Compact Equipment Leads Charge in Off-highway Electrification
02 August 2022
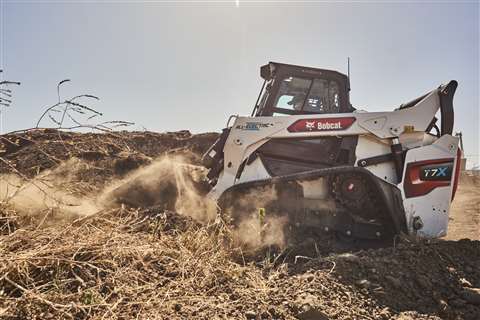
The advancement of electrification into off-highway equipment has gained substantial momentum as of late as OEMs seek solutions to help customers meet expanding emissions regulations and decarbonization objectives. For many, efforts to move electric machine solutions from proof of concept to series production have taken on a renewed sense of urgency.
Growing customer interest, and acceptance, of electric power are key contributors. “Customer interest trends continue to climb for off-highway battery electric vehicle (BEV) applications, with some market segments reaching as high as two-thirds of customers that are ready and willing to adopt a BEV,” noted Jennifer Preston, director of John Deere Electric Powertrain, CEO, Kreisel Electric (which was acquired by John Deere in early 2022).
“The OEMs we work with are seeing that there is a willingness from their customers to pay a premium for the benefits of electric power. Because of this, manufacturers are realizing they need to include battery-powered equipment in their offerings to be competitive,” said Nick Moore, director of product management for Electrification, Briggs & Stratton.
Where the industry has seen the greatest degree of actualization has been in compact equipment. “Battery capacity density has made it more feasible to easily convert equipment that has a limited footprint,” said Moore, “allowing more OEMs to quickly move toward their electrification goals.”
Providing equivalent performance
While numerous construction equipment manufacturers have shown electric variants of machines, only a select group have announced availability of models ready for serial production.
Volvo Construction Equipment (Volvo CE) counts itself among the first and currently offers five compact models – the L20 Electric and L25 Electric compact wheel loaders and the EC18, ECR18 and ECR25 Electric compact excavators. All five models are available to order, with the L25 and ECR25 Electric currently in use in Europe and deliveries to North American customers set to begin this summer. Deliveries of the three remaining models will start in 2023.
In early 2022, Bobcat Co. announced availability of three electric models, the E10e and E32e electric compact excavators, which use lithium-ion batteries with traditional hydraulics driven off the battery pack, and the T7X all-electric compact track loader, which replaces the hydraulic pump and motor with electric drives and electric actuators. The E32e and T7X are scheduled to begin production in July, while the E10e is currently in production at Bobcat’s plant near Prague, Czech Republic.
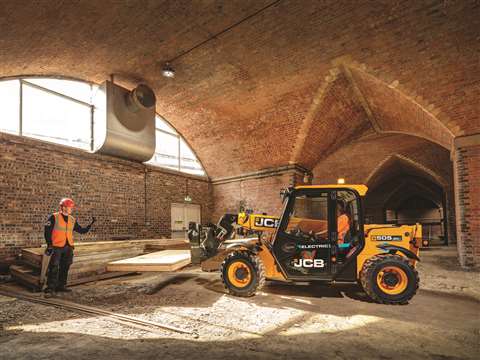
JCB is yet another supplier offering several models, and types, of compact electric equipment, including the 19C-1E compact excavator, 505-20E compact telehandler, 66-40E Teletruk, HTD-5E electric dumpster and several models of scissor lifts. According to Ashby Graham, general manager - production & marketing, overall response to the electric machines has been positive.
“Customers are impressed by the ease of use of the equipment and the ability to utilize their machinery in an even larger variety of applications,” she said. “Performance capability is probably the biggest objection or concern customers have about battery powered equipment. And the easiest way to help customers understand that battery powered equipment performs just as well as the diesel variant is to have them try out the equipment so they can see for themselves.”
Volvo CE’s electric compact excavators and wheel loaders “have nearly identical specs as their diesel counterparts, maintaining or exceeding the power of the diesel models,” according to Lars Arnold, electromobility product manager. This means they can be used on any jobsite where you would find diesel-powered machines.
“When some people think about electric-powered construction equipment, they tend to jump to the conclusion that it will be inferior to a diesel machine in some way – mainly power,” Arnold said. “That’s not the case at all.” In fact, he said customer feedback following operation is that “they feel the electric machines are more powerful and reactive.”
