevator codes for which they don’t apply.”
Achieving results by being resilient and resourceful
Mike Pitt, owner of Georgia-based Mastclimbers LLC, reported that the past 12 months were good for his company who service and rebuild programs for all makes and models of hoists, mastclimbers and transport platforms on top of supplying mast climber rentals, sales and training.
He stated, “We have won new projects we did not expect. We have had work delayed and had work cancelled, but overall we have done okay.
“We continue to develop new and existing markets. Talking to other mast climbing and hoist fleet owners, we can see people using the same products in different markets and in different ways. So I am confident more end-users will continue to find new ways to use our equipment. We just need manufacturers to continue to come up with new products at prices that reflect the savings to the end-users
“European manufacturers are still continuing to look at the US market, but not until they can travel. We have some big contracts coming, so our growth will continue.”
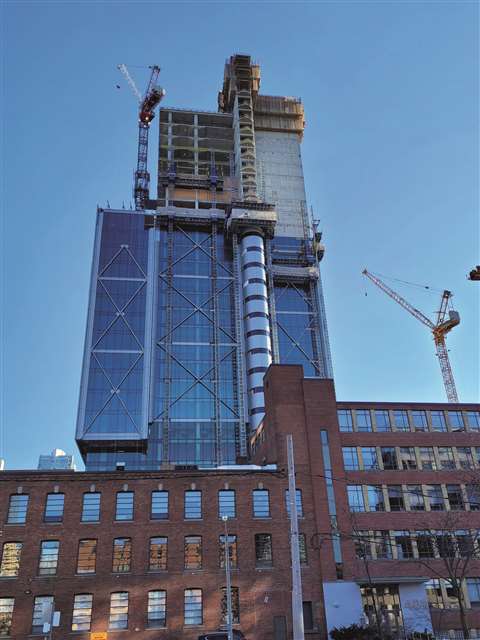
Klimer Platforms – whose mast-climbing work platforms (MCWP) and transport platforms are a proven alternative to suspended scaffold, fixed scaffold, lifts and other traditional access methods – are expecting to see an increase in demand for the remainder of 2021.
The Ontario-based mast climbing and transport platform company found the first eight months of the Covid-19 pandemic particularly difficult.
Christine Gordon, the HR/office administrator with Klimer, said, “We suffered approximately a 20 per cent drop in forecasted revenues. During the pandemic certain jobsites were affected due to the nature of the work, which resulted in some jobsites being closed or delayed.
“Efficiencies went down and operational labor costs increased as with most industries. Overall, we were fortunate enough to remain relatively busy throughout the pandemic.”
The Canada business currently has equipment on a number of jobs, including one on Toronto’s West End that requires a specialized solution. Klimer developed a material handling and access solution to facilitate the installation of 14ft high panels, with weights up to 1,400lbs, on shear wall areas of a new 40-storey commercial/residential building.
The system was required to pick up curtain wall panels and architectural feature panels from the slab edge adjacent to the shear walls, transport the panels around the perimeter and position them so that the glaziers could reach the top and bottom of the panels for installation.
Klimer collaborated with Engineered Lifting Systems to design and manufacture components of the translating monorail system, used to provide a continuous material pathway around the building’s irregular shape.
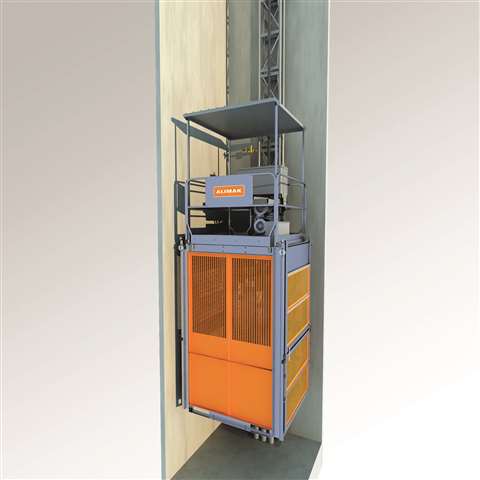
Modifying services has reaping the benefits
Texas-based Alimak Group, a world-leading provider of vertical access solutions for professional use, is wary of the debilitating effects and economic costs caused by the sudden arrival of the Covid-19 pandemic.
David Batson, EVP construction division with the Alimak Group, slammed, “The construction industry is on the brink of significant change and disruption. Previously it was only considered if change will come, but it’s now a matter of when.
“As the ecosystem of a construction site moves and adapts, players need to move quickly or be left behind.
“The logistics and supply chain and the digitalization of that is something being embraced, and it is moving quickly in many markets globally along with sustainability. Not only in the end products being constructed, but the whole supply chain and its contribution to its impact on society and the environment.”
With an eye on global trends and the increasing need for enhanced efficiency and productivity, Alimak launched the LSH construction hoist at the bauma CHINA 2020 exhibition.
