Electric or hydrogen? JCB says the answer depends on what - and where - you’re building
09 May 2025
JCB has sold more than 35,000 electric machines and has been developing its hydrogen internal combustion engine since 2021. Tim Burnhope, the company’s group director of special projects tells Power Progress International editor Julian Buckley why it expects both to power the construction machinery of the future.
When it comes to hydrogen-powered construction machines, UK manufacturer JCB is one of the most evangelical.
The company has been developing its hydrogen internal combustion engine since 2021 and recently drove an H2-powered backhoe loader past the Houses of Parliament and Buckingham Palace in central London to celebrate the UK government signing a ‘statutory instrument’ which allows hydrogen-fuelled construction and agricultural machinery to use public roads.
Yet for Tim Burnhope, the company’s group director of special projects, the case for investing in hydrogen or electric – powered equipment in the future is likely to depend on your geography as well as the sort of machinery you’re using.
“When it comes to hydrogen and rationalising the use case, you have to start with the job site and work back from there. The case for hydrogen is much more compelling from that perspective,” he says.
Hydrogen outside Europe
“The global population will be growing in regions outside Europe and unlike here, a lot of this growth will involve greenfield projects – there’ll be no infrastructure, no power cables. But what a lot of those countries have is solar power and that electricity can be used to produce hydrogen on the site.”
Burnhope points to global infrastructure projects such as Saudi Arabia’s Neom, where renewable electricity will be converted to hydrogen to power self-sustaining cities and where H2 could one day be as easy to get hold of for your JCB backhoe loader as diesel is today.

“That will work well in places like Saudi Arabia. But in Britain, where the sun doesn’t always shine and there’s not always any wind, stored renewable electricity can be used to produce green hydrogen to deliver power where and when it’s necessary,” he adds.
Different applications too, are likely to require different power sources, Burnhope predicts.
“I don’t say it’ll be one energy source or another across the entire industry, but we’re likely to see different energy sources for different applications, electric for compact machines, hydrogen for larger machines and perhaps biofuels for the very large mining and quarrying machines,” he says. “It’s all about using the right energy type to deliver what’s needed.”
JCB now offers nine electric models, including mini excavators, compact dumpers, and telehandlers. These are designed for urban and indoor environments, where noise and emissions must be kept to a minimum. The company has already sold more than 35,000 electric machines globally.
At the same time the company has also been developing its hydrogen internal combustion engine since 2021 and has designed the engine in such a way that it can easily switch to producing it at its production facilities.
The same production set up
The engine can be built in any sequence and in any volume on the same assembly line as the company’s 55 kW four-cylinder diesel units on which it is based. This means machines like backhoe loaders can be fitted with either diesel or hydrogen engines without changing the production setup.
“It’s very similar to engine manufacturing. Where we are producing backhoe loaders, instead of dropping in a traditional diesel engine and fuel tank the machines can be fitted with a hydrogen pressure tank, the fuel delivery system and the H2 engine on the same line,” says Burnhope.
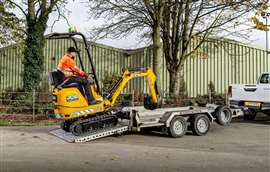
When it comes to larger equipment, battery-electric technology still presents major cost and logistical hurdles.
“It all sounds very good, having the capability to recharge in an hour. But sometimes you can’t get power delivered at that level, plus you need a pretty heavy cable to support charging at those rates,” Burnhope says. “That’s when you end up with diesel generators on site, which defeats the objective.”
For instance, running a 20-tonne electric excavator requires up to 400 kWh of batteries. That means frequent swaps using trucks, extra operators, and charging infrastructure—sending costs skyrocketing.
“A 20-tonne electric excavator can have between 200 and 400 kWh of batteries,” Burnhope adds. “One scenario we’ve modelled is where you have a machine like this that supports battery swapping, but you need a 16-tonne truck to carry the eight tonnes of batteries to and from where they’re charged. Plus you need another set of batteries on charge and at least two operators. Including the cost of the excavator, you could be looking at around £1 million [US$1.3 million], where a diesel version of the same machine is about £150,000 [US$200,100].”
For rental companies, which rarely benefit from the lower fuel costs of electricity over diesel, it is difficult to make that kind of outlay stack up financially.
Depreciation and battery lifecycle
Burnhope also flags long-term concerns about depreciation and battery life cycle.
“Residuals are important. And that is impacted by the expected number of recharging cycles. For mini electric machines, those batteries will last a long time. For larger machines, prospective customers are asking if they will need to buy new lithium batteries in 10 years and that would be expensive,” he says.
“That’s part of why lead-acid batteries were historically popular: “The batteries didn’t offer a great runtime, and they would wear out, but they were cheap to replace.”
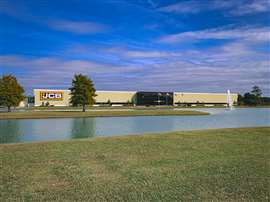
JCB’s appetite for hydrogen is one of the reasons the company chose to open a new production facility in Texas, a state which has made recent investments to support large-scale hydrogen production.
