HAE: Prevention is better than cure
20 August 2020
Thankfully, most construction projects are completed without serious injury, due to careful health and safety planning in advance of the start of a project, coupled with the ongoing vigilance, cooperation and professionalism of workers during the build. Hazard recognition plays a key role in preventing accidents and some hazards are obvious, like the requirements for people working at height, but other hazards such as the safe operation of rented earthmoving equipment could be less so.
The latest annual figures from the Health & Safety Executive (HSE) reveal that there is at least one accident involving a digger or dumper each week on sites in the UK, with the majority caused by unstable ground or unsafe working practices – an industry challenge that must be met head on by all stakeholders if the frequency of incidents is to be reduced.
Construction remains dangerous
Although the UK consistently has one of the lowest rates of work-related fatal injuries across the European Union, HSE statistics also show that 30 people were killed on construction sites between April 2018 and March 2019, and construction continues to account for more workplace deaths than any sector other than farming. These tragic incidents are often swiftly followed by costly court proceedings and hefty fines for the companies found to be culpable.
In terms of legislation, those companies or persons implicated in such a court case could be prosecuted on numerous grounds. Firstly, under the Health and Safety at Work Act because employers have a duty of care to maintain a safe working environment, and furthermore, depending on the circumstances, in the event of a fatality they could also be found personally liable under the Corporate Manslaughter and Corporate Homicide Act. A whole raft of associated legislation can also be drawn upon in the event of rental equipment-related incidents, such as The Management of Health and Safety at Work Regulations, or even the Road Traffic Act in relation to earthmoving vehicles.
It also pays to remember that incidents involving rented equipment can have grave consequences across the board. The knock-on effects can be far reaching in terms of the mental health of family and co-workers and the damage done to the reputation of the implicated firm is very difficult to undo.
Businesses of all sizes
Many companies are proactively investing in health and safety training and reviewing their policies and processes in order to avoid accidents and even potential criminal proceedings against them. It would be easy to believe that safety improvement activity in the construction supply chain is driven solely by bigger and better financed companies. But in fact, small to medium-sized independent firms account for 62% of the total turnover for the UK construction industry. Clearly, if the level of safe working is to be improved, businesses of all sizes need to address health and safety matters as part of their core business strategy and policy.
Construction sites are inherently dangerous places to work, but prevention is always better than cure, and putting pre-emptive measures in place rather than waiting for an incident to occur can save rental companies time, money and ultimately lives. Key plant manufacturers coming together across the board and agreeing on improvements to the safety standards of earthmoving rental equipment and working practices could lead to a significant reduction in incidents. The HSE statistics clearly demonstrate that we cannot afford to become complacent in the equipment rental industry in preventing injury, ill health and death at work.
Learning from tragedy
A tragic accident involving a dumper truck in 2018 proved the catalyst for the formation of such an initiative between HAE member rental companies. The Digger and Dumper Operational Safety Group brought together by Hire Association Europe (HAE), consists of likeminded rental companies and equipment manufacturers. The group’s focus involves improving the recording of incidents, reviewing standards, engaging with manufacturers and making the sector aware of potential issues.
By working together to gather and analyse reliable data, companies can agree a framework, including training and education, that will further improve safety standards by ensuring that their operators are fully competent in handling earthmoving machinery and are aware of the risks associated with their actions.
Because of the wide range of contributory factors leading to digger and dumper related incidents, rather than taking a scatter-gun approach, the group aims to analyse the data gathered in a way that leads to action being taken to address the root causes, be they equipment design, poor training or other related factors. For example, one of the group’s goals is to determine any trends related to specific types of equipment. This may then help to determine the root causes and relevant factors leading to the incidents. This information can thus be used as a basis on which to develop a meaningful dialogue with the manufacturers of this type of equipment in order to agree a way forward for future products.
Long-term view
Engaging with the broader sphere of health and safety in this structured, in-depth way means that the whole process takes a long-term view and is not simply based on maintaining the status quo or merely making retrospective improvements to existing machinery.
Similarly, there may be risk factors that involve specific staff or customer issues, for example, a rental company may be adhering to exemplary health and safety standards, but perhaps the customer renting earthmoving equipment may have refused to accept the familiarisation briefing on offer. Again, if such factors can be systematically recorded and analysed by rental companies working together to collate information, industry standards can be agreed upon to try and eliminate as many of these risks as possible.
Despite initiatives such as these, getting tool and machine rental companies on board with more robust safety measures can still be a challenge. Agreed standards can be put in place, but ensuring staff compliance presents its own set of issues. Some may view making such changes as an additional strain on resources and may feel that they lack the manpower, time or budget to implement further training or maintain compliance checks. However, health and safety compliance extends to far more than just the work done on-site. Ensuring adequate staff training is vital, and the way in which health and safety is communicated as a whole needs to be conveyed in a manner that resonates with staff, encouraging them to remain engaged and boosting a positive company morale.
Creating incentives
As a means of incentivising positive change and overcoming these barriers, HAE researched and created the SafeHire Certification Scheme which was formalised into a private standard by the British Standards Institute. The HAE scheme is a mandatory requirement to maintain membership and HAE is now working to raise awareness of the SafeHire scheme at local and national governmental levels.
In order for rental firms to achieve certification, participation in the SafeHire scheme requires that businesses are inspected annually and everything, from paperwork, day-to-day operations and maintenance, to staff training and environment, is checked for continued compliance with the scheme’s rigorous standards.