Designed for use inside elevator shafts during building construction, the LSH was designed to be installed inside an elevator shaft by tower cranes and takes half the time of a traction jump-lift.
The LSH is also able to serve the top level of the construction site, due to the rack and pinion technology used. It also has a large seven-inch display control panel in a stainless steel casing. The touchscreen boasts protective glass and ingress protection to IP54, while Alimak’s intelligent hoist monitoring system delivers real-time status information.
Intelligence is a vital element of current and future Alimak product design. All new Alimak Scando construction hoists are equipped with remote diagnostics systems.
The Alimak Group says it can provide new services to optimize utilization for different applications, predictive maintenance to improve uptime, automate safety and calibration measures to improve ease-of-use.
Oregon-based Morrow Equipment Company LLC, which owns and operates the largest fleet of tower cranes in North America, recently ordered 36 construction hoists from the Alimak Group.
Peter Juhren, president and COO with Morrow, enthused, “We know Alimak is the leader in technology and quality, so we are pleased to grow this relationship further.”
BrandSafway – a leading global provider of specialized access services as well as forming and shoring solutions to the commercial, industrial and infrastructure markets – was recently called upon to assist with a tricky smokestack demolition.
Tate & Lyle, an international provider of food ingredients and solutions, needed to deconstruct and replace an old boiler house at one of their grain processing plants in the Midwest.
Their facility had two smokestacks located next to the boiler house, measuring 230ft and 330ft high respectively, and a third steel stack that rose out of the roof of the boiler house. All three needed to be taken down to accommodate the company’s long-term plan. The towers also stood very close to a pipe system that fed corn to the rest of the facility, and could not be damaged.
To ensure that no debris would fall on the outside of the smokestacks during demolition, which could potentially damage the surrounding facilities and piping, the towers had to be dismantled starting at the top. Then any broken concrete would be pushed down through the center and carted out at the bottom via an existing debris hole.
However, providing access to a tower as its being torn apart poses unique challenges. One traditional solution would have been to fully scaffold the tower, and then dismantling it as each layer of the smokestack fell. Yet this option would have been time, labor and material intensive on top of proving costly.
Another alternative might have involved using crane baskets to lift workers with jackhammers to the top and having them demolish the tower while suspended. But BrandSafway had yet another alternate approach, which would be both safer and more efficient.
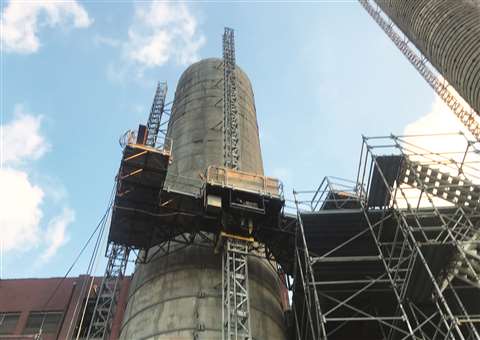
Robots to the rescue to improve safety on site
BrandSafway opted to use Brokk 90 demolition robots, remote-controlled demolition machines with jackhammer-like tools attached to a controllable arm, and SafRise mast climbers to complete the job.
Their Brokk 90 robots were lifted to height on top of three SafRise units, which feature a single-mast capacity of 8,000lbs and the ability to reach heights up to 500ft.
The custom “bridges”, engineered by Hydro Mobile for BrandSafway, were utilised to accommodate the width and weight of the robots. These bridges were added to the mast climbers, connecting all of them together and granting the machines complete access all the way around each tower.
Using robots was more efficient due to their destructive power and it was also safer, as it meant that fewer workers had to be sent up to that height.
Bill Beaman, VP and project manager for Illinois-based American Demolition Corporation – the general contractor for the $1.3 million project completed in September 2020 – explained, “With this approach there was no one hanging off the end of the stack and no major fall protection challenges, which made it a great solution from a safety standpoint.”
No job is without its challenges. The first issue that BrandSafway faced was that the piping around the towers limited the possible positions of the mast climbers. Those limitations meant that a mast climber needed to be placed directly in front of the precut debris hole of one of the smokestacks.
Unable to be moved left or right, the mast climber had to be moved up. So BrandSafway built a custom shoring platform capable of supporting the weight of a mast climber, using Systems™ Scaffold, and a demolition bot as well as the reactive forces generated by the machines. With the mast climber resting on top of the platform, the underside was left open and allowed workers access to the debris hole to cart out rubble.
Another challenge was keeping the mast climbers in place. The mast climbers needed to be tied to the smokestack for stability, but the force of the robots breaking through the concrete tower was greater than what standard clamp-style connections could handle.
BrandSafway utilized Telespar ties, pin-style connections designed to withstand either long-tie applications or demanding conditions. These were then cut to size and attached, eventually being removed as each section of the smokestack fell.