In 2024, JCB announced that it had acquired 400 acres of land in San Antonio, Texas on which it planned to build a new 500,000 square foot plant to boost its production of machines for the US market.
The new plant was always meant to produce machines for the North American market, but with the Trump administration announcing new trade tariffs on imports to the US, in April JCB said it would double the size of the facility, which is currently under construction to a million square feet.
“It’s really exciting!” said Burnhope. “We were already working on the facility, the planning and where to position different functions. But based on the policy direction in the United States, we might have to consider increasing the size of the plant again.”
STAY CONNECTED
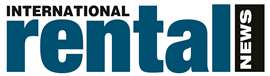


Receive the information you need when you need it through our world-leading magazines, newsletters and daily briefings.
CONNECT WITH THE TEAM
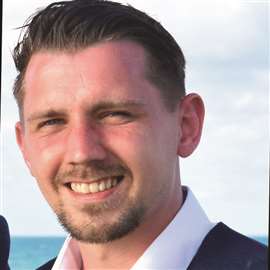
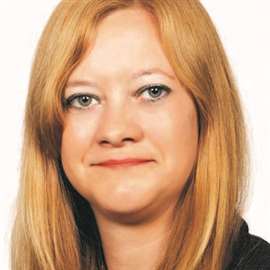
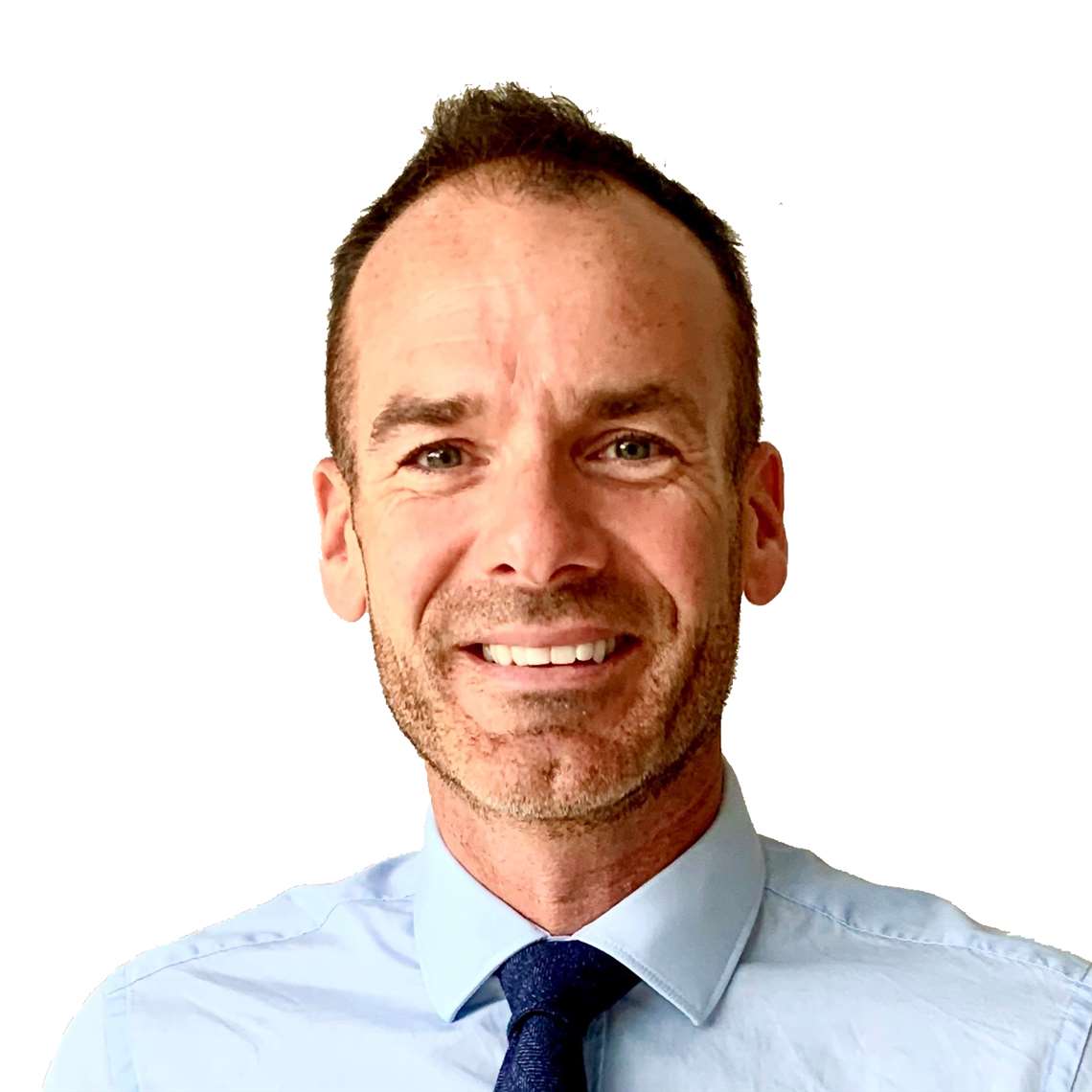