Formal certification
Having formal certification in place, such as SafeHire enables customers to approach tool and machine rental companies with confidence, as it proves a firm’s competence in upholding high standards in health, safety, environment and quality of equipment as well as a well-trained workforce to support customers as fully as possible. Furthermore, in the unfortunate event of an incident escalating to litigation, the benefits of being part of a nationally accredited health and safety scheme cannot be underestimated. Evidence demonstrating health and safety compliance can be easily drawn upon if needed and there is also the increased credibility that formal accreditation adds to a rental company’s reputation and profile. Being part of a wider scheme or professional body may also provide access to an independent arbitrator should that be necessary.
Countering any concerns about the burden on resources, schemes such as the Digger and Dumper Operational Safety Group and SafeHire certification demonstrate that accurate, vigorously researched and credible options are available to the tool and machine rental sector that not only mitigate the risk of future incidents, but also bolster customer confidence and ultimately help the bottom line.
About the author
Carl Bartlett is the Executive Director of Certification Services at Hire Association Europe, responsible for overseeing HAE’s SafeHire scheme, a business improvement programme providing safety certification to tool and machine rental companies.
Bartlett can be contacted at [email protected], and you can find more information about the SafeHire scheme at www.safehire.org.uk
STAY CONNECTED
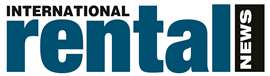


Receive the information you need when you need it through our world-leading magazines, newsletters and daily briefings.
CONNECT WITH THE TEAM
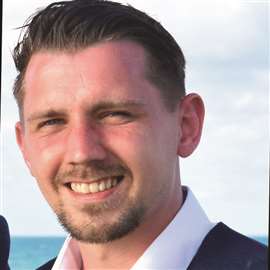
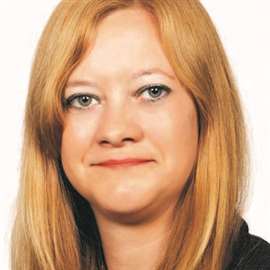
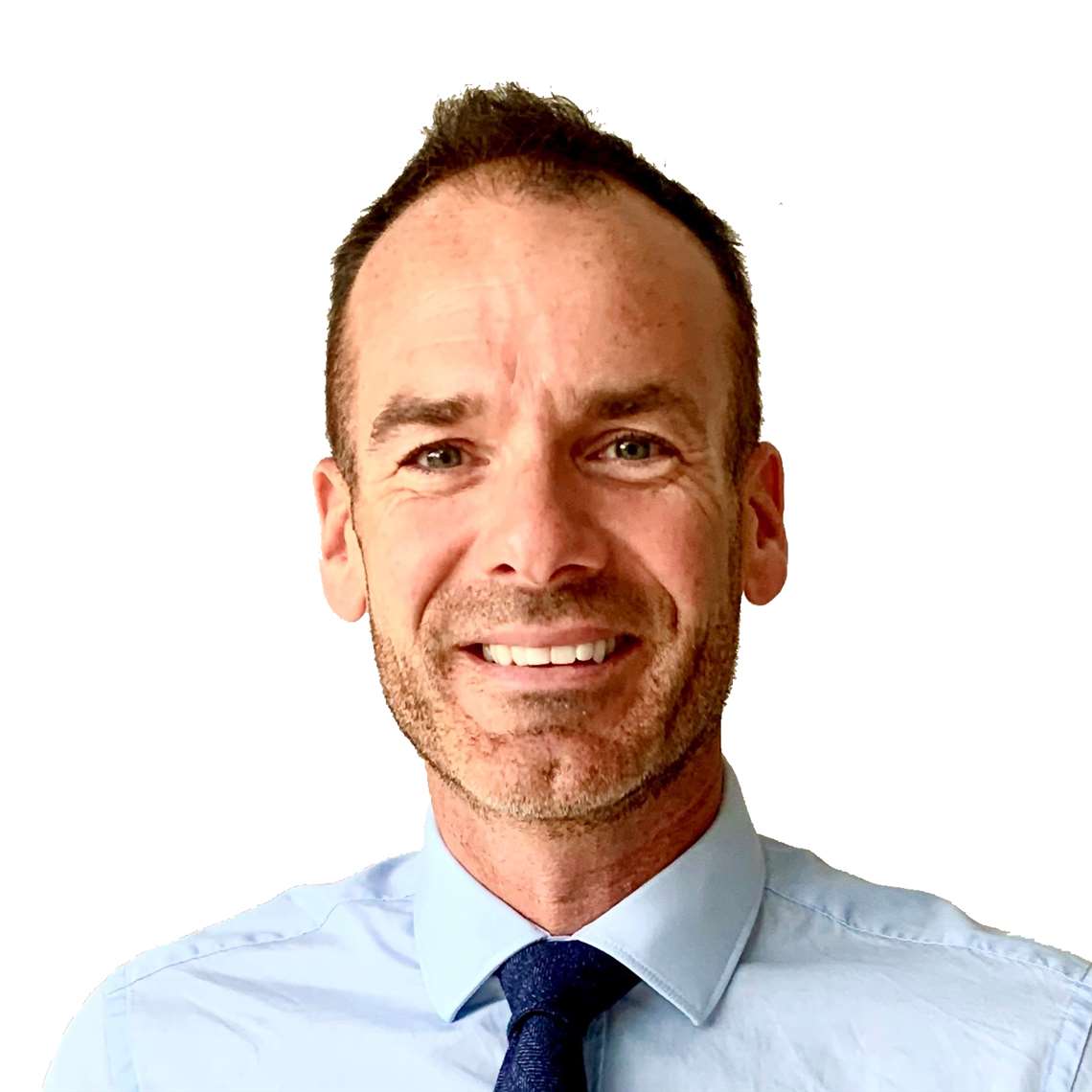