Beaman concluded, “I couldn’t be happier with the result, it was the most efficient and cost-effective approach. It enabled American Demolition to significantly reduce the labor and labor dollars that it would’ve taken to demolish the stack.”
STAY CONNECTED
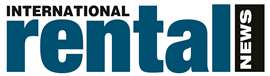


Receive the information you need when you need it through our world-leading magazines, newsletters and daily briefings.
CONNECT WITH THE TEAM
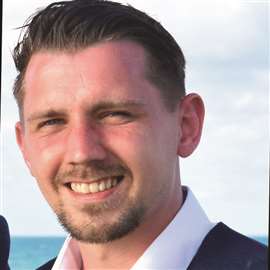
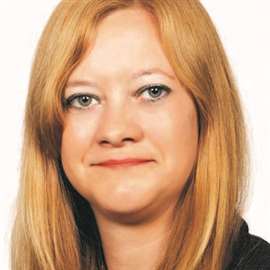
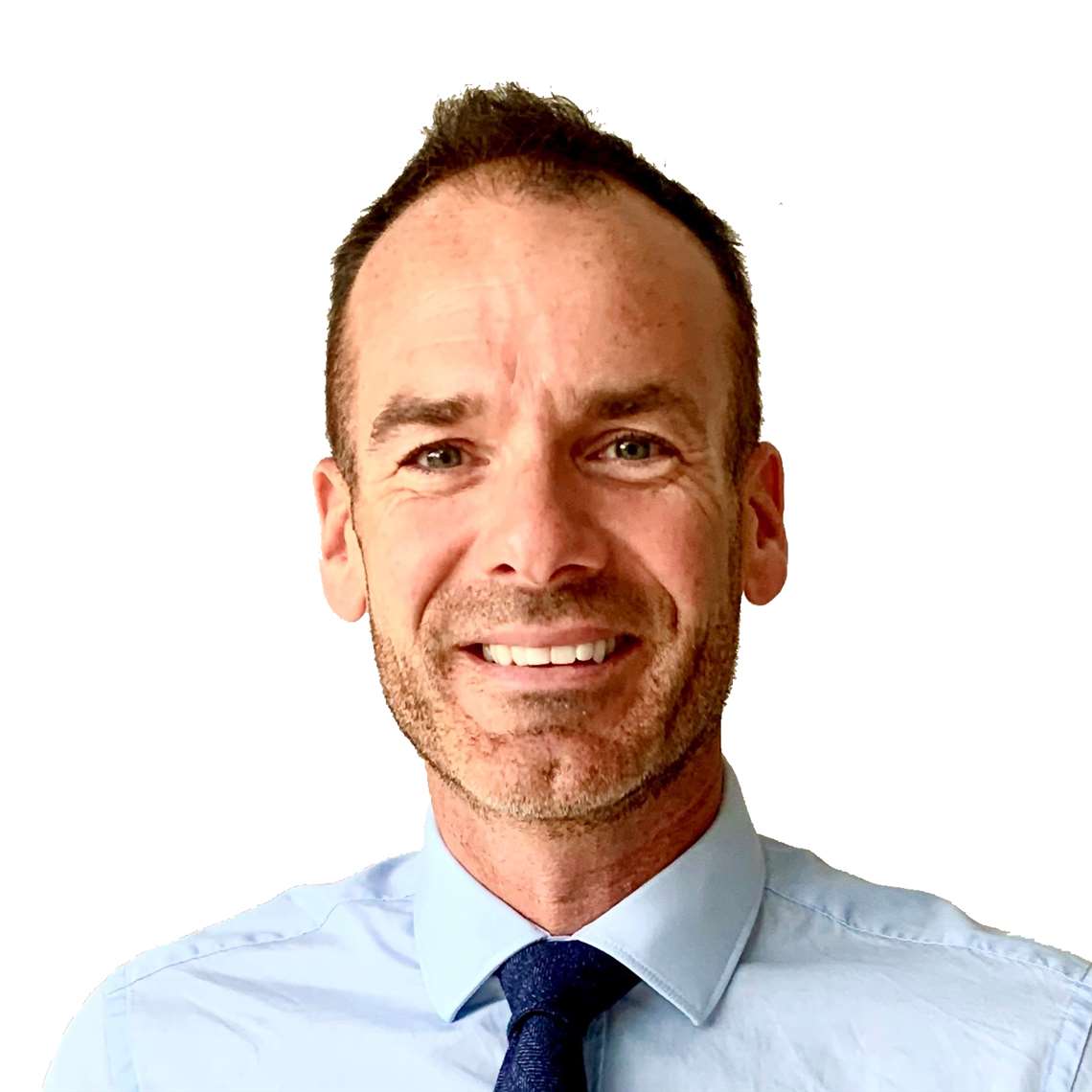