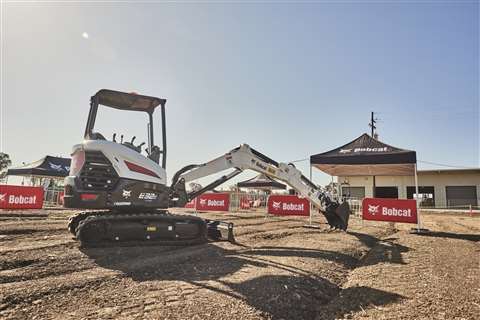
In May, Bobcat brought together experienced equipment operators for a road show in California and let them put its electric machines through their paces. “We had some really good operators out there, and all of them go, ‘Hey, that’s a really good machine that performs just as good if not better than the diesel machine,’ which is a compliment… that they’re diesel-hydraulic equivalent,” said Joel Honeyman, vice president of Global Innovation, Bobcat Co. “That’s what you’re trying to do.”
Battery electric machines can even offer certain performance advantages in some cases. For example, Volvo CE’s ECR25 Electric excavator offers a slight increase in continuous motor power and the L25 Electric wheel loader has a higher static tipping load, with both offering marginally higher operating weights than their diesel counterparts.
Bobcat’s T7X compact track loader holds the unique position as the first all-electric machine of its type; its battery pack electrically powers both the drive of the machine and the work group. “Because of software, we’re able to tune a wider range of performance characteristics of the machine than you could traditionally with diesel-hydraulic,” noted Honeyman. “We can have different work modes, which saves on the battery and the battery pack, but we can also create what we call a ‘beast mode,’ where you get full instantaneous torque to the drive motors, and you can really go into the pile and get that work going.”
Ultimately, the proof is in the performance on the worksite. “Contractors who have been using the compact electric machines are first impressed with the power. These machines can do everything a diesel-powered unit can, so any hesitation about performance can be quickly resolved. And the torque is instant, so many operators have perceived the machines to have more power,” Arnold stated. “Second, they love the quiet operation, which allows others on site to easily communicate with the operator without yelling.
“Most of our electric compact equipment early adopters have been happily surprised with the power and performance of these machines,” he said. “So far, our biggest concern from customers has been charging. Owners want to know how long a charge will last in certain applications and how long it takes to recharge the units for the next task at hand.”
Run and charge times
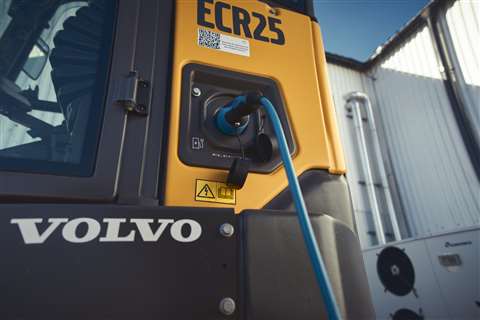
Bobcat electric machines have a stated run time of four hours, which is cause for pause for most any construction equipment owner. That’s why it’s essential to explain what that four hours means to the customer.
“Every time that you’re actuating the power of the machine and you’re moving the joysticks or working the work group or the drives or whatever, it’s consuming energy. Unlike a diesel machine, there’s no idle, so as soon as you let off the joysticks of an electric machine, it is not consuming energy or it’s consuming very, very little,” Honeyman explained.
“There’s this perception ‘well, I have to run eight hours and your battery only lasts four,’” he continued. “No, that’s four hours of active run time work. Most contractors are running four hours or less when you look at the hours of their current diesel-hydraulic machines.”
Education and operation are crucial in this case. “People have to drive it,” said Honeyman. “Experience and understand, ‘oh, I could do a full workday with this electric machine.’ Yeah, you sure can because it’s intermittent use – you’re in and out of the machine, you’re taking breaks and a lunch break. You’re doing other work… with other equipment. And all of a sudden, it’s an eight- to 10-hour day with that piece of equipment.”
“I think a big lesson the industry is learning is how to understand the actual duty cycle of equipment. People think they use a piece of equipment for eight or more hours a day. In reality, the actual run time where the equipment is working may be much less,” Moore said. “This is especially true with battery power when you no longer have idle time. Because of this, a piece of equipment may allow for a smaller battery than expected, making it a more cost-effective solution.
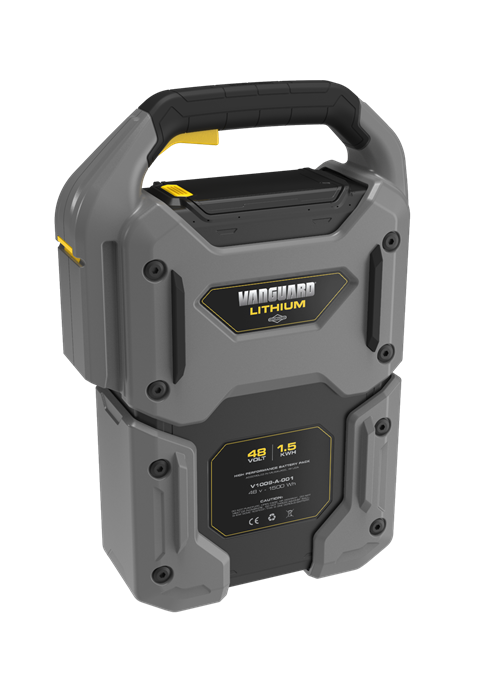
“We can work with OEMs to define true run time by building samples and getting them in customers’ hands to compile real usage data,” he continued. “We can then use that data to design the powertrain that will make the transition to electrification as easy and productive as possible.”
Charging time and availability of charging options is another common concern. “To have an optimal charging time for electric machines, it’s strongly recommended to have a 240 V, 32-amp, Level 2 AC-charging setup utilizing an SAE J1772 charging adapter or J plug – the same as for electric vehicles,” Arnold noted. “While you can charge the machines on a common household 120 V network, it takes longer.”
Fortunately, many contractors, especially those putting up larger structures, are roughing in the higher capacity power needed to efficiently charge battery electric equipment, said Honeyman. Some are also starting to utilize portable energy storage solutions on site.
Volvo CE offers a true off-grid solution, as well – a solar-powered fast charger from California-based Beam Global, which Arnold describes as an “no-connection, freestanding solar charger that has a battery pack similar to the size of the one inside the Volvo L25 wheel loader.” Other solutions will surely follow.
“We’ll continue to research, develop and provide a wider range of charging options in the coming months and years,” said Arnold. “As electric vehicles continue to roll out into the market, improved charging infrastructure will follow suit, which is also good news for the construction industry.”
Looking ahead
There will continue to be challenges for OEMs as they move further into electrification. Chief among them will be battery selection.
“Battery technology is constantly updating and becoming more efficient. So, as we develop and update electric machines, we want to make sure we’re utilizing the most up-to-date battery technology so the machinery is as efficient as possible,” said Graham.
“There’s certainly increasingly better battery technologies and better battery management,” Honeyman commented, including more environmentally friendly materials emerging out of the automotive sector. “We’re increasingly monitoring automotive – where they’re going with batteries, voltages, whatever it might be – and then those suppliers that can help us in the construction industry, as well.”
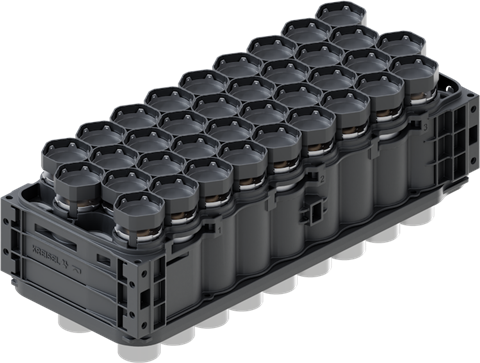
Proper battery selection, and sizing, will be essential to broader adoption, particularly in a market with little tolerance for unscheduled downtime. “Equipment with a high load and run time that is sized with too small a battery will be a dissatisfier,” Moore stated. “We work closely with OEMs to ensure they understand where and when it makes sense to incorporate battery power and how to do so effectively. With electrification, there isn’t a one size fits all solution…”
“Proper battery sizing and a deep understanding of how the vehicle is being used will be critical,” Preston agreed. “Packaging the power density will continue to be a challenge for OEMS and in some cases is going to require significant changes to the vehicle in order to accommodate the power storage. Looking ahead to the future, OEMs may need to reimagine their vehicle form and how their customers interact with the vehicle in order to find that perfect balance of performance and a great user experience.”
“When working in electrification, setting expectations is essential,” Moore concluded. “There are so many different options and factors OEMs need to weigh when designing an electrical system. When both the OEM and end user know what they are working to achieve with the electric equipment, and the performance they can expect, everyone is happier.”
STAY CONNECTED
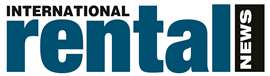


Receive the information you need when you need it through our world-leading magazines, newsletters and daily briefings.
CONNECT WITH THE TEAM
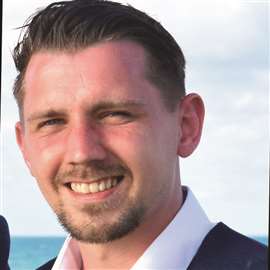
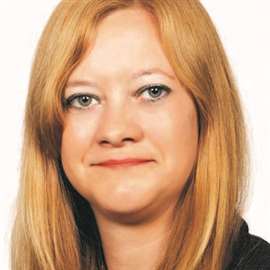
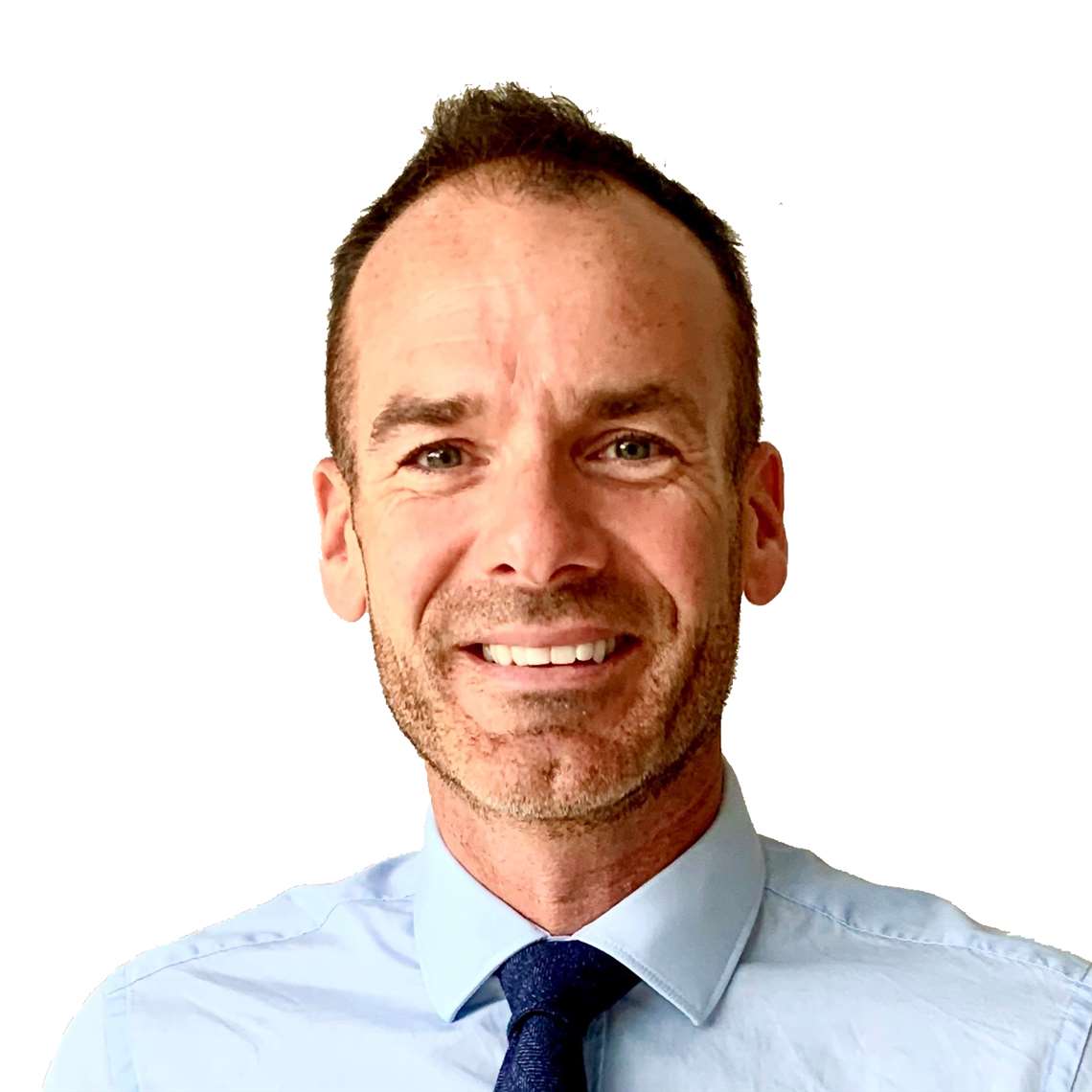